How Does a Milk Tanker Work?
Milk tankers play an essential role in the dairy industry, transporting large quantities of fresh milk from farms to processing facilities safely and efficiently. Unlike general-purpose trucks, milk tankers are designed with specialized features to handle delicate and perishable products like milk. Let’s delve into how milk tankers work, from the design of the tanker itself to the process of milk collection, transportation, and delivery.
1. Design of the Milk Tanker
Milk tankers are designed with features that help maintain milk’s freshness and quality throughout the journey. Some critical design aspects include:
– Stainless Steel Construction: Most milk tankers are made from food-grade stainless steel, which is corrosion-resistant and easy to clean. Stainless steel prevents the milk from coming into contact with materials that could affect its flavor or safety, making it the ideal material for transporting perishable dairy products.
– Insulation: Milk tankers are typically insulated to keep the milk cool throughout transport. Insulated tankers are not refrigerated like traditional refrigerated trucks but rely on maintaining the temperature of the milk as it was at the time of loading. High-quality insulation keeps milk close to its original temperature (usually between 34°F to 39°F) for up to 24 hours, which is crucial for preventing bacterial growth and spoilage.
– Compartmentalized Tanks: Many milk tankers are divided into compartments, allowing them to carry milk from multiple farms or sources. This design allows each farm’s milk to be kept separate for quality control, sampling, and testing purposes. Compartmentalization also helps reduce sloshing during transit, making the tanker more stable and reducing the risk of spills.
– Rounded Shape: Milk tankers have a rounded cylindrical shape, which helps with weight distribution and minimizes the risk of structural stress. The rounded shape also prevents milk from accumulating in corners and reduces sloshing while the tanker is in motion.
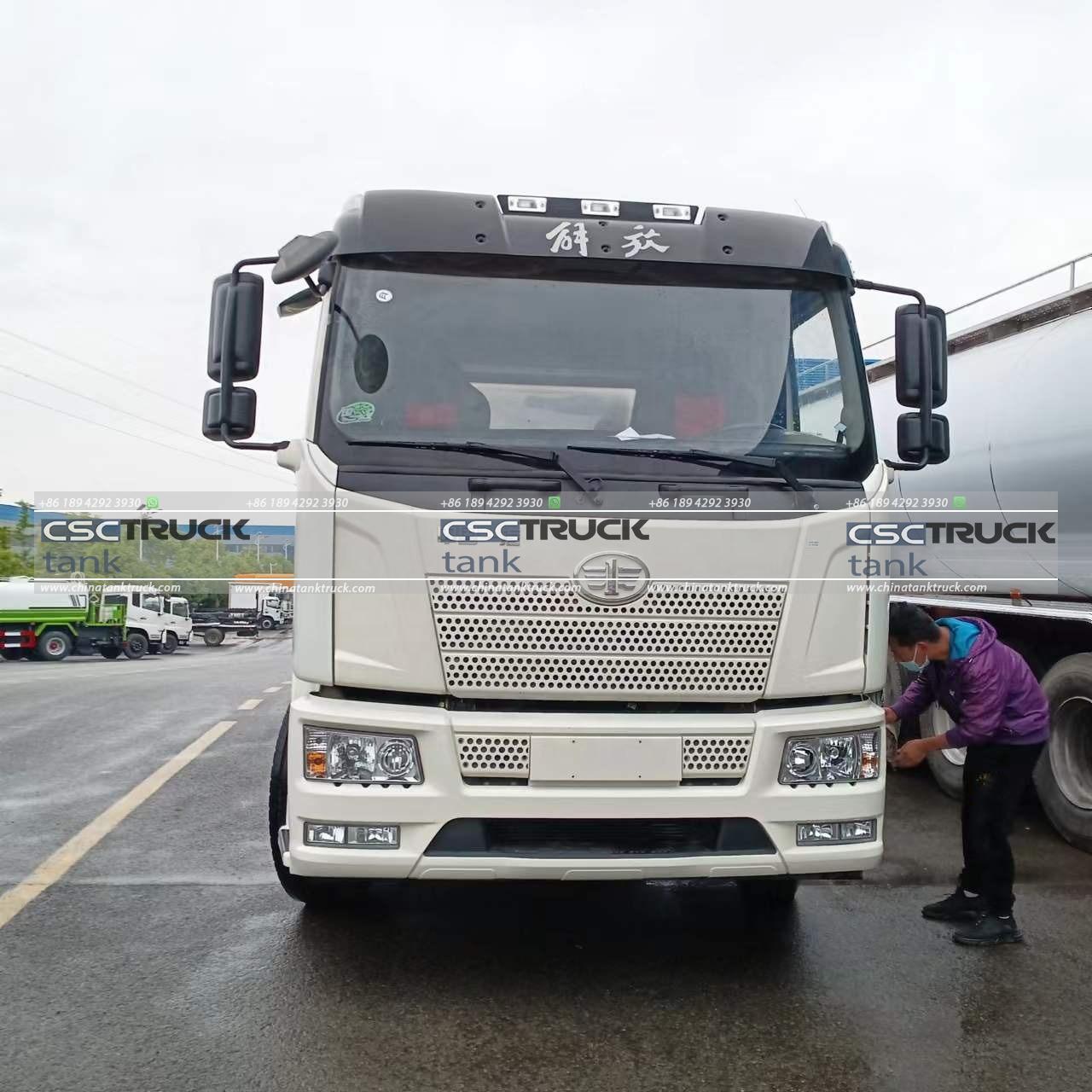
2. Loading the Milk
The process of loading milk into a tanker requires careful handling to maintain quality and comply with safety regulations.
