Milk Tank Trucks: Hygienic and Insulated Solutions for Dairy Transport
Milk tank trucks are essential in the dairy industry, facilitating the safe and efficient transport of raw milk from farms to processing facilities. Given the perishable nature of milk, these trucks are engineered to maintain strict hygienic standards and thermal insulation to prevent spoilage and contamination. This article delves into how milk tank trucks operate as hygienic and insulated solutions for dairy transport, examining their structural features, materials, and maintenance practices.
1. The Critical Need for Hygienic Transport in Dairy
Milk is highly susceptible to bacterial contamination and spoilage. The journey from the farm to the dairy plant needs to be as short and clean as possible to ensure milk retains its freshness and nutritional value. Even minor exposure to external contaminants can degrade milk quality, leading to souring, the growth of pathogens, or the presence of off-flavors. Due to these risks, milk transport vehicles are required to meet rigorous cleanliness standards.
Countries around the world enforce stringent regulations on milk tank trucks. Regulatory bodies like the Food and Drug Administration (FDA) in the U.S. or the European Union‘s hygiene guidelines mandate that milk tanks are made of food-grade materials, are fully insulated, and adhere to sanitization protocols after each trip.
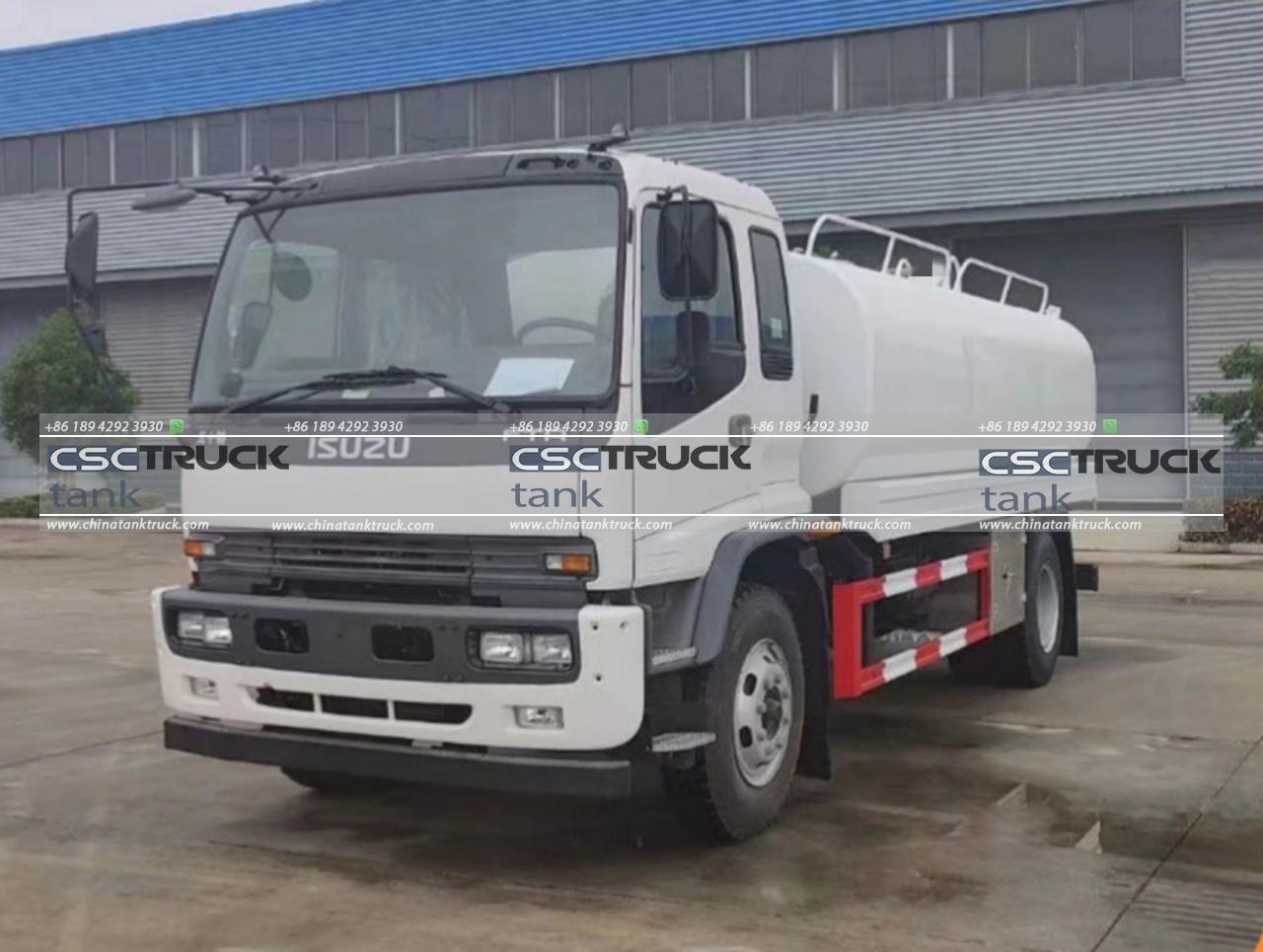
2. Key Structural Features of Milk Tank Trucks
Milk tank trucks are designed to maximize cleanliness and thermal stability. Here’s a breakdown of their key structural elements:
A. Stainless Steel Tanks
The interior of milk tank trucks is usually made of food-grade stainless steel. Stainless steel is chosen for several reasons: it’s resistant to corrosion, it’s easy to clean, and it doesn’t react chemically with milk, preserving the quality of the liquid. Most commonly, Type 304 or 316 stainless steel is used, as these alloys provide excellent durability and hygiene for dairy applications.
