Do Fuel Tankers Have Pumps?
Fuel tankers play a crucial role in transporting various types of fuel, such as gasoline, diesel, and aviation fuel, from refineries to distribution points. One question that often arises is whether these tankers are equipped with pumps. The answer depends on the specific design of the tanker, the intended application, and the operational needs of the transportation process. This article explores the functionality of pumps in fuel tankers, their applications, and the technical considerations involved in their use.
Understanding Fuel Tankers
Fuel tankers are specialized vehicles designed to carry liquid fuels. They come in various sizes, from small trucks for local deliveries to large semi-trailers for long-distance hauling. The design of a fuel tanker includes several critical components:
1. Tank Body: The main compartment for storing fuel. It is usually constructed from aluminum or stainless steel to resist corrosion.
2. Compartments: Many fuel tankers have multiple compartments to carry different types of fuel simultaneously.
3. Valves and Hoses: These are used to load and unload the fuel.
4. Safety Features: These include vapor recovery systems, grounding mechanisms, and emergency shutoff valves.
One significant aspect of fuel tanker operation is how fuel is loaded into and unloaded from the tank, which is where pumps come into the picture.
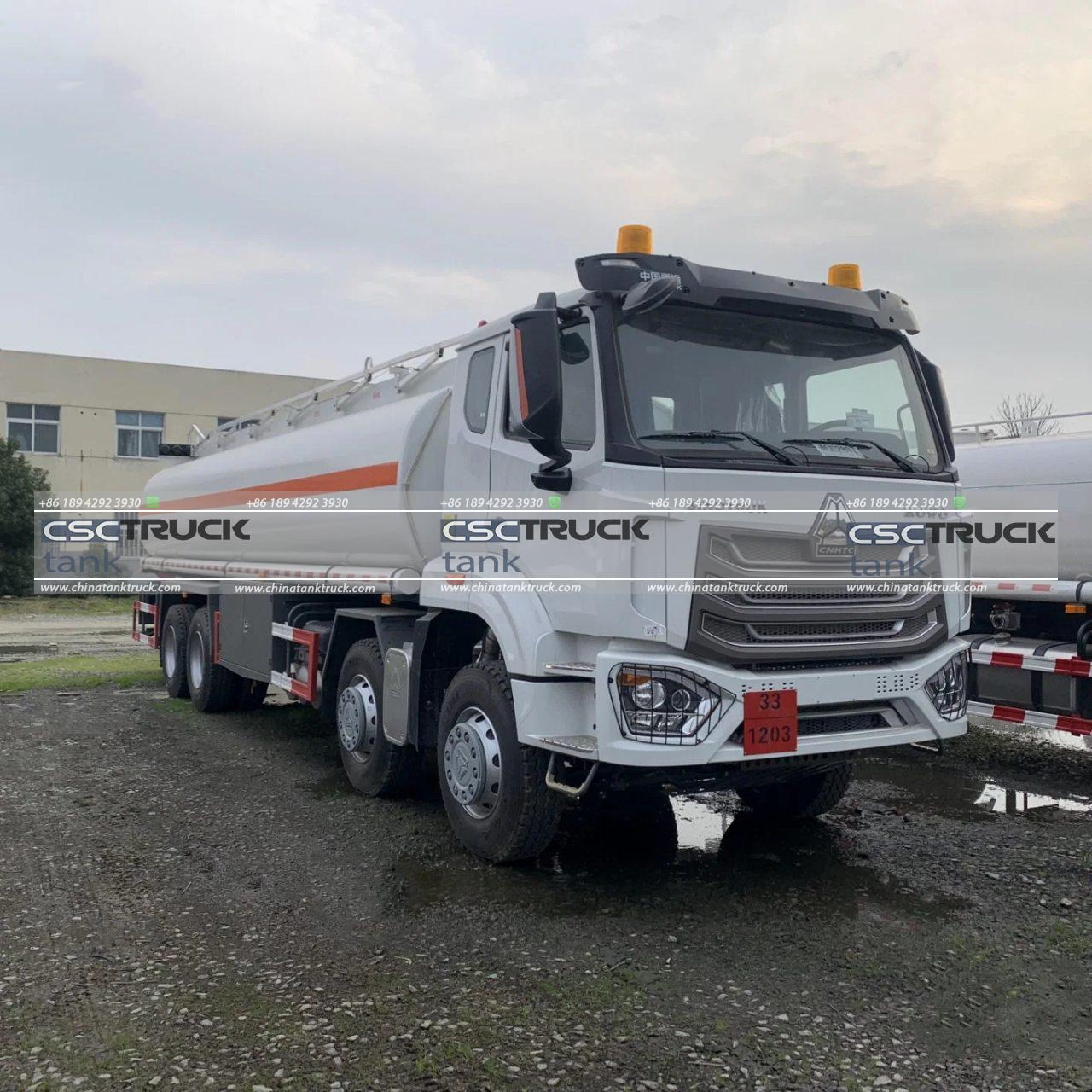
Do All Fuel Tankers Have Pumps?
