How Do Milk Tankers Stay Cold?
Milk is a highly perishable product, requiring stringent measures to ensure it remains fresh from the moment it leaves the farm until it reaches the consumer. One of the critical stages in the milk supply chain is transportation, where milk is moved from dairy farms to processing plants, often over long distances. This is where milk tankers come into play. These large vehicles are specially designed to keep milk cold, preserving its quality and safety. But how exactly do milk tankers stay cold? Let’s explore the intricate process that ensures your glass of milk remains fresh.
1. The Importance of Temperature Control
Milk needs to be kept at a consistent temperature of about 3-4°C (37-39°F) to prevent bacterial growth and spoilage. The moment milk is harvested from cows, it begins to degrade, and without proper refrigeration, it can quickly become unsafe to consume. The milk tanker’s primary function is to maintain this low temperature throughout the journey from farm to processing plant.
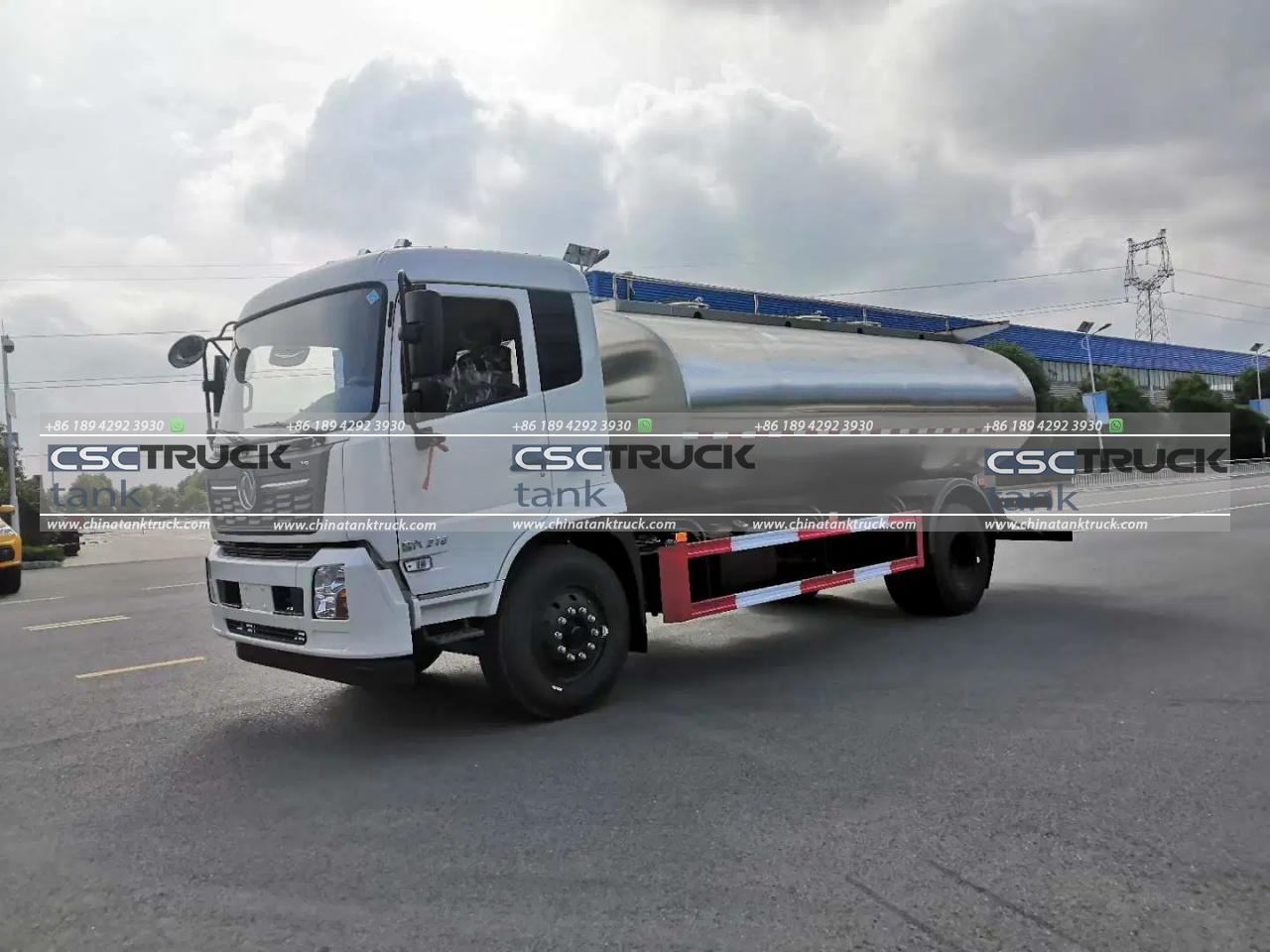
2. Insulation: The First Line of Defense
The most critical component in keeping milk cold is the insulation of the tanker. Milk tankers are built with layers of high-quality insulation materials, typically polyurethane foam or similar substances, sandwiched between layers of stainless steel. This insulation works similarly to a thermos flask, minimizing heat exchange between the milk inside and the external environment.
