How Do Pneumatic Air Cylinders Work?
Pneumatic air cylinders, often referred to as air cylinders or pneumatic actuators, are mechanical devices that use the power of compressed air to produce a force in a reciprocating linear motion. These devices are commonly used in industrial machinery, automation systems, and various other applications that require controlled and precise movement. In this article, we will explore the working principles of pneumatic air cylinders, their types, components, and common applications.
Basic Working Principle of Pneumatic Air Cylinders
At the heart of a pneumatic air cylinder is the principle of converting air pressure into mechanical energy. Compressed air, which is air at a higher pressure than the atmosphere, is used to move a piston inside a cylinder. The movement of the piston can be harnessed to produce linear motion, which can be used to push, pull, or lift objects.
Here is a step-by-step explanation of how pneumatic air cylinders work:
1. Compressed Air Supply: A pneumatic system is powered by an external air compressor that supplies compressed air. This air is directed into the pneumatic cylinder through valves and tubing. The pressure of the compressed air is the driving force behind the cylinder’s operation.
2. Air Enters the Cylinder: When compressed air is directed into one end of the cylinder (the chamber on one side of the piston), it pushes against the piston, causing it to move. The movement of the piston generates a linear motion, which can be used to perform work, such as moving a load or opening a valve.
3. Piston Movement: The piston inside the cylinder moves linearly in response to the pressure difference between the 2 sides of the cylinder. In a single-acting cylinder, compressed air is only supplied to one side of the piston, and a spring is used to return the piston to its original position once the air is released. In contrast, a double-acting cylinder uses compressed air on both sides of the piston to control movement in both directions.
4. Exhaust of Air: After the piston has completed its stroke, the compressed air needs to be exhausted from the cylinder. In single-acting cylinders, the air is vented from the side of the cylinder that is not pressurized. In double-acting cylinders, air is exhausted alternately from both sides of the piston as it moves back and forth.
5. Controlling the Motion: The speed, force, and position of the piston can be controlled by regulating the amount of compressed air, the size of the cylinder, and the pressure inside the cylinder. This is often achieved using control valves, pressure regulators, and flow control devices.