– Milk Collection at the Farm: Milk tankers travel directly to dairy farms where the milk is collected. Farms typically store their milk in refrigerated bulk tanks to keep it at the right temperature before collection. Once the milk tanker arrives, a trained operator connects a hose from the farm’s storage tank to the tanker’s inlet valve.
– Sampling and Testing: Before loading the milk, the operator collects a sample for quality testing. These tests are essential for verifying that the milk meets safety and quality standards and checking for bacterial contamination, antibiotic residues, and temperature compliance.
– Gravity and Pumping: Milk is typically loaded into the tanker using a combination of gravity and pump mechanisms. Once the inlet hose is connected, a pump may be used to move the milk into the tanker, or gravity may assist in allowing the milk to flow from the storage tank to the lower part of the tanker. This process helps maintain milk quality by avoiding excessive agitation, which can lead to unwanted foaming.
3. Maintaining Milk Quality During Transportation
Milk’s delicate nature makes quality control during transit essential. Here are some key methods employed to keep the milk in good condition.
– Temperature Control: Since milk tankers are insulated but not refrigerated, maintaining the temperature is crucial. After loading, the tank’s insulation maintains the milk’s temperature to prevent spoilage. Some modern tankers use advanced insulation techniques to reduce temperature fluctuations, ensuring that milk arrives at the processing plant as fresh as it was at the farm.
– Sanitization Protocols: To prevent contamination, milk tankers must adhere to strict sanitization protocols. Tankers are thoroughly cleaned and sanitized after each delivery to avoid bacterial buildup. This includes cleaning the tank, hoses, and any other equipment that comes into contact with the milk. Cleaning and sanitizing are done using specialized equipment and chemical agents that remove bacteria and residues without leaving harmful traces.
– Minimizing Agitation and Sloshing: Agitation can damage milk’s structure and cause unwanted foaming, which can affect quality. The design of milk tankers minimizes sloshing by employing internal baffles in the compartments. These baffles slow down the movement of the milk when the tanker stops or makes turns, ensuring that the milk stays as still as possible and reducing the risk of spoilage.
