How Do You Fill an ISO Tank?
ISO tanks are an integral part of the global logistics and transportation network, used for shipping various liquids including chemicals, food products, and fuels. Filling these tanks requires a precise process to ensure safety, efficiency, and compliance with international standards. This article provides a comprehensive guide on how to fill an ISO tank, highlighting essential procedures, safety considerations, and best practices.
Understanding ISO Tanks
ISO tanks are standardized containers designed for the transportation of liquid cargo. They are built to ISO (International Organization for Standardization) specifications, ensuring uniformity and compatibility across different modes of transport, such as ships, trains, and trucks. These tanks are typically made of stainless steel and are equipped with insulation and heating elements if required.
Components of an ISO Tank:
– Tank Body: The main compartment where the liquid is stored.
– Valves: Control the flow of liquid into and out of the tank.
– Pipes and Hoses: Used for transferring liquid.
– Pressure Relief Valves: To prevent overpressure situations.
– Temperature and Pressure Gauges: To monitor the conditions inside the tank.
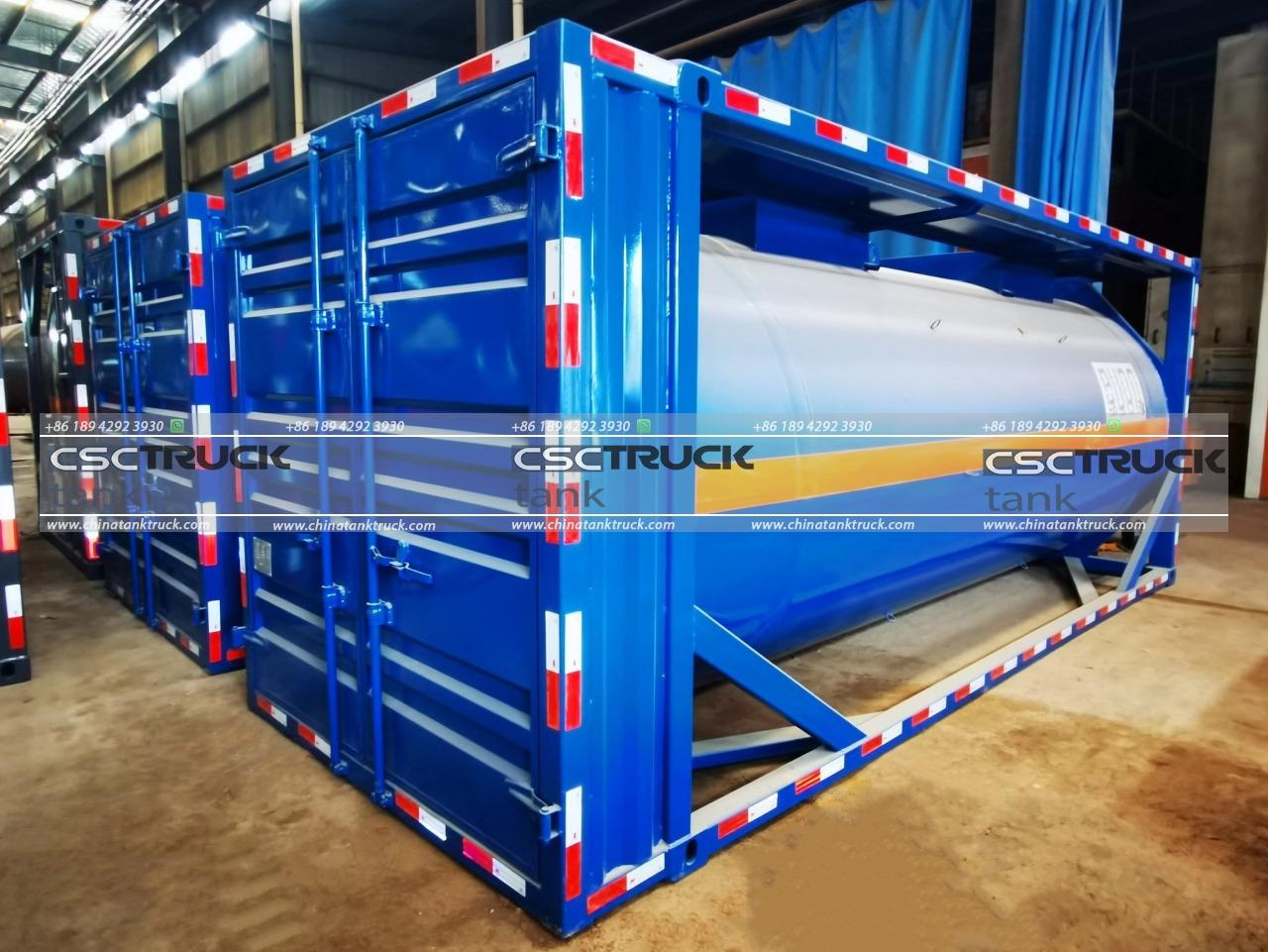
Preparation Before Filling
1. Inspect the Tank:
  Before filling an ISO tank, it’s crucial to perform a thorough inspection. Check for any signs of damage or wear and ensure that all valves and seals are functioning correctly. Verify that the tank is clean and free from any residues from previous loads.