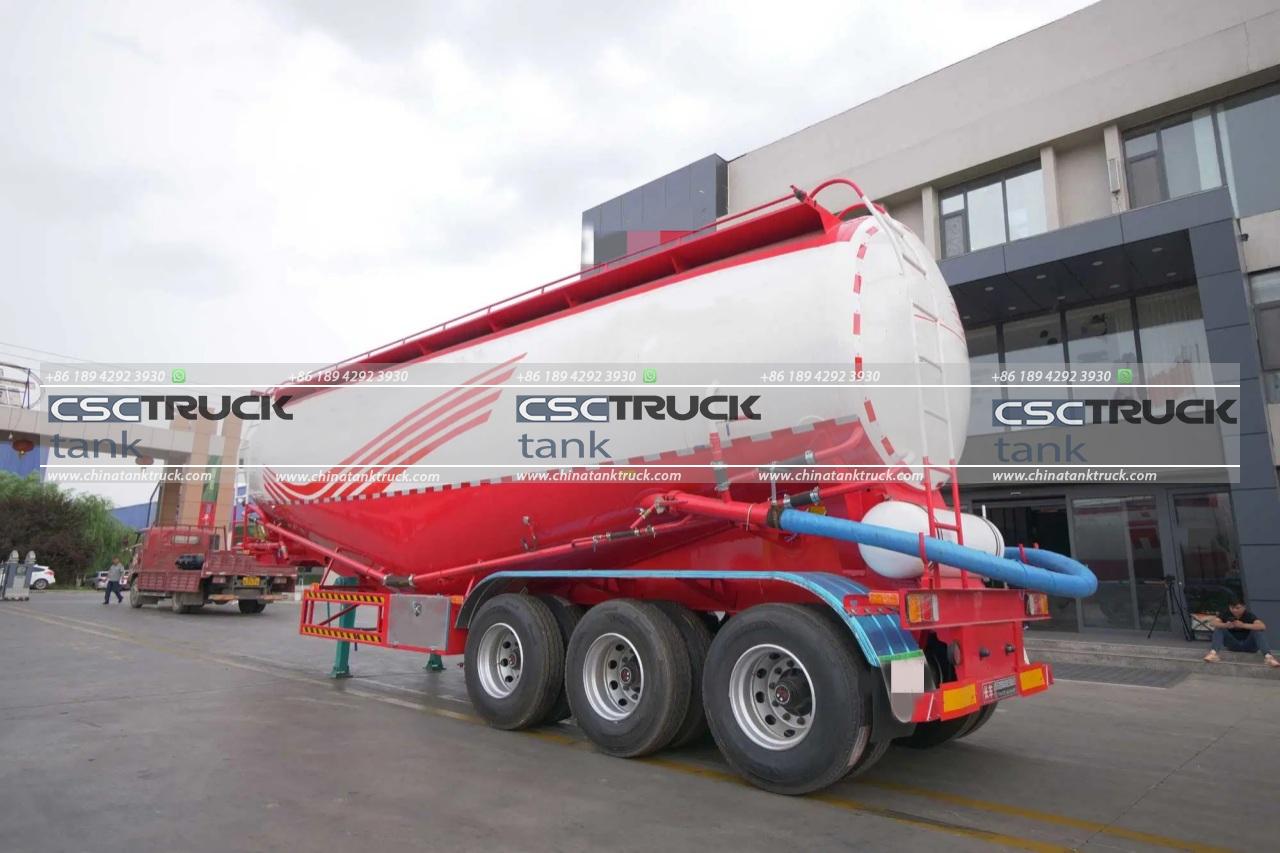
Types of Pneumatic Air Cylinders
There are several types of pneumatic air cylinders, each designed for different applications and working conditions. The most common types include:
1. Single-Acting Cylinders (SAC)
In a single-acting cylinder, compressed air is applied to one side of the piston to move in one direction. The return stroke is typically powered by a spring or external force. These cylinders are simple in design and are used in applications where the force is only needed in one direction, such as lifting or clamping.
– Advantages: Low cost, simple design, reduced air consumption.
– Disadvantages: Limited stroke length, lower efficiency compared to double-acting cylinders.
2. Double-Acting Cylinders (DAC)
Double-acting cylinders have airports at both ends, allowing compressed air to be supplied to either side of the piston. This setup enables the piston to move in both directions with controlled force and speed. Double-acting cylinders are more versatile and are commonly used in industrial automation for pushing and pulling tasks.
– Advantages: Precise control of movement in both directions, higher efficiency.
– Disadvantages: Higher air consumption, more complex design.
3. Telescoping Cylinders
Telescoping cylinders consist of multiple stages or sections that extend from within one another, much like the segments of a telescope. This design allows for a longer stroke than would be possible with a single, fixed-length cylinder. Telescoping cylinders are often used in applications that require long extension capabilities, such as hydraulic lifts or aerial platforms.
– Advantages: Long stroke with compact retracted length.
– Disadvantages: More complex design, potential for more wear and tear.
4. Rodless Cylinders
In a rodless cylinder, the piston is connected to a carrier on the outside of the cylinder, allowing the piston to move without an external rod. This type of cylinder is used in situations where space constraints or the need for an uninterrupted surface make traditional rod-type cylinders unsuitable.
– Advantages: Compact design, suitable for applications with space limitations.
– Disadvantages: More expensive and complex.
5. Rotary Pneumatic Cylinders
While most pneumatic cylinders produce linear motion, rotary pneumatic cylinders produce rotational movement. These cylinders use the same principle of air pressure but convert the linear motion of a piston into a rotary motion using gears or other mechanical linkages. They are commonly used in applications requiring rotational motion, such as turning valves or operating rotary tools.
