What is a Pressurized Tank Used For?
A pressurized tank is a specialized container designed to hold and maintain a specific level of pressure inside, usually higher than the surrounding atmospheric pressure. These tanks serve a wide range of applications across various industries, such as manufacturing, energy, chemical processing, and water treatment. The use of pressurized tanks is vital to ensuring the safe storage, transportation, and handling of gases, liquids, and other materials that require specific pressure levels to maintain their properties or prevent unwanted reactions. In this article, we’ll explore the essential uses of pressurized tanks, their types, components, and how they function in different sectors.
1. Storage of Compressed Gases
One of the most common uses for a pressurized tank is the storage of compressed gases. Gases like oxygen, nitrogen, hydrogen, and propane are often stored at high pressure because they occupy much less space in compressed form. For industries such as medical facilities, laboratories, and manufacturing, these gases are essential for processes like welding, sterilization, and chemical reactions.
For example, oxygen is stored in pressurized tanks in hospitals for use in life-support systems and portable oxygen systems for patients with respiratory conditions. Similarly, pressurized hydrogen tanks are crucial for hydrogen-powered vehicles and fuel cells, where hydrogen needs to be stored safely until it’s used to produce electricity.
Benefits:
– Space efficiency: Storing gases at high pressures allows for the transportation of larger amounts in smaller volumes.
– Safety: Special materials and designs help ensure that gases remain securely stored without leaks or the risk of explosion.
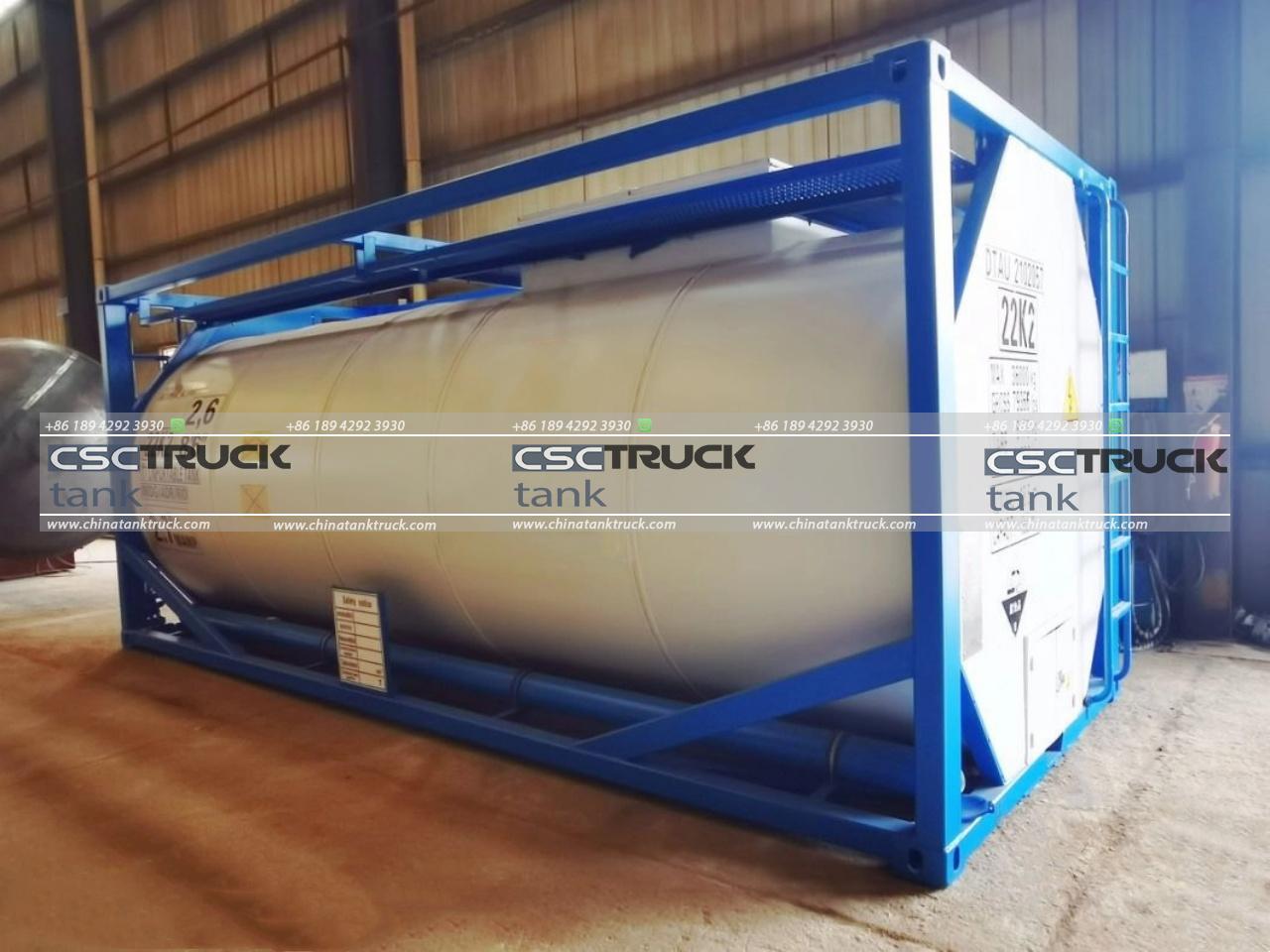
2. Water Treatment and Supply Systems
In water treatment plants and distribution systems, pressurized tanks play a key role in storing and regulating the flow of water. These tanks are often used as **water pressure booster systems**, ensuring that water is supplied to residential, commercial, and industrial buildings at a constant pressure. The tanks maintain adequate pressure even during periods of high demand, ensuring that water reaches taps and equipment efficiently.