2. Verify Compatibility:
  Ensure that the liquid to be filled is compatible with the tank’s material and the previous contents. For example, a tank previously used for chemicals should be properly cleaned and verified before being filled with food-grade liquids.
3. Review Documentation:
  Ensure all required documentation, including safety data sheets (SDS) for the liquid being transported and certificates of cleanliness or inspection, is in order. This documentation helps ensure compliance with regulations and safety standards.
4. Check Equipment:
  Inspect all equipment used for filling the tank, including hoses, pumps, and connections. Make sure they are clean, properly maintained, and suitable for the liquid being transferred.
The Filling Process
1. Prepare the Filling Station:
  Set up the filling station by connecting the hoses and ensuring all connections are secure. The filling station should be equipped with necessary safety features like spill containment and emergency shut-off systems.
2. Connect to the Tank:
  Attach the filling hose to the ISO tank’s inlet valve. Ensure a tight seal to prevent leaks. It is common to use camlock or flange connections, which are designed for quick and secure attachment.
3. Start the Transfer:
  Begin the transfer process by opening the inlet valve and activating the pump. Monitor the flow rate and ensure it is within safe limits for the liquid being filled. Overfilling or high flow rates can cause spills or damage to the tank.
4. Monitor the Process:
  Continuously monitor the tank’s pressure and temperature using the installed gauges. Maintain regular communication with the filling operator to address any issues promptly. If the liquid being filled is sensitive to temperature, ensure that it is kept within the specified range.
5. Check Levels:
  As the tank nears full capacity, closely monitor the liquid levels. Most ISO tanks have a level gauge or sight glass that provides a visual indication of the liquid level. Do not exceed the maximum fill level indicated for the tank.
6. Finalizing the Fill:
  Once the tank reaches the desired level, close the inlet valve and stop the pump. Disconnect the filling hose and ensure the valve is securely closed to prevent leakage. Conduct a final inspection to ensure no spills or leaks occur during the filling process.