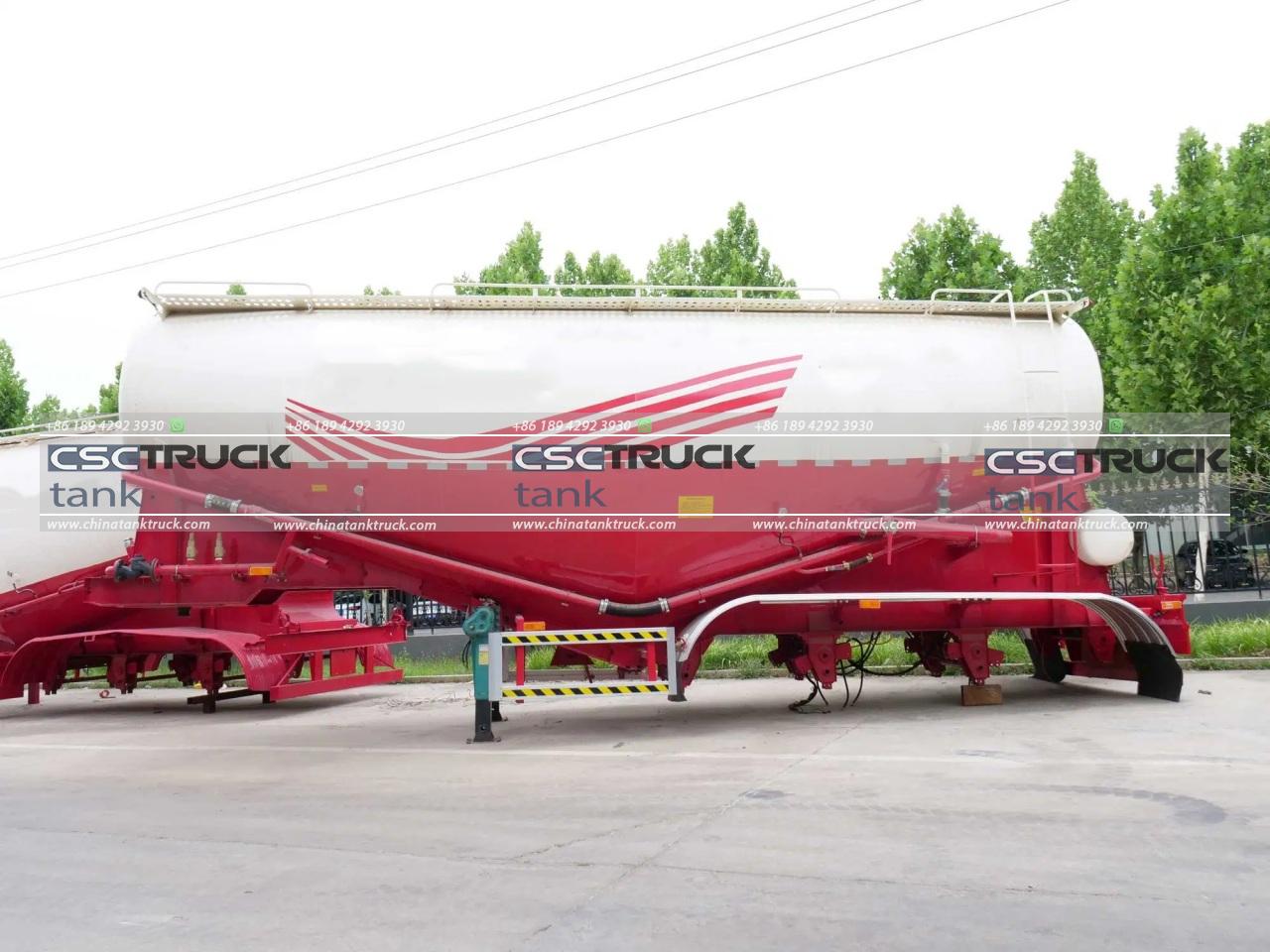
Key Components of a Pneumatic Air Cylinder
Pneumatic cylinders consist of several critical components that work together to generate controlled linear or rotary motion. The key components include:
1. Cylinder Body:Â
The cylinder body is a hollow tube that contains the piston and allows it to move back and forth. It is usually made of materials like aluminum, steel, or stainless steel to withstand high pressure and resist wear.
2. Piston:Â
The piston is the moving component inside the cylinder that divides the internal volume into 2 chambers. The piston moves in response to the force of compressed air and transmits that force to the load. Pistons are usually fitted with seals to prevent air leakage between the chambers.
3. Piston Rod:Â
The piston rod is a solid bar that extends from the piston to the outside of the cylinder, transmitting the force generated by the piston to the load or external mechanism. In double-acting cylinders, the piston rod may extend from both ends of the cylinder.
4. End Caps:Â
End caps are located at both ends of the cylinder and contain airports through which compressed air is supplied and exhausted. The end caps also support the piston rod and provide structural integrity to the cylinder.
5. Seals:Â
Seals are critical components that prevent air leakage within the cylinder and ensure efficient operation. They are typically made of rubber or other flexible materials and are located around the piston, piston rod, and end caps.
6. Air Ports:Â
Air ports are the openings in the cylinder that allow compressed air to enter and exit. Control valves are connected to these ports to regulate the flow of air and control the motion of the piston.