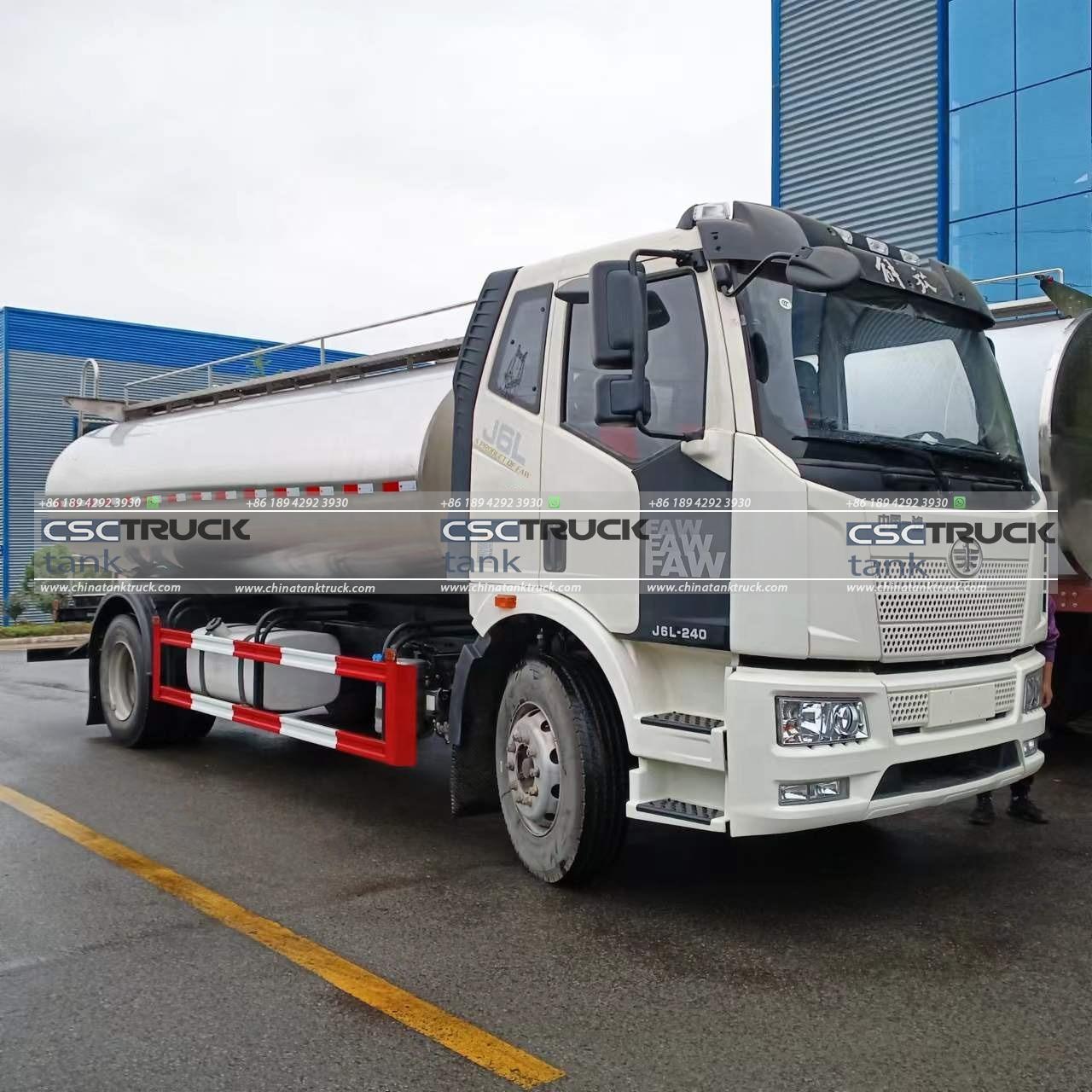
4. Unloading the Milk at the Processing Facility
Once the milk arrives at the processing facility, it is ready to be unloaded. This process is carefully monitored to maintain milk quality and ensure that each batch remains traceable to its source.
– Connecting to the Facility’s Storage Tanks: Upon arrival, a milk sample is taken again for final testing, verifying that the milk remained at a safe temperature and was not contaminated during transport. After testing, the operator connects the tanker’s hose to the facility’s storage tanks for unloading.
– Pump-Assisted Unloading: Unloading usually requires pumping since the milk needs to be moved up into the storage tanks of the processing facility. High-quality, food-grade pumps are used to avoid contamination and maintain the milk’s structural integrity.
– Cleaning and Preparation for the Next Load: After unloading, the tanker undergoes a rigorous cleaning process. This includes washing the interior, hoses, and pumps to remove any milk residues and prevent bacterial contamination. The tanker is then prepared for its next load, ensuring it is sterile and ready to transport fresh milk from another farm.
5. Advanced Features in Modern Milk Tankers
With advancements in technology, modern milk tankers come with additional features that help streamline transportation and improve quality control.
– Data Logging Systems: Many modern milk tankers are equipped with data logging systems that monitor temperature and other conditions in real-time. These systems provide live data on the milk’s temperature and other conditions during transit, alerting operators to any changes that could affect quality. This information can also be shared with the processing facility and dairy farms, adding another layer of traceability.
– GPS Tracking and Routing: GPS tracking allows milk tanker operators to optimize routes, reducing transport times and fuel costs. This helps ensure that milk reaches the processing plant as quickly as possible, which is critical for a perishable product. Real-time tracking also enables dispatchers to monitor tanker locations and make adjustments if there are unexpected delays or detours.