Not all fuel tankers are equipped with pumps. Whether a pump is included depends on the intended use of the tanker and the unloading method employed. Broadly, fuel tankers can unload fuel using either a gravity-fed system or a pump-assisted system.
Gravity-Fed Systems
Gravity-fed systems rely on the natural force of gravity to move the fuel from the tanker to the receiving tank or facility. This system is common in situations where the delivery point is lower than the tanker, such as underground storage tanks at fuel stations.
Advantages of Gravity Systems:
– Simple design, reducing maintenance needs.
– Lower upfront costs since no pump is required.
– Effective in locations designed for gravity-based unloading.
Limitations:
– Inefficient when the receiving tank is at the same or a higher elevation than the tanker.
– Slower unloading process compared to pump-assisted systems.
Pump-Assisted Systems
Pump-assisted systems use mechanical pumps to transfer fuel actively from the tanker to the receiving tank. These pumps can be mounted on the tanker itself or installed at the delivery point.
Types of Pumps in Fuel Tankers:
1. Centrifugal Pumps: Common for high-volume transfers; they use rotational energy to move fuel quickly.
2. Positive Displacement Pumps: These include gear pumps or vane pumps, suitable for precise fuel delivery.
3. Diaphragm Pumps: Ideal for handling a variety of fuel types with minimal risk of leakage.
Advantages of Pump-Assisted Systems:
– Can pump fuel to tanks located at higher elevations than the tanker.
– Faster unloading times, increasing efficiency.
– Allows greater flexibility in delivery locations, including remote or uneven terrains.
Limitations:
– Higher maintenance requirements due to the mechanical complexity of pumps.
– Increased cost of tanker production and operation.
– Potential for pump failure, requiring backup unloading methods.

Applications of Pumps in Fuel Tankers
Pumps are more commonly found in fuel tankers designed for specific applications or challenging conditions. Here are some scenarios where pumps are essential:
1. Fuel Delivery to Remote Locations
In rural or remote areas, fuel tanks at delivery points may not be designed for gravity-fed systems. Pumps enable tankers to transfer fuel efficiently, regardless of terrain or elevation.
2. Industrial and Commercial Fueling
Fuel tankers used for industrial or commercial operations, such as fueling construction equipment or aircraft, often require pumps for precise delivery. These pumps ensure the right amount of fuel is quickly and safely delivered.
3. Emergency Response
Fuel tankers used in emergency response scenarios, such as supplying fuel to disaster-stricken areas or powering generators, need pumps to ensure rapid fuel deployment.
4. Aviation Refueling
Aviation fuel tankers almost always rely on pumps. Aircraft require precise amounts of fuel delivered at specific pressures, which gravity-fed systems cannot provide reliably.
Technical Considerations for Pumps in Fuel Tankers
Equipping a fuel tanker with a pump involves several technical considerations:
1. Compatibility with Fuel Types
The pump material must be compatible with the specific fuel type to prevent corrosion or degradation. For instance, aviation fuels may require pumps made from specialized materials to meet stringent safety standards.
2. Flow Rate and Pressure
The pump must deliver the required flow rate and pressure. High flow rates are critical for industrial or aviation applications, while lower flow rates may suffice for local fuel deliveries.
3. Power Source
Pumps in fuel tankers can be powered by:
– The vehicle’s engine (via a PTO or power take-off system).
– Independent power sources, such as hydraulic systems or electric motors.
Each option has its trade-offs in terms of cost, efficiency, and reliability.
4. Safety Features
Fuel transfer pumps must include safety features such as:
– Overpressure relief valves to prevent system failures.
– Flame arresters to reduce fire risks.
– Automatic shutoff mechanisms to prevent overflows.
5. Maintenance and Durability
Given the demanding operating conditions, pumps must be robust and require minimal maintenance. Regular inspections are necessary to ensure safe and efficient operation.