Pressurized water storage tanks are often installed in homes that use well water. The well pump fills the tank with water, and the pressure in the tank pushes the water through the plumbing system to fixtures such as faucets, showers, and toilets. This ensures that the well pump does not need to run continuously, saving energy and reducing wear on the system.
Benefits:
– Energy conservation: Pressurized tanks reduce the need for constant pumping in water systems.
– Reliable supply: Helps ensure a consistent flow and pressure, even during peak usage times.
3. Fire Suppression Systems
In firefighting, pressurized tanks are an integral part of **fire suppression systems**. These tanks store and release firefighting agents, such as water, foam, or dry chemicals, under pressure. For example, a pressurized water tank connected to a fire sprinkler system can deliver water instantly when the system detects a fire.
Similarly, fire trucks are equipped with pressurized tanks that store water and other firefighting agents. These tanks ensure that water is delivered at the right pressure to reach the fire, even when hydrants or other water sources are not immediately available.
Benefits:
– Instant activation: The pressurized tanks can immediately release firefighting agents to control or extinguish fires quickly.
– Portability: Firefighting tanks can be mobile, installed on fire trucks, or part of sprinkler systems, making them highly versatile in different settings.
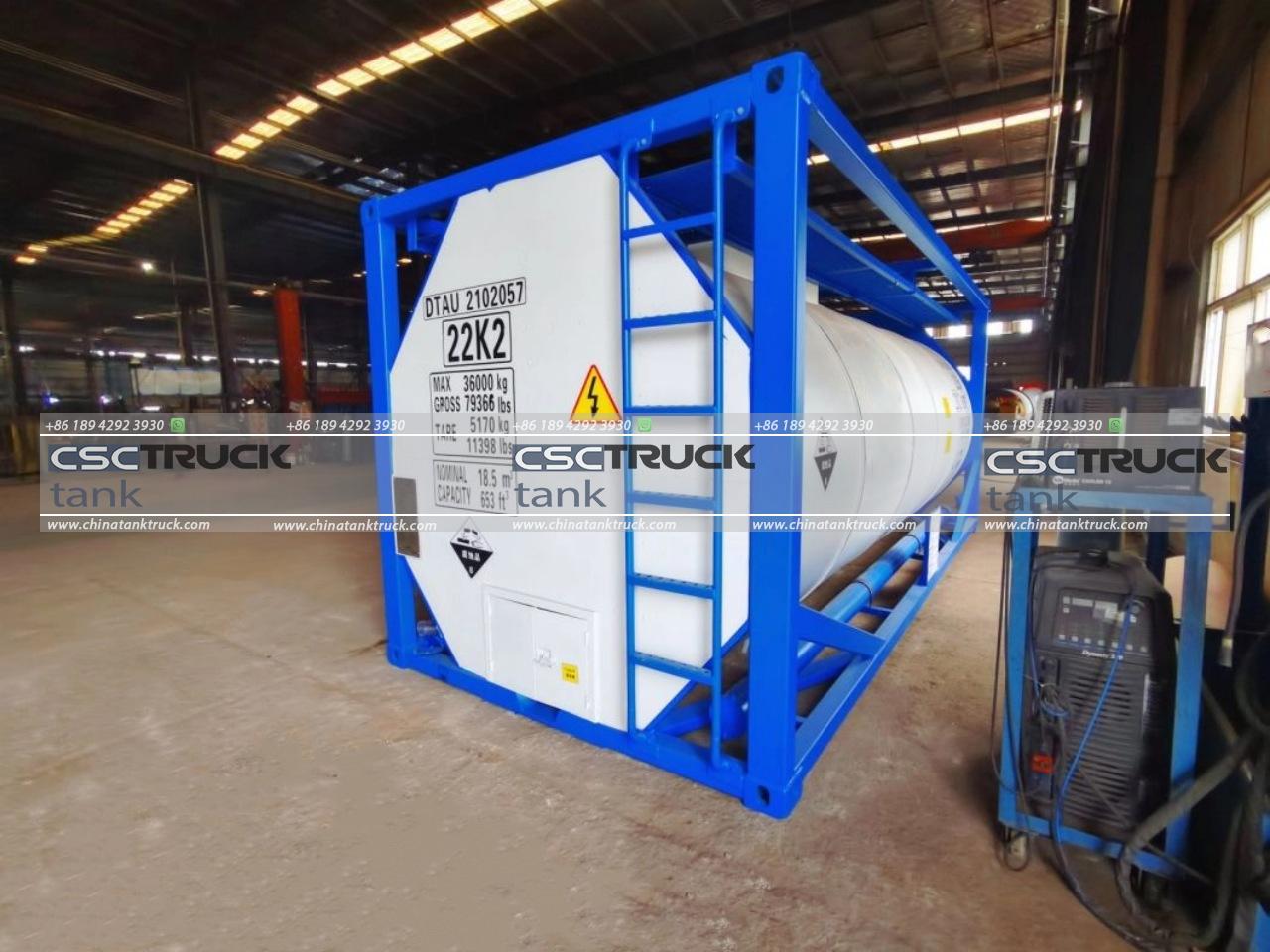
4. Chemical Processing and Industrial Manufacturing
In chemical processing plants, pressurized tanks are used to store and process volatile or reactive chemicals that need to be kept under controlled pressure conditions. For instance, in the oil and gas industry, these tanks store raw materials like crude oil, natural gas, and liquefied petroleum gas (LPG) under high pressure.