B. Insulation
Insulation is crucial in milk tank trucks to prevent temperature fluctuations. Milk needs to be kept cool (ideally around 4°C) to minimize bacterial growth. To maintain this temperature during transport, milk tanks are wrapped in thick layers of insulating material, typically polyurethane foam. This insulation prevents heat from penetrating the tank, ensuring that milk remains at a stable temperature for the duration of its journey.
C. Tank Shape and Compartmentalization
Milk tanks are cylindrical, which helps to reduce the risk of milk sloshing and aids in maintaining a balanced load while driving. Additionally, many trucks are divided into compartments. This compartmentalization allows for the transportation of different batches of milk, each collected from separate farms. It also minimizes the risk of cross-contamination and facilitates efficient unloading, as each compartment can be emptied independently.
3. Ensuring Hygiene: Cleaning and Sanitization Protocols
After every milk delivery, the tank must undergo thorough cleaning and sanitization to prevent bacterial build-up and ensure the next load remains uncontaminated. Here are some methods commonly used:
A. CIP (Cleaning in Place)
Most milk tank trucks are equipped with CIP (Cleaning in Place) systems, allowing for an automated cleaning process that doesn’t require disassembly. In a CIP system, high-pressure jets spray hot water mixed with detergent inside the tank, removing milk residues and killing bacteria. Following this wash, the system rinses the tank with clean water, ensuring that no soap or detergent remains. This method is efficient and complies with regulatory standards.
B. Hot Water and Chemical Cleaning
For deeper cleaning or after transporting multiple loads, chemical disinfectants are sometimes applied. These chemicals are often acidic or alkaline solutions that break down fats and proteins left by the milk, followed by a rinse to eliminate chemical residues. Steam cleaning may also be used to reach a high enough temperature to kill bacteria without requiring chemicals.
C. Routine Inspections and Swab Tests
Regular inspections are mandatory for milk trucks to ensure no residues are left in hard-to-reach areas. Swab tests are conducted after cleaning to check for bacteria or leftover milk proteins, confirming the cleanliness of the tank.