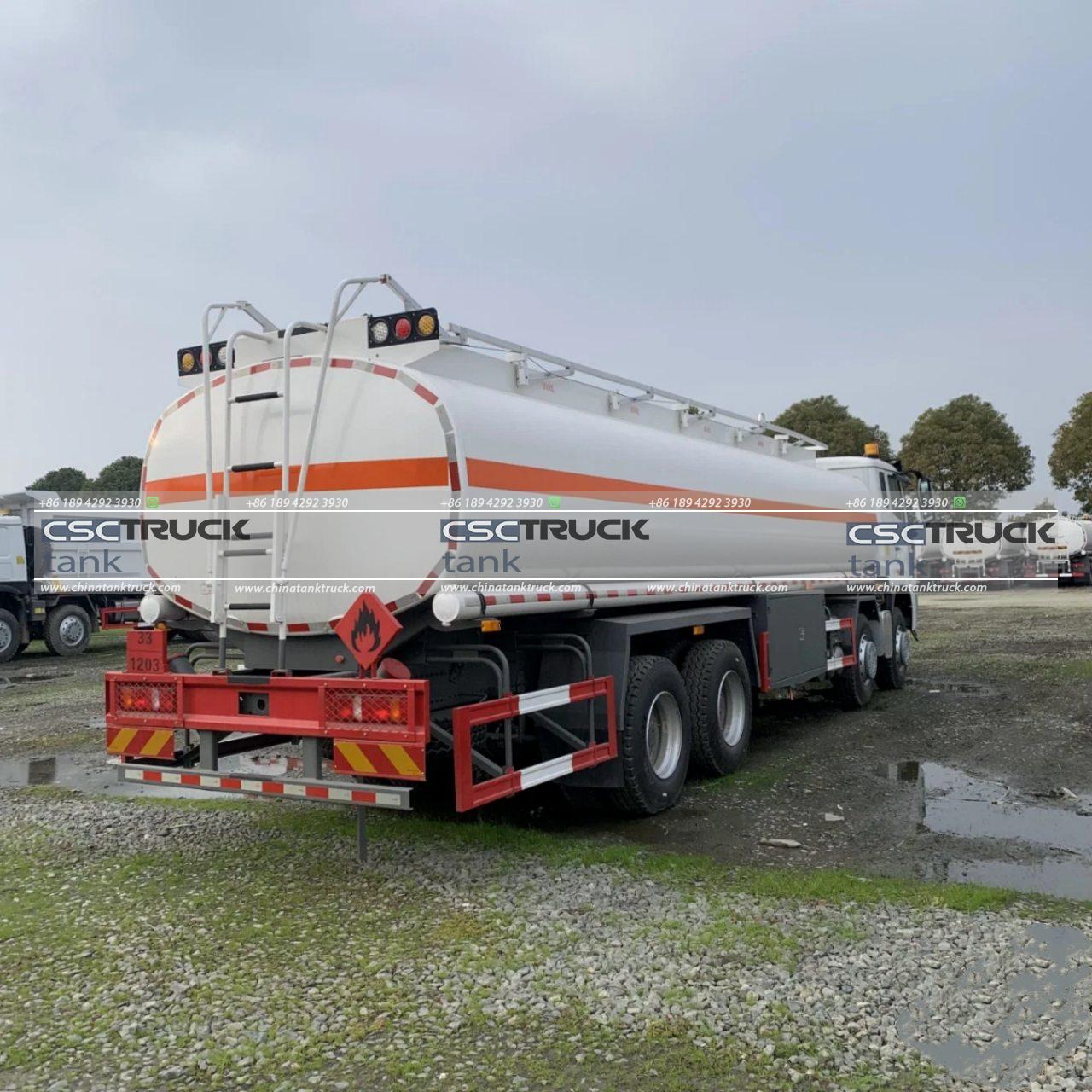
Challenges of Using Pumps in Fuel Tankers
While pumps offer numerous advantages, they also introduce challenges:
1. Cost
Installing and maintaining pumps increases the overall cost of the tanker. Operators must weigh this cost against the benefits of faster and more flexible fuel delivery.
2. Complexity
Pumps add complexity to the fuel tanker’s operation. Drivers and operators need proper training to handle pump systems effectively.
3. Potential for Failure
Mechanical pumps can fail due to wear and tear, fuel contamination, or improper maintenance. Backup systems, such as gravity-fed mechanisms, are often included to mitigate these risks.
Regulatory and Safety Considerations
The inclusion of pumps in fuel tankers is subject to regulatory guidelines, which vary by region and fuel type. Key considerations include:
– Compliance with environmental standards, such as vapor recovery requirements.
– Adherence to safety regulations, including grounding and bonding to prevent static electricity.
– Certification of pumps for use with specific fuel types.