In other industries, like pharmaceuticals, these tanks can be used for blending, mixing, and reacting chemical substances under specific pressure conditions. Some industrial processes require high-pressure environments to promote or accelerate chemical reactions.
Benefits:
– Safety: Pressurized tanks are designed to withstand extreme conditions, reducing the risk of explosions or chemical spills.
– Controlled environments: They enable precise control over the pressure, temperature, and other factors during chemical processes.
5. Cryogenic Storage
Pressurized tanks are essential for the storage of cryogenic materials, such as liquefied natural gas (LNG), liquid nitrogen, and liquid oxygen, at very low temperatures. These tanks maintain both the temperature and pressure necessary to keep these substances in their liquid form. For example, liquid nitrogen is widely used in medical and scientific applications, from cryopreservation of biological samples to cooling MRI machines.
These cryogenic tanks are built with insulating materials and pressure control mechanisms to prevent heat from entering the tank, which would cause the liquid inside to evaporate and increase pressure. In cases where the pressure rises too high, relief valves or venting systems are used to release gas safely.
Benefits:
– Efficient storage: Liquefied gases take up far less space than their gaseous forms, allowing for more efficient storage and transportation.
– Temperature control: Pressurized cryogenic tanks maintain the necessary conditions for storing materials at extremely low temperatures.