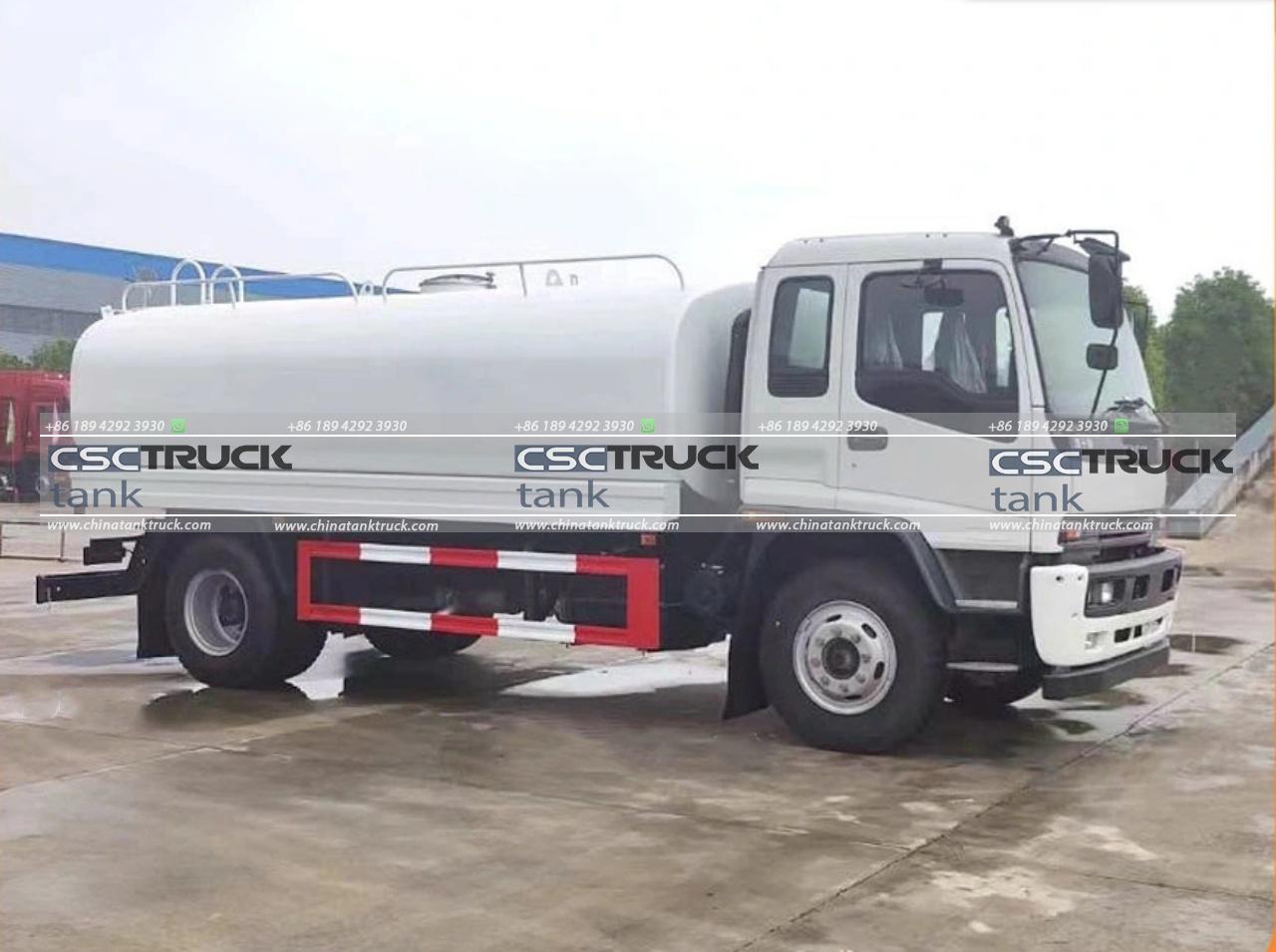
4. Advanced Insulation Technology: Keeping Milk Fresh
Modern milk tank trucks incorporate advanced insulation techniques to optimize temperature retention. Insulated milk tankers are often lined with multiple layers of high-density polyurethane foam between the stainless steel tank and the outer shell. This layer prevents heat from infiltrating the tank, keeping milk at a stable temperature even during lengthy transport.
In more extreme climates, some trucks are equipped with additional cooling systems. These may include ice banks or refrigerated coils, which are activated only if the temperature rises above acceptable levels. Such cooling measures offer an additional layer of protection in case of unexpected delays or breakdowns.
5. Monitoring and Tracking: Real-Time Temperature Control
Temperature monitoring is essential for maintaining milk quality. Modern milk tank trucks are equipped with sensors that measure the milk’s temperature in real time. These sensors are connected to a control panel in the driver’s cabin, where the driver can monitor temperature fluctuations and respond to any changes. Some trucks are also equipped with GPS-enabled tracking systems, allowing dispatch centers to monitor both the truck’s location and its temperature data. If the temperature begins to rise, alerts are sent, enabling the dispatch team to intervene or reroute the truck if necessary.