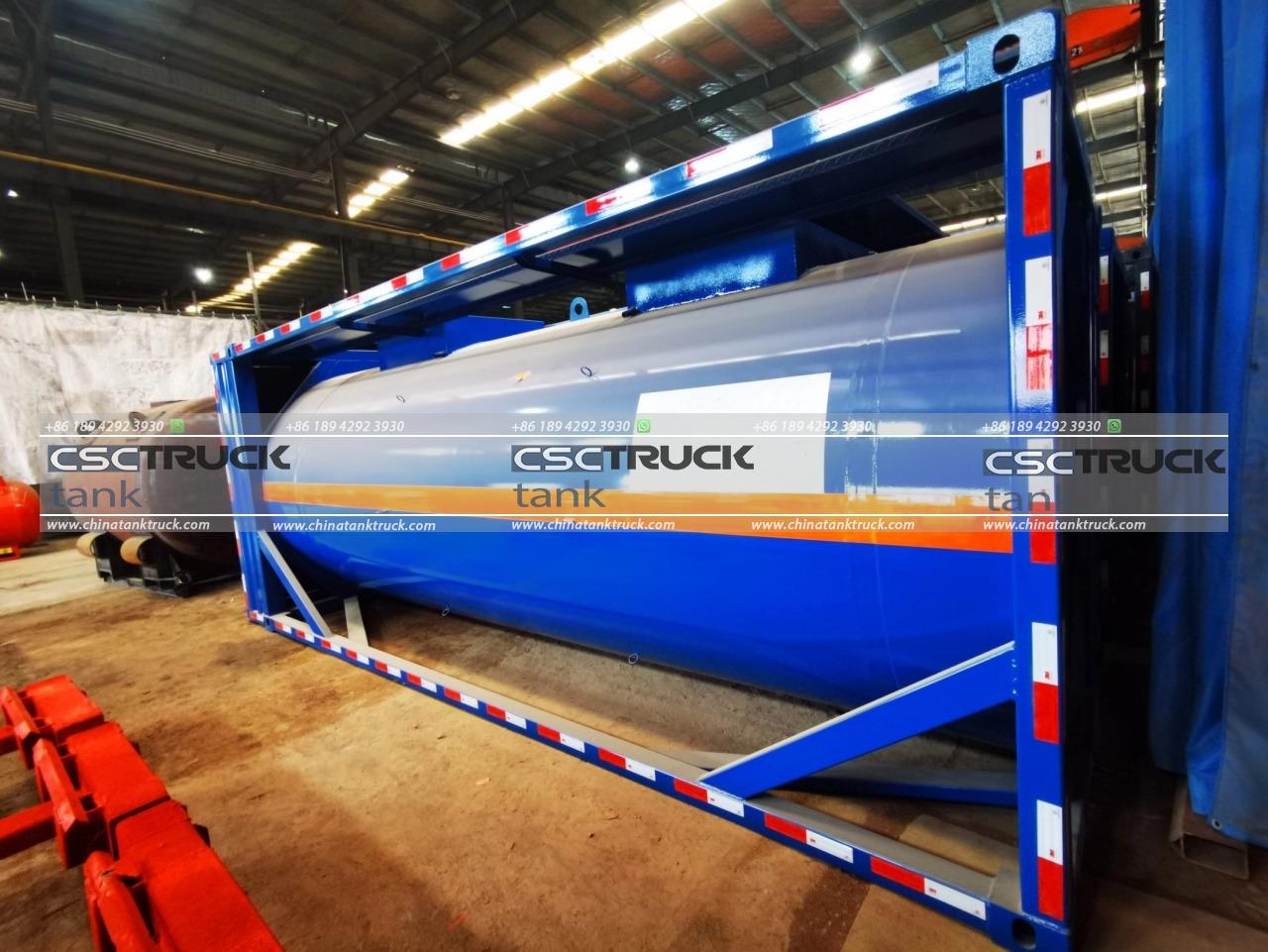
Post-Filling Procedures
1. Clean Up:
  Clean the filling area and equipment to remove any residual liquid or potential contaminants. Properly dispose of any waste or cleaning materials by environmental regulations.
2. Document the Fill:
  Complete all necessary documentation, including filling reports and inspection logs. Record details such as the type and quantity of liquid filled, the date and time, and the name of the operator.
3. Inspect for Leaks:
  Conduct a post-filling inspection of the ISO tank to ensure there are no leaks or other issues. Perform a pressure test if required to confirm the integrity of the tank.
4. Prepare for Transport:
  Ensure that the tank is properly sealed and prepared for transportation. Check that all required labels and documentation are in place. Verify that the tank is secured and ready for its journey to its destination.
Safety Considerations
1. Personal Protective Equipment (PPE):
  Operators should wear appropriate PPE, including gloves, goggles, and protective clothing, to minimize the risk of exposure to hazardous materials.
2. Emergency Procedures:
  Be familiar with emergency procedures for spills, leaks, or accidents. Ensure that emergency response equipment, such as spill kits and fire extinguishers, is readily available and in good condition.
3. Training:
  Ensure that all personnel involved in the filling process are properly trained and familiar with the procedures, safety protocols, and the characteristics of the liquid being handled.
4. Compliance:
  Adhere to all relevant regulations and standards, including those set by organizations like the International Maritime Organization (IMO) and the Department of Transportation (DOT). Compliance helps ensure safety and avoids legal issues.