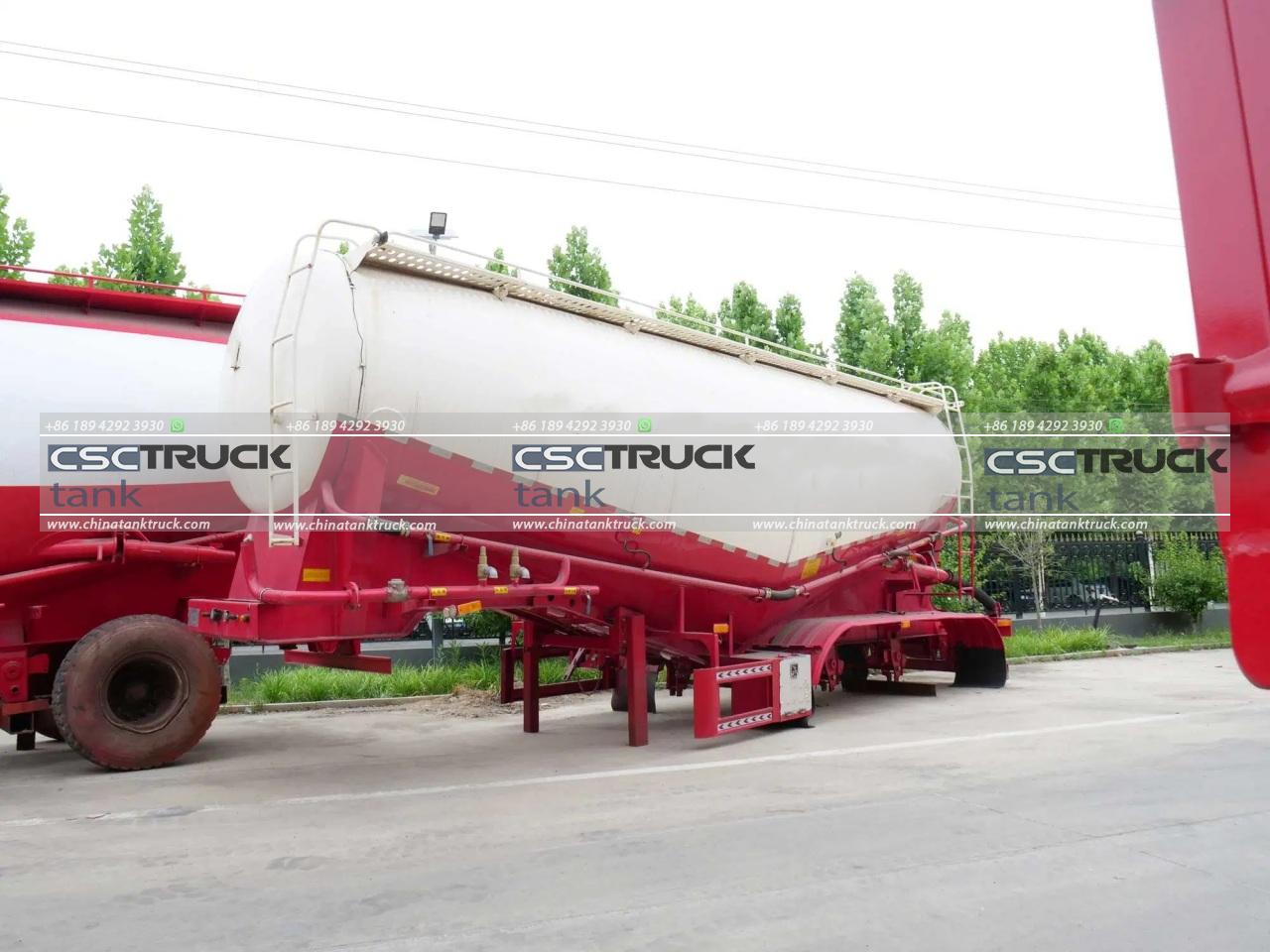
Applications of Pneumatic Air Cylinders
Pneumatic air cylinders are used in a wide range of applications across industries, including:
– Manufacturing and Automation: Pneumatic cylinders are used in assembly lines, packaging machines, and robotic systems to perform tasks such as lifting, pushing, and gripping.
– Automotive Industry: They are used in car manufacturing plants to operate robotic arms, presses, and other machinery.
– Medical Devices: Pneumatic actuators are used in medical devices, such as ventilators, to control airflow and assist breathing.
– Agriculture: Pneumatic cylinders are used in farm equipment for tasks like seed planting and crop harvesting.