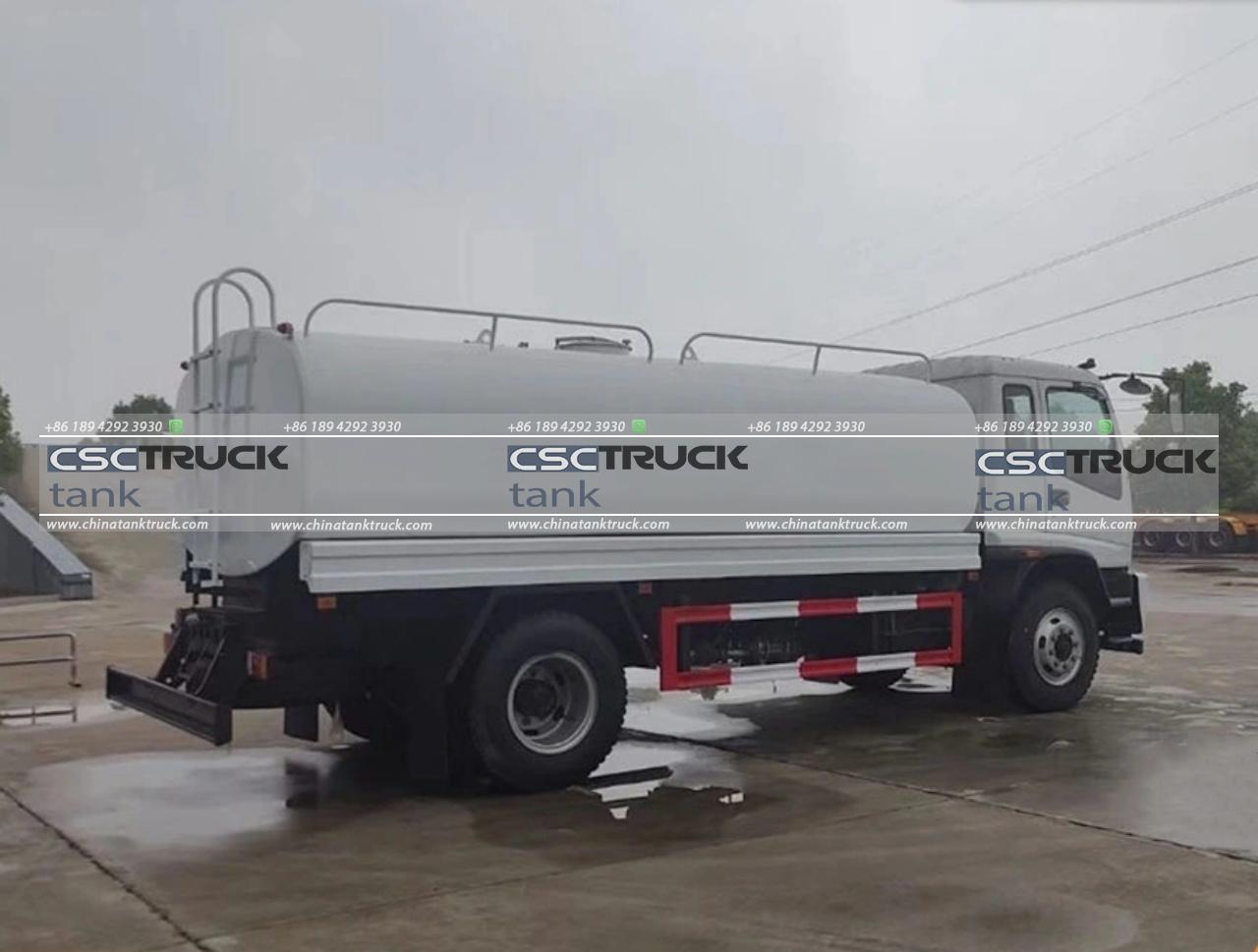
6. Innovations in Milk Tank Truck Design: Reducing Environmental Impact
As sustainability becomes more of a focus across industries, milk tank trucks are being designed to minimize their environmental impact. Here are some ways manufacturers are making these trucks more eco-friendly:
A. Lightweight Materials
Reducing the weight of a milk tank truck can significantly lower fuel consumption. Engineers are increasingly exploring lightweight but durable materials that don’t compromise on strength or insulation. Advanced alloys and composites are being incorporated to reduce overall weight while maintaining high standards of insulation.
B. Electric and Hybrid Milk Trucks
Electric and hybrid milk trucks are being developed to cut down on emissions. These vehicles are particularly beneficial for routes with frequent stops or areas with stringent emissions regulations. Additionally, since electric engines operate quietly, they’re ideal for early morning or late-night milk collection without disturbing communities.
7. Future of Milk Tank Trucks: Automation and Smart Tech
The future of milk tank trucks is heading toward automation and smart technology. Autonomous milk trucks are currently being tested in some regions, especially for repetitive routes between farms and dairies. These trucks use advanced GPS and sensor technology to navigate without a driver, cutting labor costs and improving efficiency.
AI-powered systems are also being developed to optimize routes based on traffic and temperature data. These systems can predict the best times to collect and deliver milk, ensuring freshness while minimizing energy consumption. Smart tech also assists in predictive maintenance, detecting when parts need repair, thus reducing downtime and increasing reliability.