Operators must ensure that both the tanker and its pump system meet these regulations to avoid fines and operational disruptions.
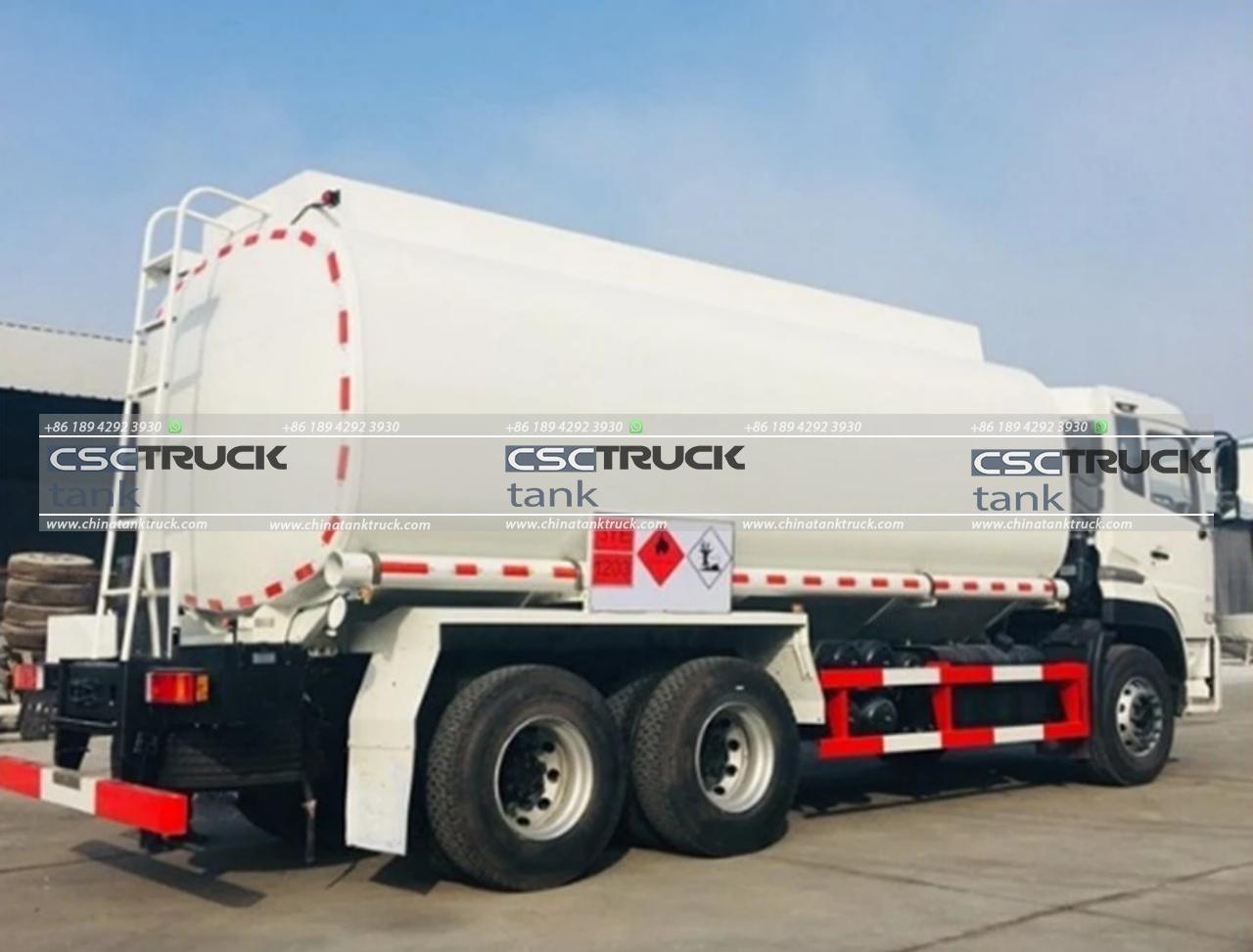
Conclusion
Fuel tankers may or may not have pumps, depending on their intended use, operational requirements, and the conditions at delivery points. Gravity-fed systems are sufficient for many standard fuel delivery scenarios, while pump-assisted systems provide the versatility needed for challenging or specialized applications.
Understanding the role of pumps in fuel tankers is essential for operators, engineers, and logistics professionals. The decision to include a pump depends on balancing the costs, benefits, and technical requirements of the fuel delivery process. As technology advances, more efficient and safer pump systems are likely to become an integral part of fuel tanker design, meeting the evolving demands of the energy sector.