– Aerospace: In aircraft systems, pneumatic cylinders are used to control flaps, doors, and landing gear.
Conclusion
Pneumatic air cylinders are vital components in industrial automation and other systems that require precise and controlled motion. Their ability to convert compressed air into linear or rotary movement makes them versatile and widely used across different industries. Understanding how they work and their various types can help in selecting the right cylinder for a specific application, ensuring efficiency and reliability in the system.
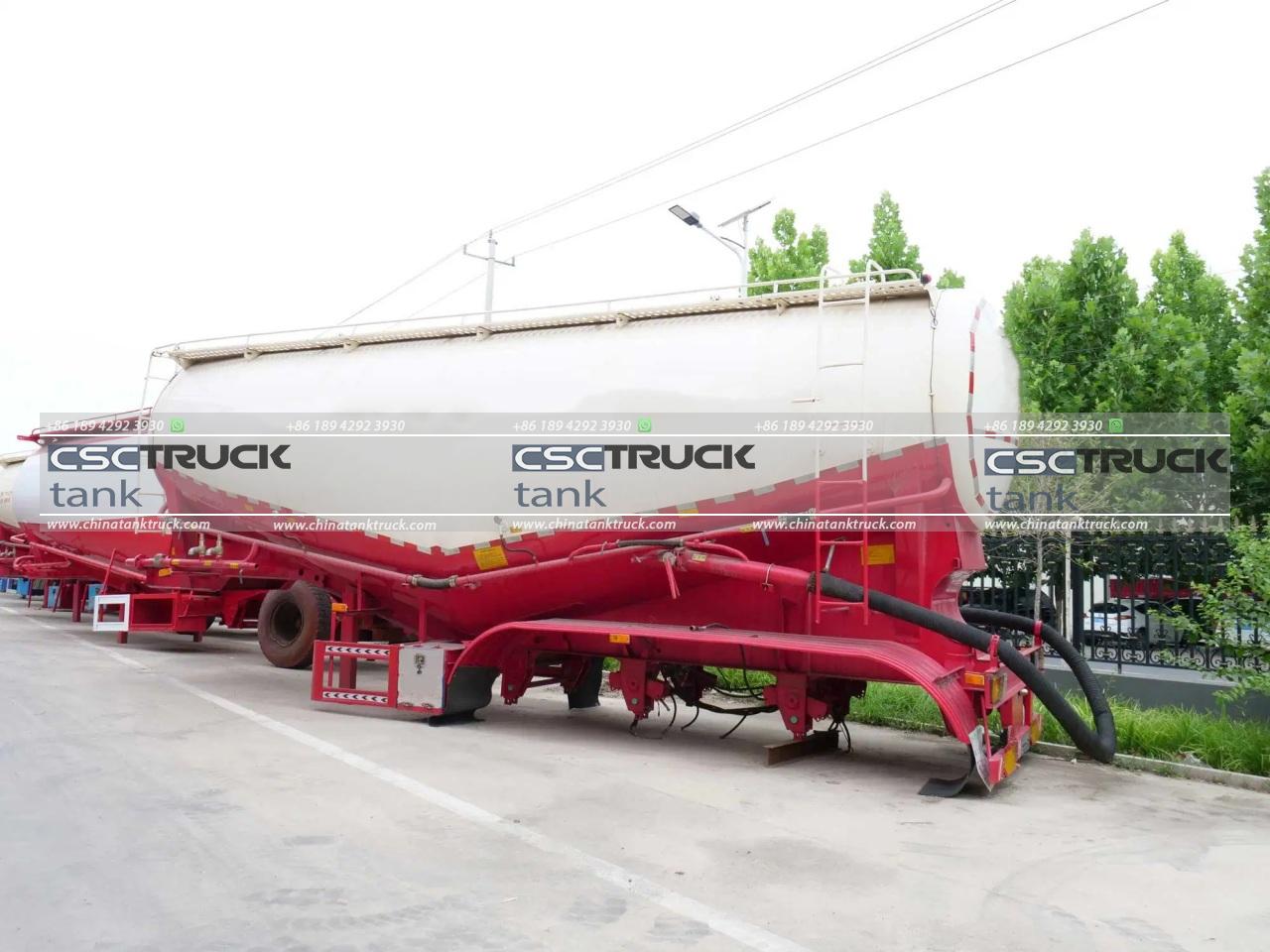