The thickness of the insulation varies depending on the design of the tanker, but it’s typically substantial enough to maintain the milk’s temperature for many hours. The outer layer of stainless steel also serves to reflect sunlight, reducing the amount of external heat absorbed by the tanker.
3. Pre-Cooling at the Farm
Before milk even enters the tanker, it undergoes a pre-cooling process at the farm. Once milk is collected, it is quickly cooled using plate coolers or bulk tanks that bring the temperature down to the desired level. This step is crucial because it means the milk enters the tanker already at the correct temperature, reducing the need for the tanker itself to cool the milk further. The pre-cooled milk is then pumped into the tanker, which is sealed to preserve the low temperature.
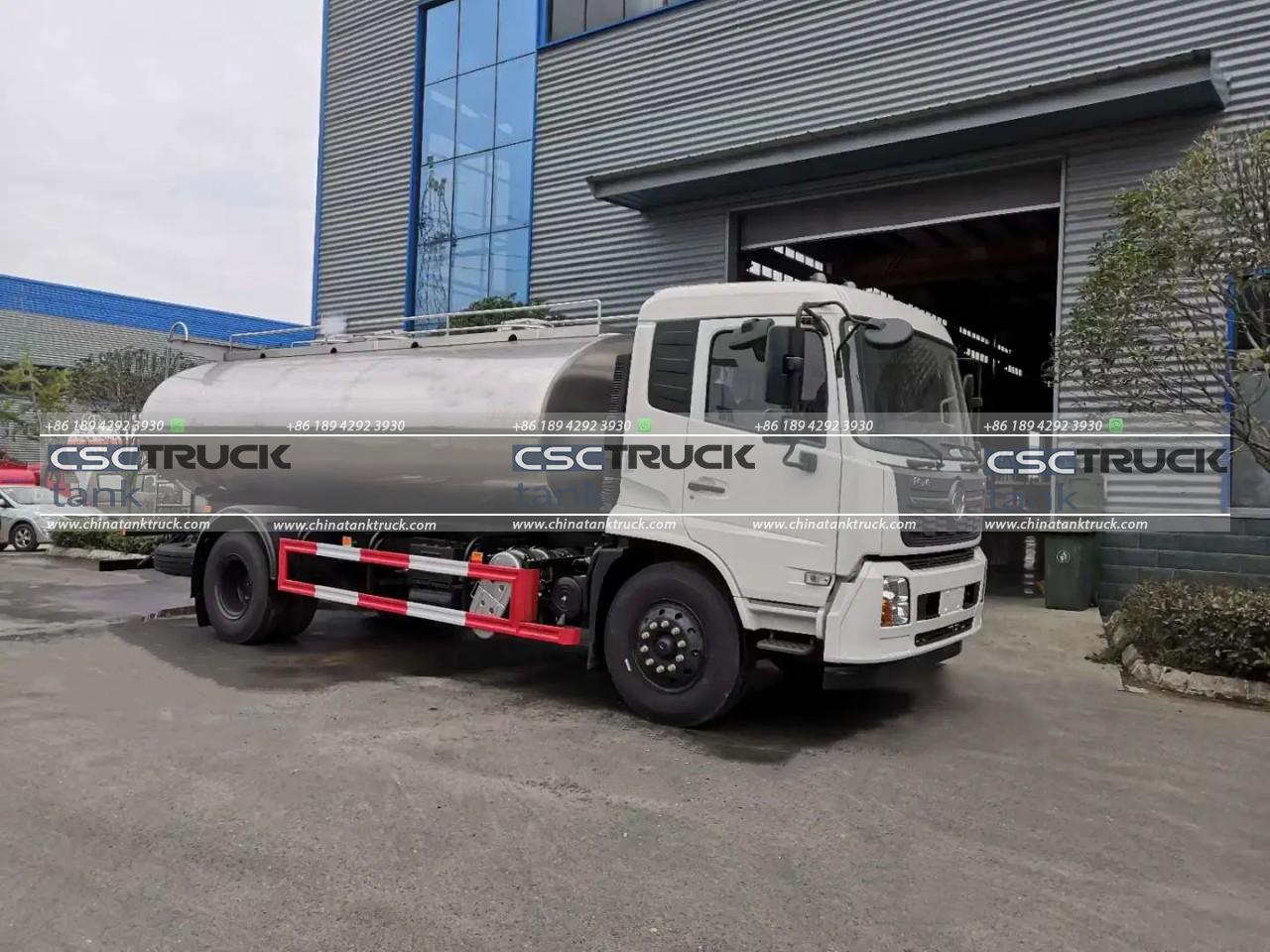
4. Refrigeration Units: The Power Behind the Cold
Some milk tankers are equipped with onboard refrigeration units, although this is less common. These units function similarly to refrigerators, using a compressor, evaporator, and refrigerant to remove heat from the milk and keep it cold.