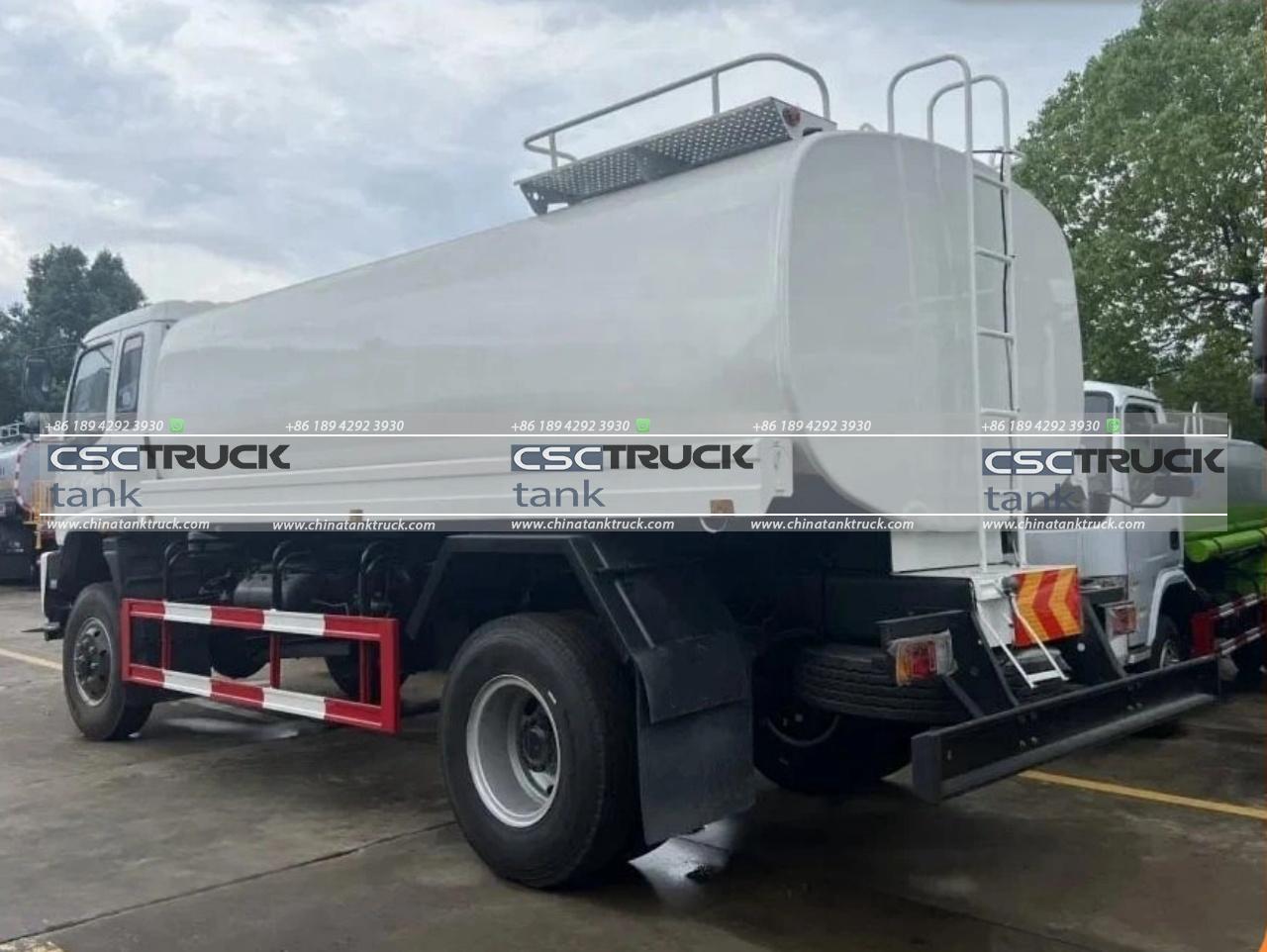
Conclusion
Milk tank trucks play a critical role in the dairy supply chain, ensuring the hygienic and insulated transport of milk from farms to dairies. Their design, built around high-quality stainless steel tanks, advanced insulation, and stringent hygiene protocols, safeguards milk quality and prevents spoilage. Innovations in insulation, temperature monitoring, and environmental technologies are pushing these trucks toward greater efficiency and sustainability, benefiting both dairy suppliers and consumers. As technology continues to advance, milk tank trucks will likely become even more specialized, embracing automation and eco-friendly materials to support a rapidly modernizing dairy industry.