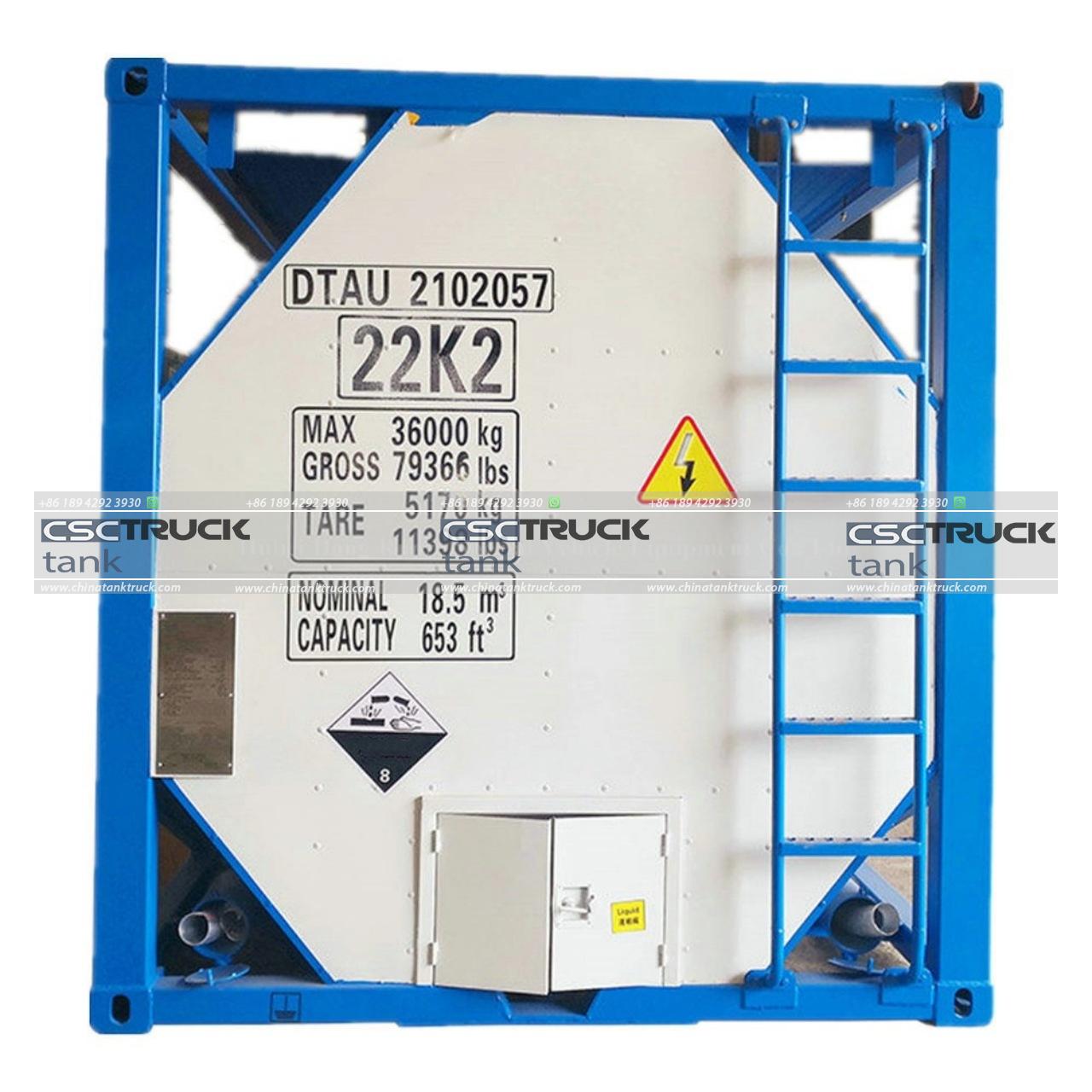
6. Energy Storage Systems
Pressurized tanks are increasingly being used in energy storage systems, especially in compressed air energy storage (CAES). In these systems, excess electrical energy generated during periods of low demand is used to compress air and store it in pressurized tanks or underground caverns. When demand for electricity increases, the compressed air is released and used to drive turbines that generate power.
This form of energy storage is particularly useful for balancing the supply and demand of renewable energy sources, such as wind and solar power, which can be intermittent. By storing energy in pressurized air, CAES systems provide a way to store large amounts of energy and release it when needed.
Benefits:
– Grid stabilization: Pressurized tanks can store surplus energy and release it during peak demand, improving grid reliability.
– Renewable energy integration: These systems help manage the variability of renewable energy sources by providing energy storage solutions.
7. Hydraulic and Pneumatic Systems
Pressurized tanks are also key components in hydraulic and pneumatic systems, where they store fluids or gases at high pressure to power machinery. In hydraulic systems, for example, a pressurized tank may hold hydraulic oil that powers pistons and other mechanical devices. In pneumatic systems, pressurized air stored in tanks is used to drive pneumatic tools, such as drills, wrenches, and hammers.
These systems are widely used in construction, manufacturing, and aerospace industries due to their efficiency and reliability. The ability to store and release high-pressure fluids or gases on demand allows for precise control over mechanical movements.
Benefits:
– Power on demand: Pressurized tanks provide a consistent source of high-pressure fluids or gases to operate machinery.
