What is the Maximum Pressure for an ISO Tank?
ISO tanks, or ISO tank containers, are standardized containers designed for the transportation of liquids and gases. Their robust construction allows them to handle a variety of substances, ranging from chemicals and fuels to food-grade liquids. Given their critical role in global trade and logistics, understanding the maximum pressure that an ISO tank can safely endure is crucial for ensuring both safety and efficiency in transport.
Understanding ISO Tanks
ISO tanks are built to international standards set by the International Organization for Standardization (ISO). These tanks typically consist of a cylindrical steel container encased within a framework that conforms to ISO dimensions. The steel tank, known as the tank shell, is engineered to withstand substantial stresses during transportation and handling. The construction of ISO tanks ensures compatibility with standard shipping, rail, and road transportation methods.
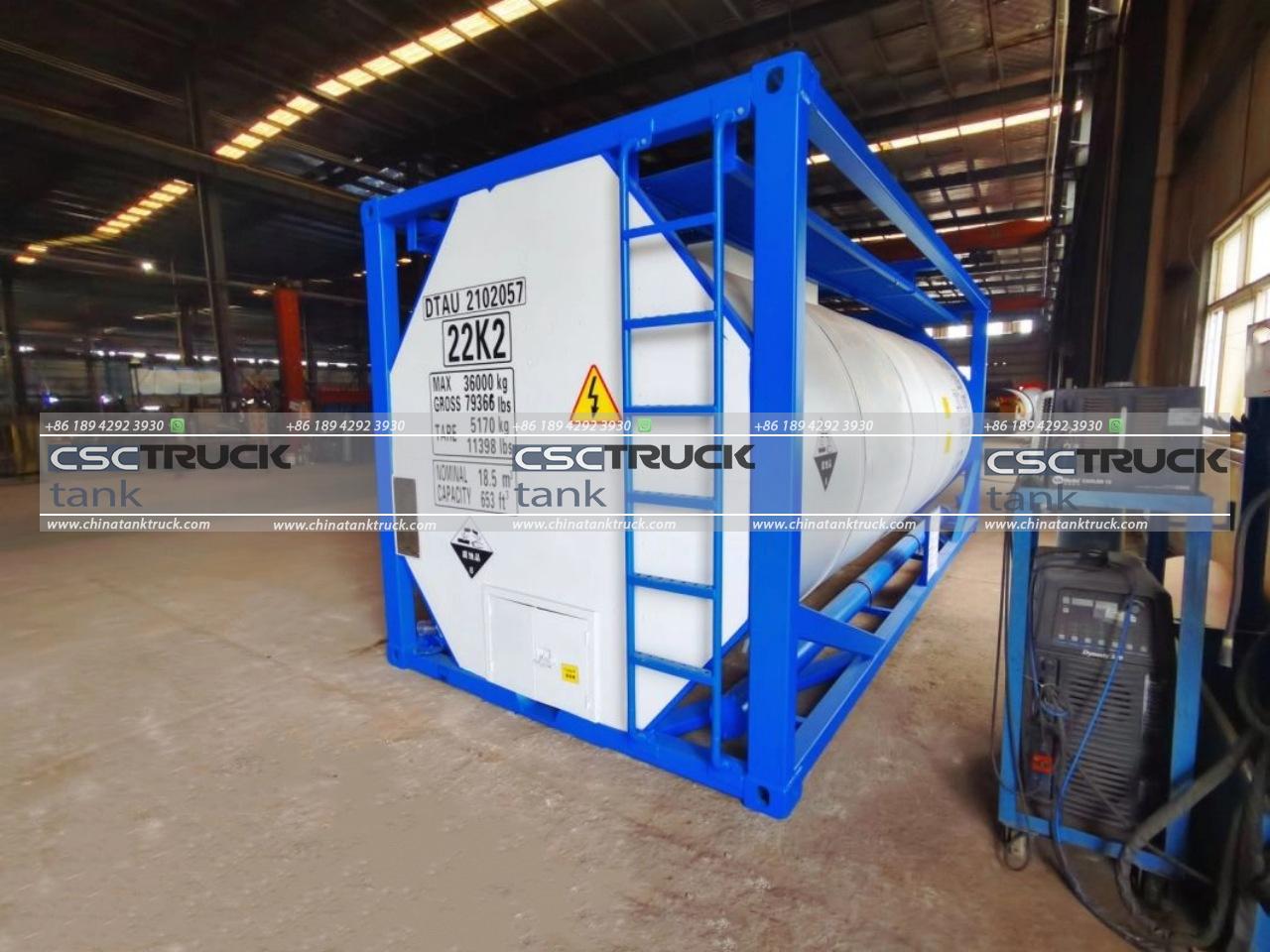
Pressure Ratings and Design Standards
ISO tanks come with specific pressure ratings determined by their design and the materials used in their construction. The pressure rating is a critical factor in determining the types of substances that can be safely transported. These ratings are dictated by both international standards and the regulations of the countries through which the tanks will travel.
