What is the Lifespan of an ISO Tank?
ISO tanks are an integral part of the global supply chain, providing a reliable, efficient, and safe means for transporting liquids, gases, and powders across countries and continents. From chemicals to food-grade products, ISO tanks are indispensable for industries ranging from manufacturing to agriculture. But how long can these specialized containers serve before they need to be decommissioned? The lifespan of an ISO tank is a topic of considerable importance, particularly for logistics operators, environmental safety regulators, and businesses that depend on seamless transportation. In this article, we will delve into the factors that determine the lifespan of an ISO tank, the maintenance requirements that can extend its service life, and the regulatory frameworks that govern its usage.
What is an ISO Tank?
Before discussing its lifespan, it’s essential to understand what an ISO tank is. ISO tanks are large, cylindrical, stainless steel containers designed according to the International Organization for Standardization (ISO) standards. These tanks are typically used for transporting liquids, gases, and even some solids in bulk quantities. They are mounted inside a steel frame that conforms to the ISO dimensions, allowing for easy transportation via various modes, including ships, trucks, and trains.
The design of an ISO tank makes it particularly robust and well-suited to handle the rigors of international shipping. Typically made from high-quality stainless steel, these tanks are resistant to corrosion, ensuring they can safely transport a variety of chemicals or other hazardous materials.
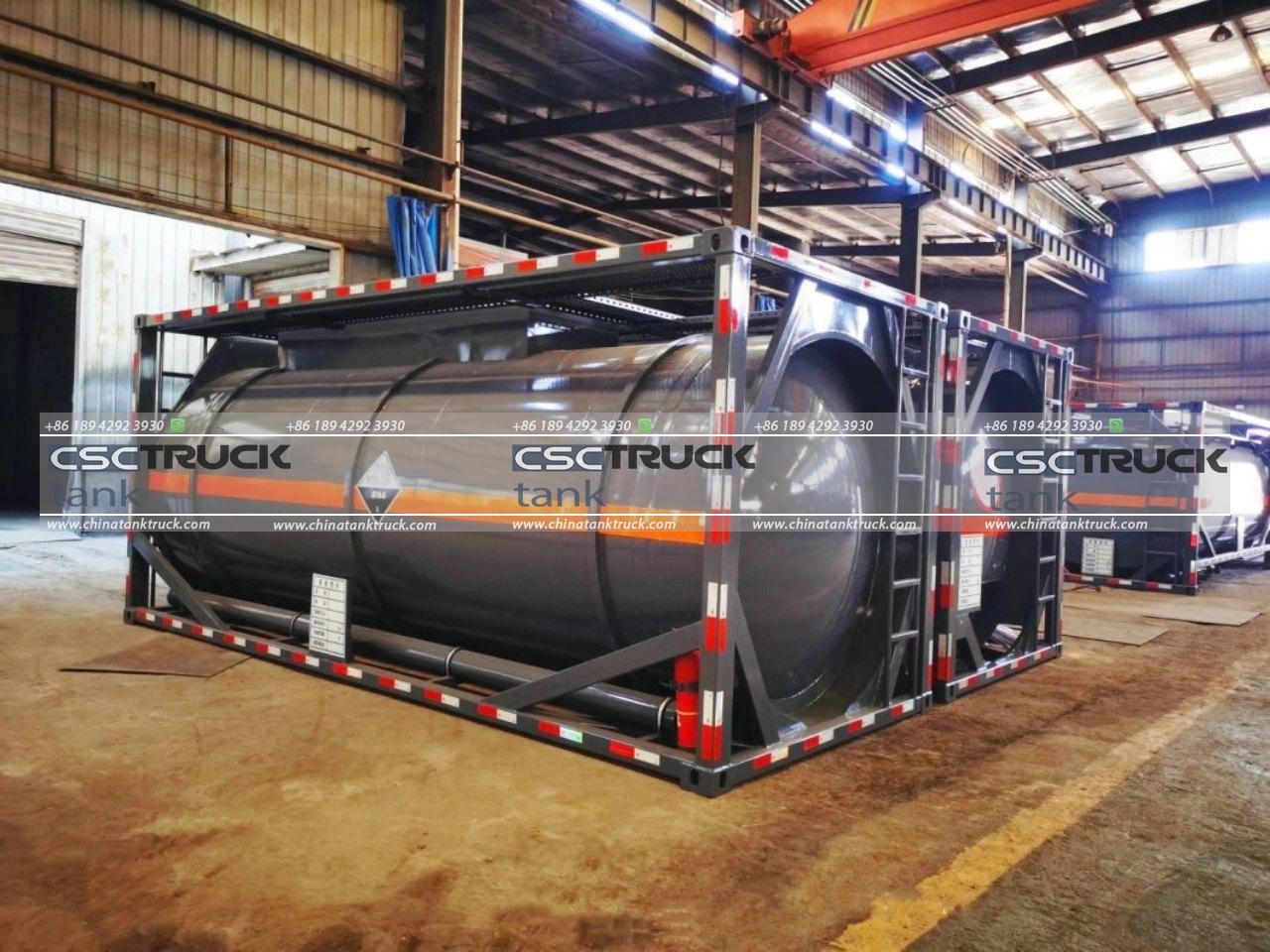
Average Lifespan of an ISO Tank
The average lifespan of an ISO tank ranges from 15 to 25 years, depending on several factors such as material quality, maintenance routines, and operating conditions. Some ISO tanks may last longer with rigorous care and consistent inspection, while others may need to be retired earlier due to wear and tear or regulatory requirements.