– Durability: These systems are designed for heavy-duty applications, often requiring minimal maintenance.
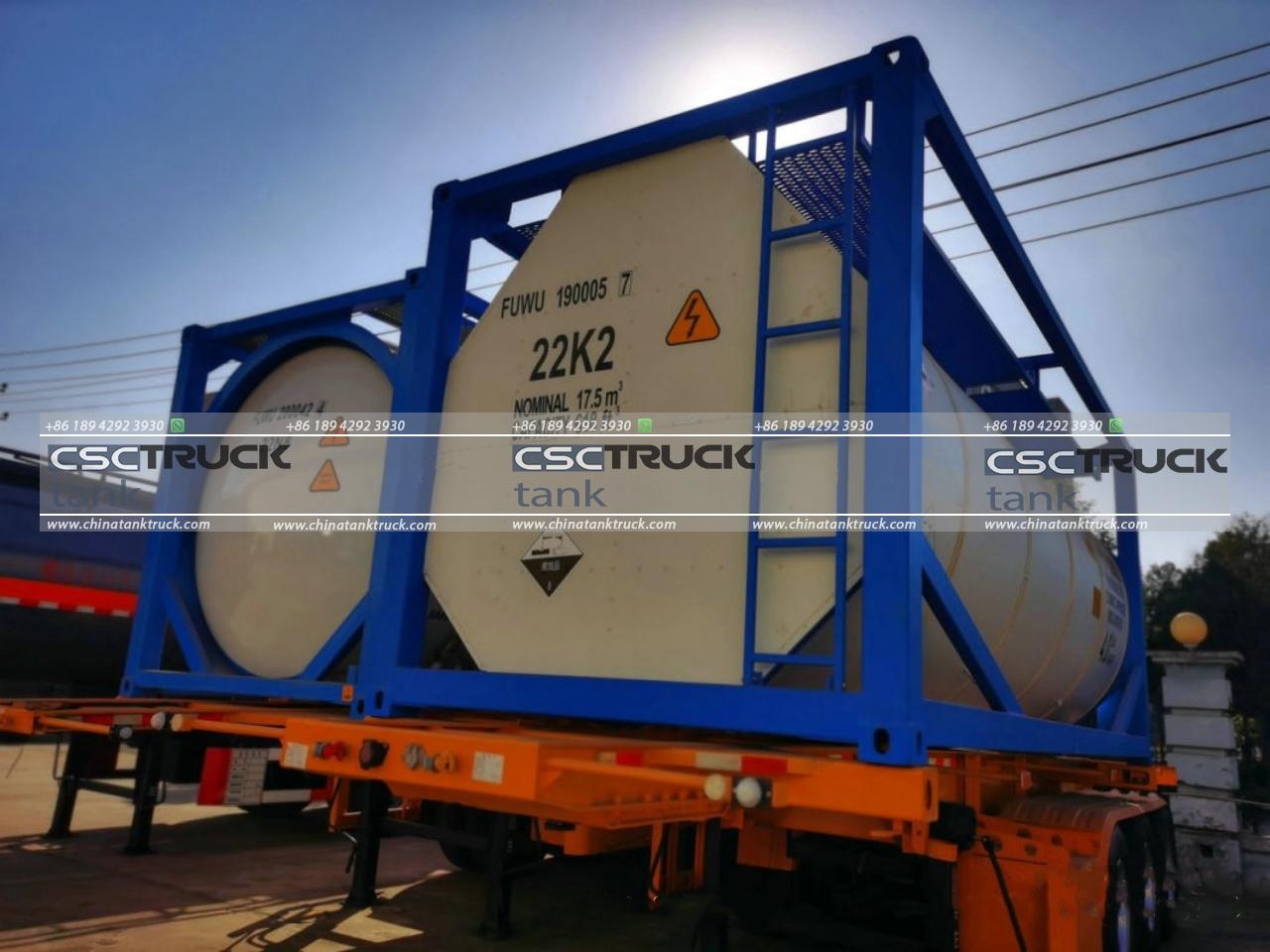
Conclusion
Pressurized tanks are indispensable across various industries due to their ability to safely store and regulate gases, liquids, and chemicals at high pressures. From ensuring a steady supply of water and energy to powering industrial processes and firefighting efforts, these tanks provide vital support in many critical applications. Their designs and materials are tailored to withstand the demands of different substances and operating environments, ensuring safety, efficiency, and reliability.