The refrigeration system is typically powered by the truck’s engine or an auxiliary power unit. However, because these systems can be costly and require regular maintenance, they are often used as a backup rather than the primary method of cooling. The onboard refrigeration units are more common in tankers that need to transport milk over exceptionally long distances or in scorching climates where insulation alone may not suffice.
5. Circulation Systems: Even Temperature Distribution
To ensure that the milk remains at a consistent temperature throughout the journey, many milk tankers are equipped with circulation systems. These systems circulate the milk within the tanker, preventing temperature gradients from forming. Without circulation, milk at the edges of the tank might warm up faster than milk in the center, leading to uneven cooling and potential spoilage.
The circulation system works by gently stirring the milk, either through mechanical means or by using the movement of the vehicle to create natural circulation. This continuous mixing ensures that all the milk in the tanker remains at the same temperature.
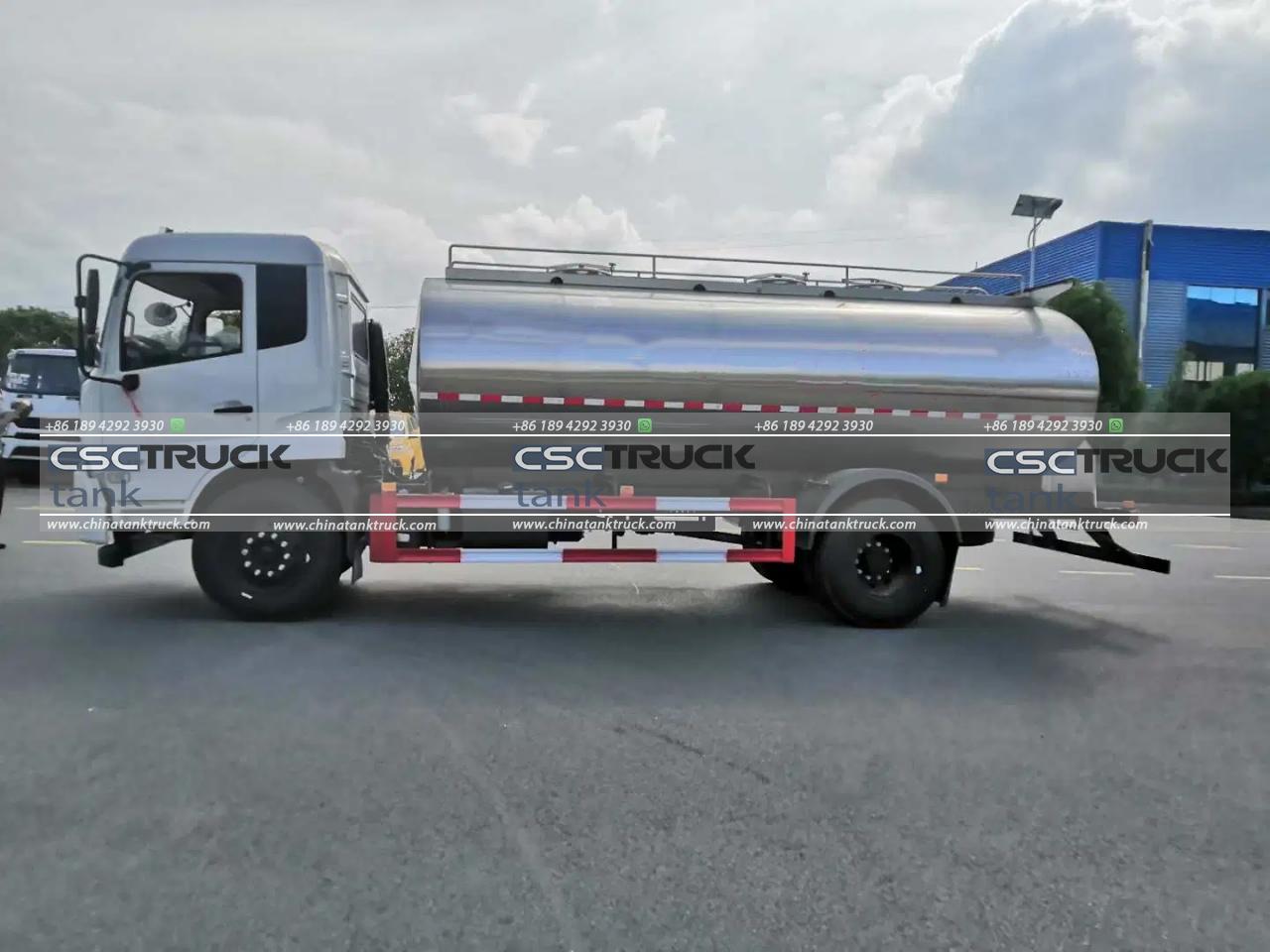
6. Monitoring and Control Systems: Keeping an Eye on Things
Modern milk tankers are equipped with sophisticated monitoring and control systems that track the temperature of the milk throughout the journey. Sensors placed at various points within the tank continuously measure the temperature, sending data to the driver and the processing plant in real-time.
Suppose the temperature begins to rise above the safe threshold. In that case, the system can alert the driver, who may be able to take corrective action, such as activating the refrigeration unit or adjusting the route to minimize exposure to heat. Some systems are also capable of automatically activating cooling mechanisms if they detect a temperature increase.
These monitoring systems are critical in ensuring that any issues are caught early, preventing a load of milk from spoiling before it reaches the processing plant.
7. Cleaning and Sanitation: Keeping It Clean
Keeping the milk cold is not just about maintaining temperature; it’s also about ensuring the tanker itself is clean and free from contaminants. After each delivery, milk tankers undergo a rigorous cleaning and sanitation process. This involves flushing the tank with hot water and cleaning agents, followed by sterilization with steam or chemical sanitizers.
A clean tanker is essential for preventing bacterial contamination, which could cause the milk to spoil even if it is kept at the correct temperature. The cleanliness of the tanker is regularly inspected, and failure to meet hygiene standards can result in fines or the rejection of the milk by the processing plant.