Types of ISO Tanks and Their Pressure Limits
1. Non-pressure tanks:Â These tanks are designed for the transportation of liquids at atmospheric pressure. The standard maximum allowable pressure for these tanks is usually around 0.5 bar (7.25 psi). They are commonly used for substances that do not require containment under high pressure, such as water or certain chemicals.
2. Pressure Tanks:Â Designed for substances that need to be transported under pressure, these tanks are built to handle pressures significantly higher than atmospheric levels. The maximum pressure for these tanks typically ranges from 4 to 6 bar (58 to 87 psi). Pressure tanks are used for substances such as liquefied gases and pressurized chemicals.
3. Cryogenic Tanks:Â These tanks are specifically engineered for extremely low-temperature substances, such as liquefied natural gas (LNG) or liquefied oxygen. Cryogenic tanks operate under pressures of about 1 to 2 bar (14.5 to 29 psi), but they must maintain very low temperatures to keep the substances in a liquid state.
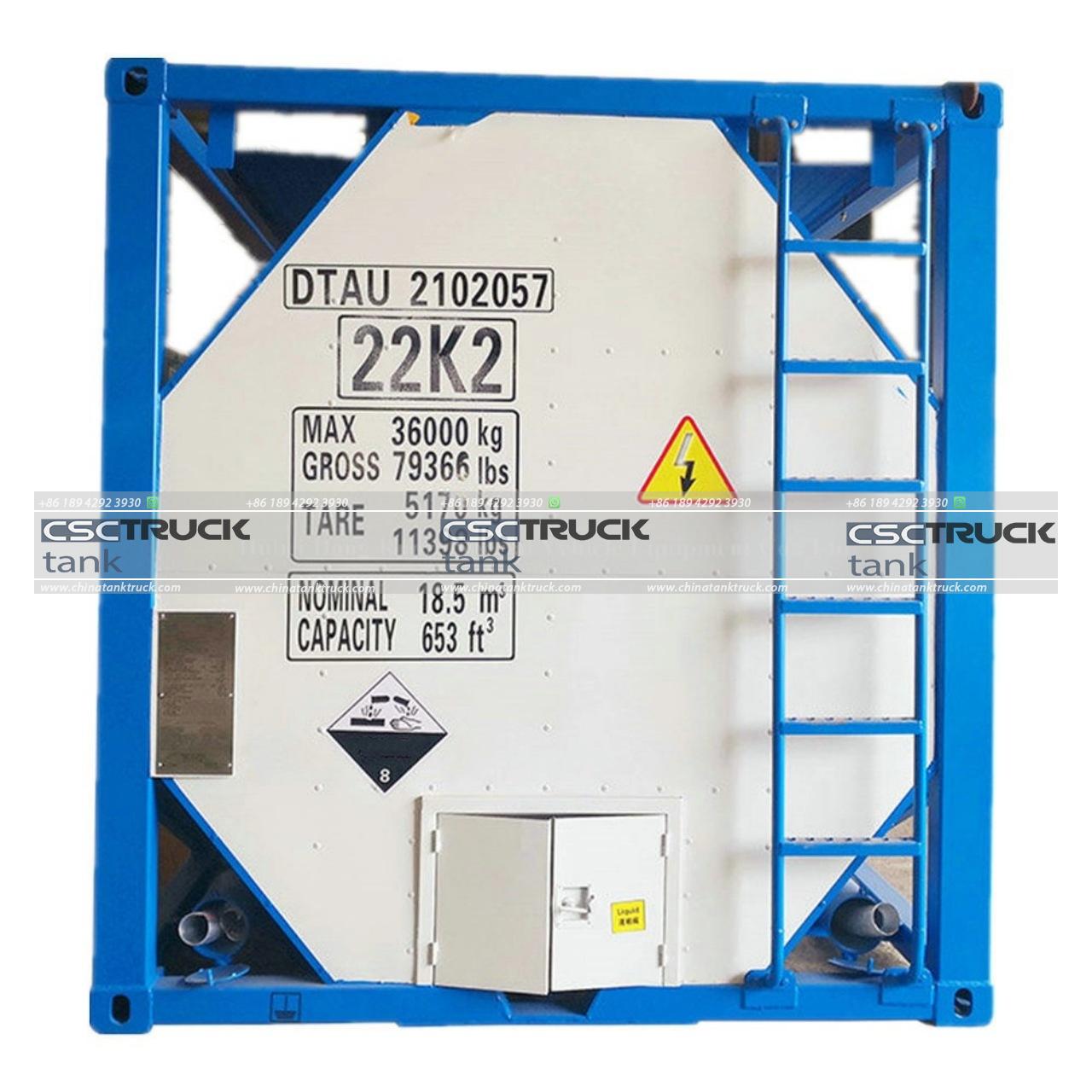
Factors Affecting Maximum Pressure
Several factors influence the maximum pressure that an ISO tank can handle, including:
1. Material Strength:Â The steel or alloy used in the construction of the tank plays a critical role in determining its pressure tolerance. High-strength materials can withstand higher pressures, ensuring safety during transport.
2. Tank Design:Â The design of the tank, including its thickness, weld quality, and overall construction, impacts its pressure rating. Tanks are tested and certified according to international standards to ensure they meet safety requirements.