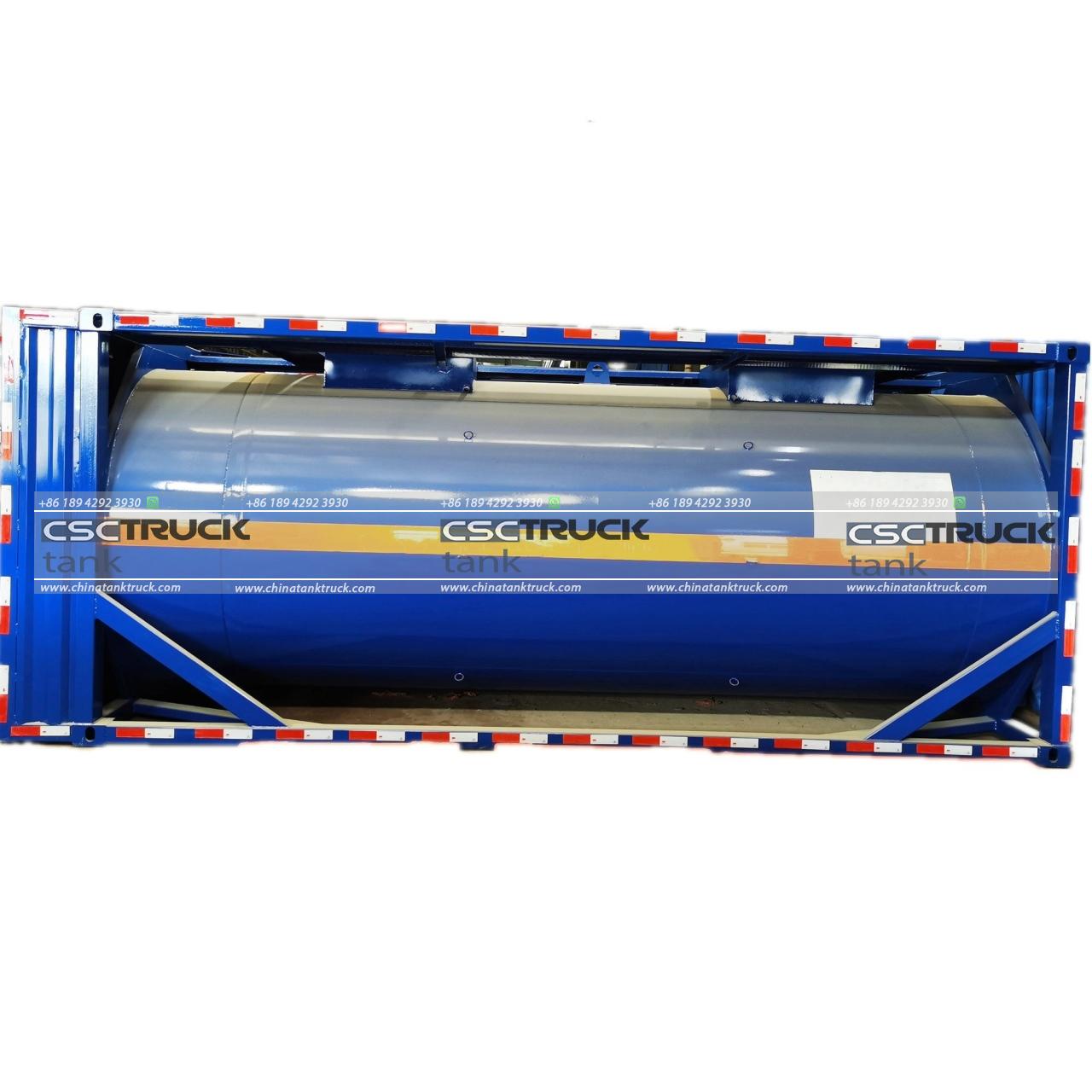
Conclusion
Filling an ISO tank is a complex process that requires careful preparation, precise execution, and rigorous adherence to safety standards. By following the outlined procedures and best practices, operators can ensure efficient and safe filling operations, minimizing risks and ensuring compliance with industry regulations. As global trade continues to expand, understanding and mastering the intricacies of ISO tank filling will remain a crucial skill for professionals in the logistics and transportation sectors.