– Automated Sampling Systems: Some tankers now come with automated sampling systems that take and store samples of milk from each compartment. These samples can be analyzed to track quality issues back to individual farms, improving traceability and quality control.
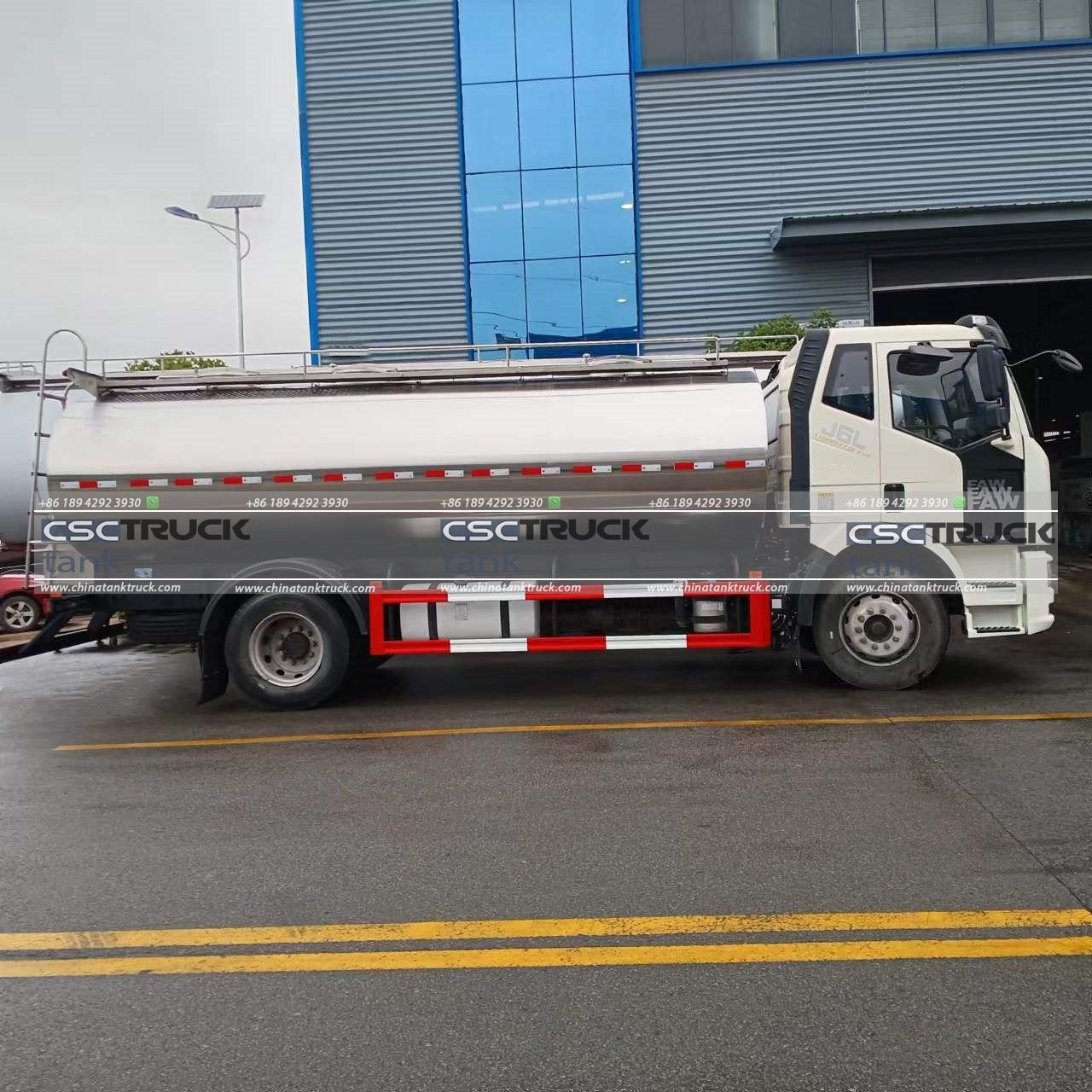
6. Environmental Considerations in Milk Tanker Operations
Milk tankers must also account for environmental concerns, given their significant fuel use and the demand for sustainability in logistics.
– Fuel Efficiency: Tankers are often designed with fuel efficiency in mind. Lightweight construction materials, aerodynamic designs, and efficient routing all help reduce fuel consumption. Some dairy transport companies are beginning to explore the use of electric or hybrid milk tankers to minimize their environmental footprint further.