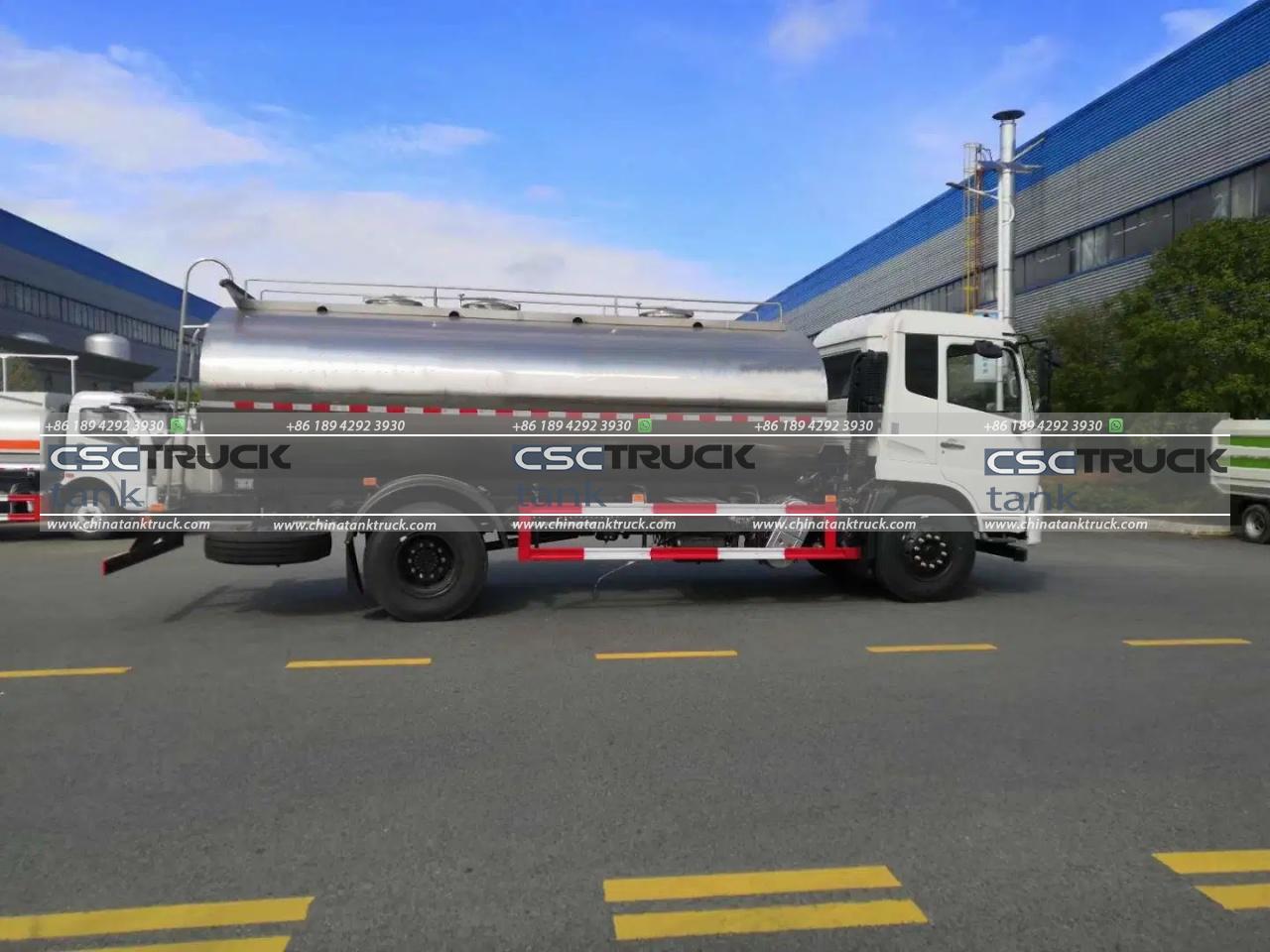
8. Environmental Considerations: Balancing Efficiency and Sustainability
Transporting milk while keeping it cold is an energy-intensive process, especially if refrigeration units are in use. The dairy industry is increasingly focused on finding ways to reduce the environmental impact of milk transportation. This includes using more efficient insulation materials, optimizing routes to reduce travel time, and exploring alternative energy sources, such as electric-powered refrigeration units.
Some companies are also experimenting with using renewable energy to power refrigeration systems, either through solar panels mounted on the tanker or by utilizing biodiesel as a more sustainable fuel option for the truck.
9. Conclusion: The Journey of Fresh Milk
The process of keeping milk cold during transportation is a complex interplay of technology, engineering, and careful planning. From high-quality insulation and pre-cooling at the farm to sophisticated monitoring systems and potential onboard refrigeration units, every aspect of the milk tanker is designed with one goal in mind: delivering fresh, safe milk to consumers.