3. Regulatory Standards:Â Different countries and regions have varying regulations regarding the pressure ratings of ISO tanks. These regulations ensure that tanks meet specific safety standards and are suitable for their intended use.
4. Temperature Conditions:Â Temperature can affect the pressure inside an ISO tank. For instance, higher temperatures can increase the pressure of gases, while lower temperatures can decrease the pressure. ISO tanks are designed to handle a range of temperatures, but extreme conditions can impact their pressure ratings.
Safety Considerations
Safety is paramount in the transportation of pressurized substances. ISO tanks are equipped with several safety features to prevent accidents and ensure secure handling:
1. Pressure Relief Valves:Â These valves are essential for releasing excess pressure and preventing overpressure situations. They are calibrated to open at specific pressure levels to maintain safety.
2. Pressure Gauges:Â Pressure gauges provide real-time monitoring of the internal pressure of the tank, allowing operators to ensure that the pressure remains within safe limits.
3. Safety Certifications:Â ISO tanks must undergo rigorous testing and certification processes to verify their pressure tolerance and overall safety. Certifications ensure that tanks comply with international and local regulations.
4. Inspection and Maintenance:Â Regular inspection and maintenance of ISO tanks are critical to ensuring their safe operation. This includes checking for signs of wear, corrosion, or other issues that could affect their pressure tolerance.