– Eco-Friendly Cleaning Protocols: Given the water and chemicals involved in sanitizing tankers, eco-friendly cleaning solutions are increasingly popular. Some facilities are adopting closed-loop cleaning systems that reuse water, and biodegradable cleaning agents to reduce the environmental impact of regular sanitization.
Conclusion
Milk tankers play a vital role in ensuring that fresh, high-quality milk reaches consumers safely and efficiently. From their specialized design to maintain temperature and prevent contamination to advanced data logging and environmental considerations, milk tankers are built with a focus on preserving the quality of a highly perishable product. Through innovation in design and technology, milk tankers continue to evolve, making the journey from farm to table smoother, safer, and more efficient than ever.
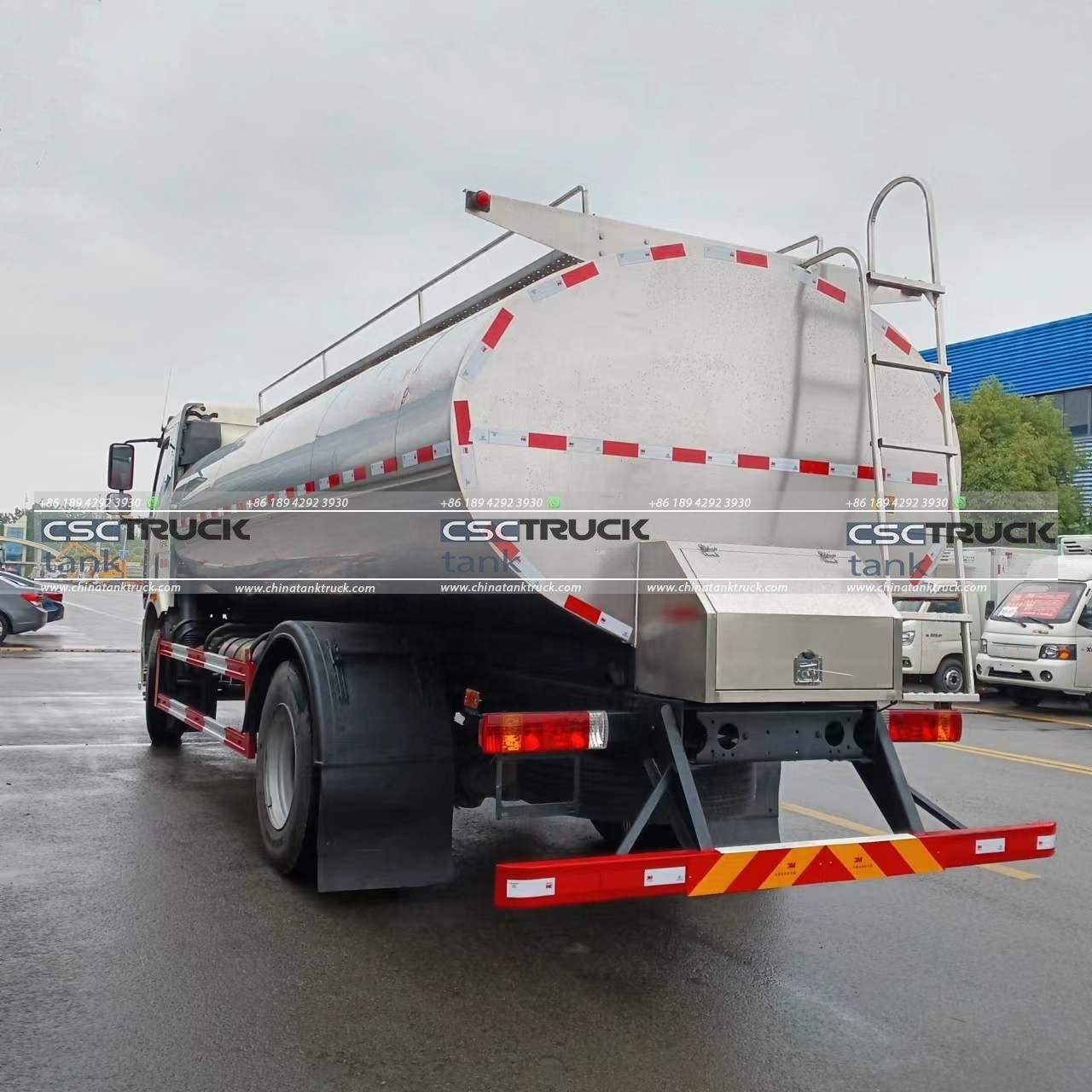