Several factors impact an ISO tank’s longevity:
1. Material of Construction: Most ISO tanks are constructed using stainless steel, which is durable, corrosion-resistant, and capable of withstanding the harsh conditions often encountered during transportation. However, the grade of stainless steel used can affect the tank’s lifespan. Higher-quality materials tend to offer longer durability, especially when transporting corrosive substances.
2. Type of Cargo: The nature of the cargo transported by the ISO tank plays a significant role in its longevity. Corrosive chemicals, for example, can lead to faster degradation of the tank’s inner walls. Gases that require high-pressure containment may also exert additional strain on the structural integrity of the tank over time. Food-grade tanks, used for transporting edible liquids, may have different lifespan requirements, as they must meet stricter hygiene standards.
3. Usage Frequency: ISO tanks that are frequently used or in particularly harsh environmental conditions will experience more wear and tear than those used occasionally. Tanks regularly exposed to extreme temperatures, humidity, or corrosive marine environments may not last as long as those in more controlled conditions.
4. Handling and Transportation: The way ISO tanks are handled during transportation also contributes to their lifespan. Proper loading, securing, and unloading of tanks minimize stress on the tank’s frame and structure, extending its operational life. Conversely, rough handling or accidents during transport can significantly reduce the tank’s useful life.
5. Maintenance and Inspections: ISO tanks that undergo regular inspections and maintenance can last significantly longer than those that are neglected. Maintenance involves cleaning the tank’s interior to prevent residue buildup, checking for signs of corrosion, and ensuring the structural integrity of the tank’s frame and shell. Inspections, often mandated by regulatory agencies, help identify potential issues before they become serious enough to warrant retiring the tank.
Regulatory Standards and Testing
ISO tanks are subject to stringent regulatory standards and testing throughout their lifecycle. These regulations help ensure the safe operation of the tanks and protect both the environment and the operators handling them. For example, in many countries, tanks must undergo periodic inspections every 2.5 to 5 years, depending on the cargo they carry and the mode of transportation used.
Types of Inspections:
1. Periodic Inspections: These are conducted at regular intervals, typically every 2.5 years. They include a thorough examination of the tank’s exterior, and checking for signs of corrosion, cracks, or other structural issues. The tank’s internal structure is also inspected for contamination, wear, or damage.
2. Hydraulic Pressure Test: During this test, the tank is filled with water and pressurized to check for leaks. This ensures that the tank can withstand the internal pressure exerted by gases or liquids under transport.
3. Leakage Testing: For tanks carrying hazardous gases or high-pressure liquids, leak testing is crucial. Any detected leaks would lead to immediate decommissioning or repair, as leaks could lead to environmental hazards or catastrophic failure during transport.
4. Ultrasonic Thickness Testing: This non-destructive test measures the thickness of the tank’s walls, which can help detect areas of corrosion or metal fatigue that might not be visible to the naked eye. A decrease in wall thickness over time can be a key indicator that the tank is nearing the end of its useful life.