Next time you pour yourself a glass of milk, take a moment to consider the incredible journey it took to reach you, and the meticulous care that went into ensuring it stayed cold and fresh every step of the way.
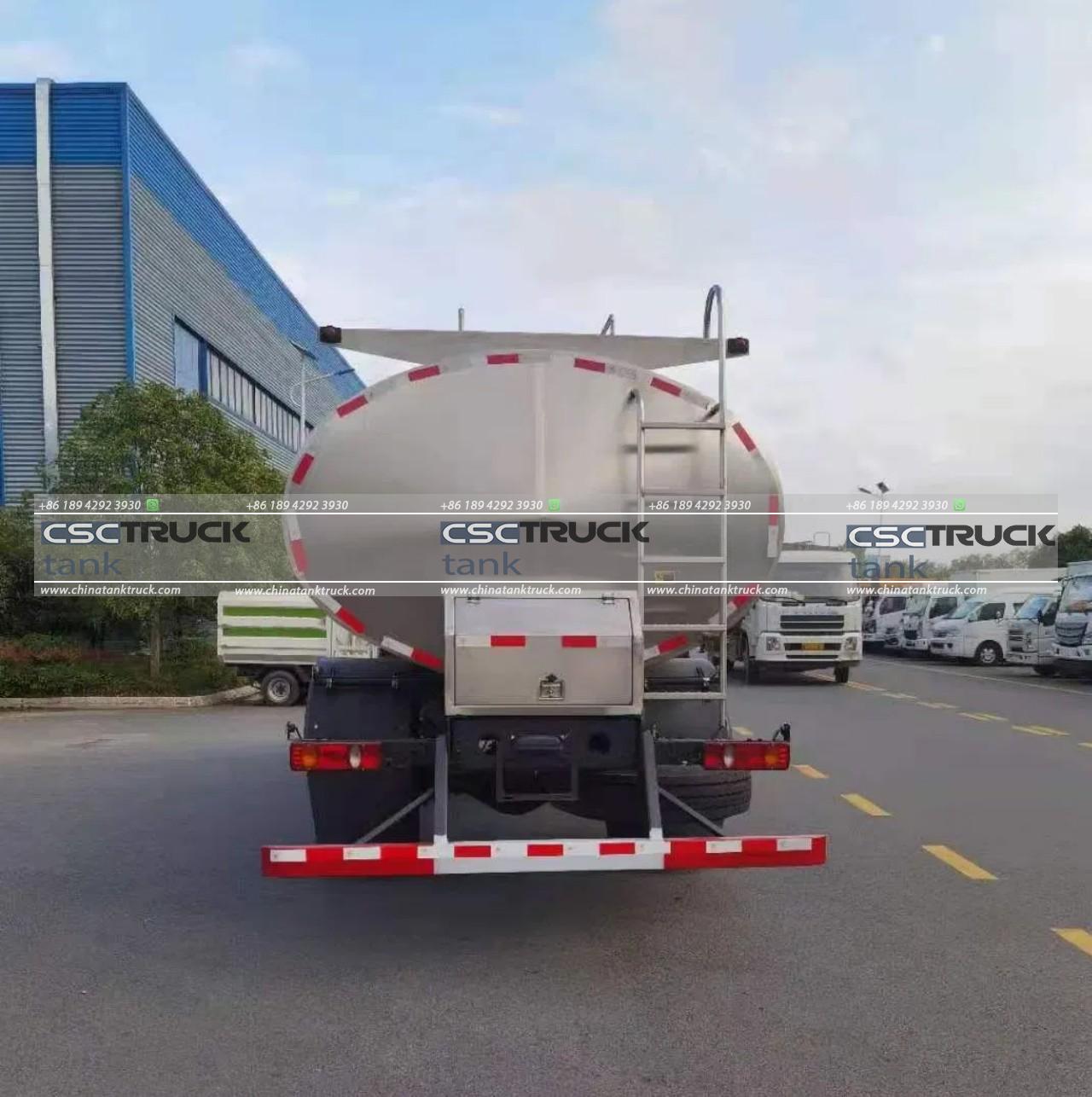