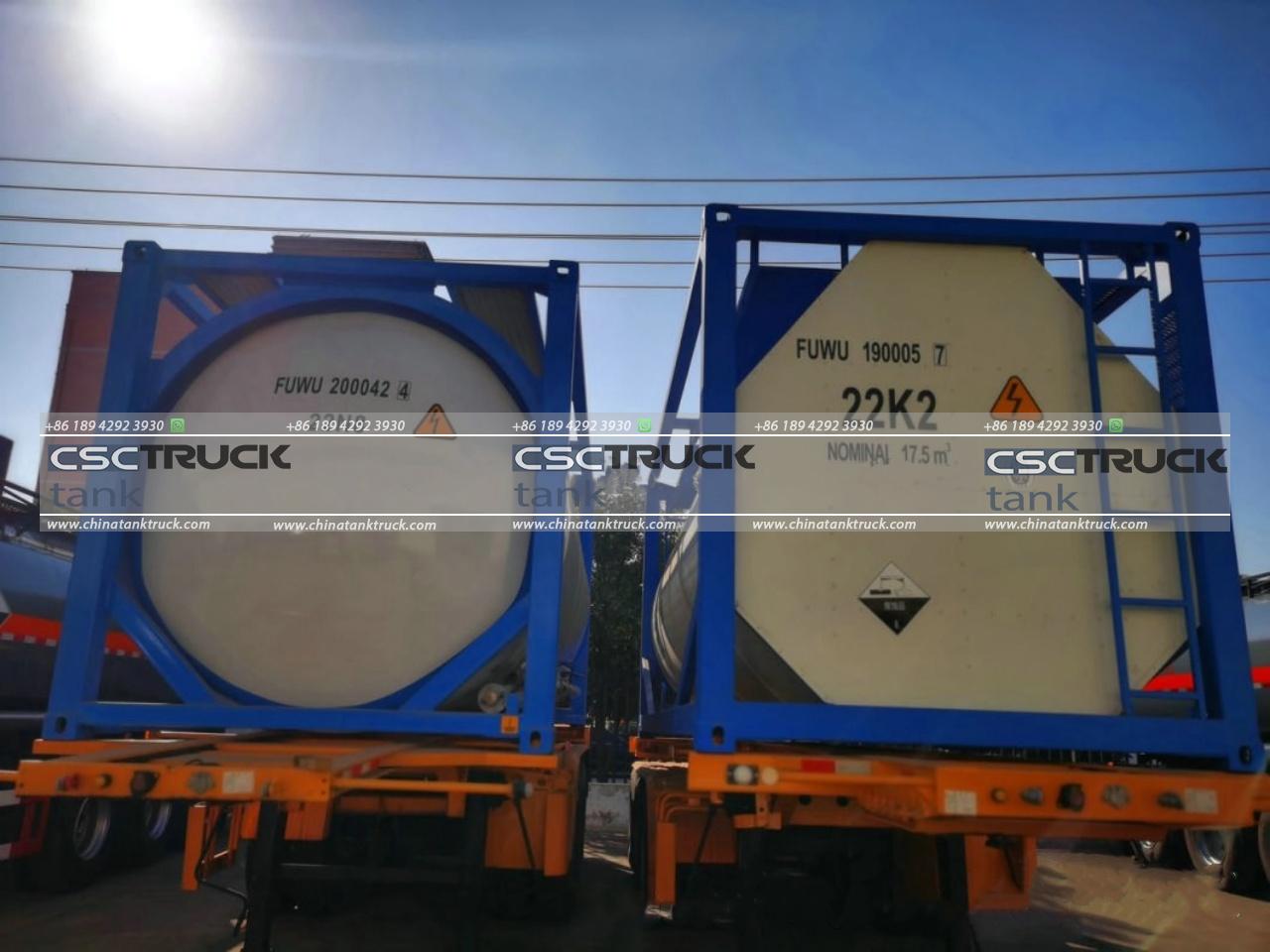
Conclusion
The maximum pressure for an ISO tank depends on the type of tank and its intended use. Non-pressure tanks handle atmospheric pressure, pressure tanks are designed for higher pressures, and cryogenic tanks operate under specific conditions for low-temperature substances. Understanding these pressure limits is essential for selecting the appropriate ISO tank for transporting different types of liquids and gases.
ISO tanks play a vital role in global logistics, and their design and construction are engineered to meet stringent safety and regulatory standards. By adhering to these standards and regularly maintaining tanks, transporters can ensure the safe and efficient movement of substances across various modes of transportation.