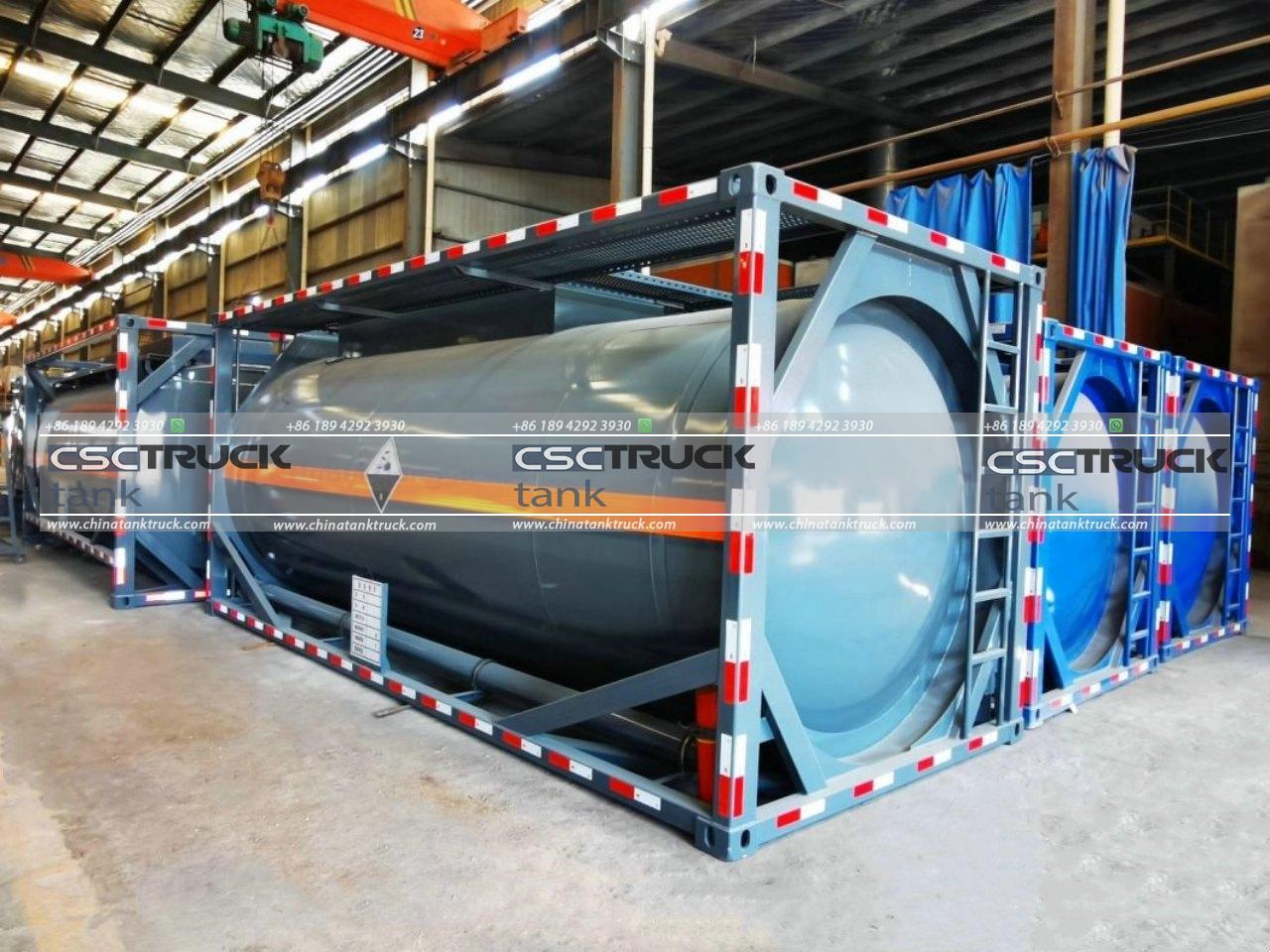
Extending the Lifespan of an ISO Tank
While the average ISO tank may last 15 to 25 years, there are steps operators can take to maximize its operational life. Proper maintenance, cleaning, and adhering to best practices in handling and transportation can significantly extend a tank’s lifespan. Here are some strategies for keeping an ISO tank in good working condition for as long as possible:
1. Regular Cleaning: Residual cargo, especially corrosive substances, can eat away at the tank’s inner surface over time. Regular cleaning ensures that no harmful substances linger inside the tank and that it’s safe to transport other materials.
2. Protective Coatings: Applying specialized coatings or linings inside the tank can help prevent corrosion, particularly when transporting aggressive chemicals. These coatings form a barrier between the tank’s metal and the cargo, reducing wear and tear.
3. Storage Conditions: ISO tanks should be stored in dry, sheltered environments when not in use. Prolonged exposure to harsh weather conditions, such as extreme heat, cold, or humidity, can accelerate corrosion and structural degradation.
4. Prompt Repairs: Addressing small issues early can prevent them from becoming significant problems later. For example, minor leaks, dents, or signs of rust should be repaired immediately to prevent further deterioration.
5. Load Management: Overloading an ISO tank or exposing it to improper loading techniques can cause undue stress on its frame and structure, shortening its operational life. Proper load management, including evenly distributing the cargo, is crucial for ensuring the tank’s longevity.
Conclusion
The lifespan of an ISO tank depends on various factors, including the material quality, the type of cargo it carries, the frequency of use, and the level of maintenance it receives. While the average lifespan ranges from 15 to 25 years, regular maintenance and adherence to safety protocols can significantly extend a tank’s operational life. By investing in high-quality tanks, conducting regular inspections, and taking steps to protect the tank from corrosion and structural damage, operators can ensure that their ISO tanks remain safe, efficient, and reliable for as long as possible.
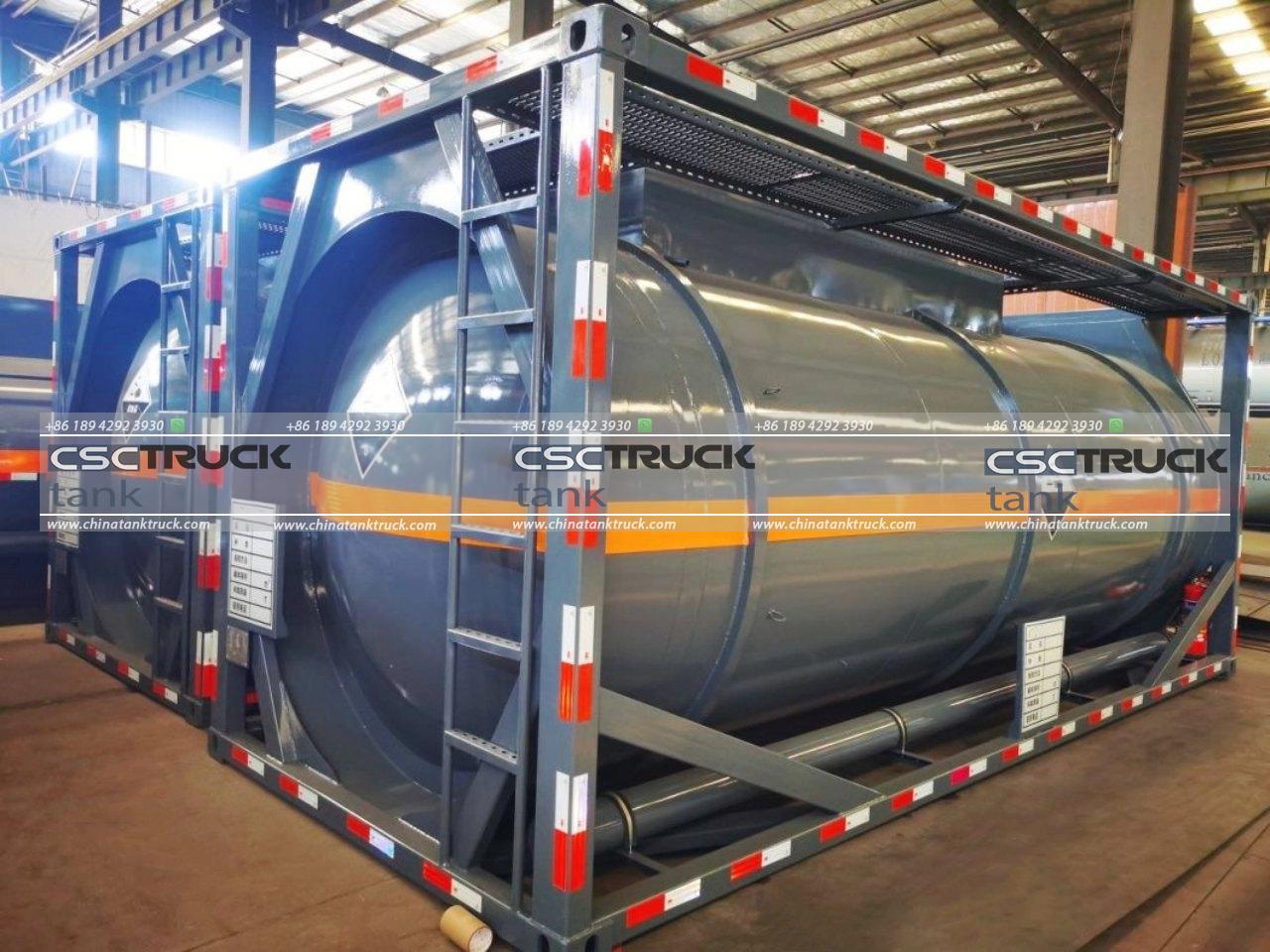