Are Tanker Trucks Pressurized?
Tanker trucks play a vital role in transporting liquids, gases, and even dry bulk materials over long distances. They are common sights on highways and are often recognized for their large, cylindrical storage tanks mounted on a truck chassis. One common question that arises when discussing these vehicles is whether tanker trucks are pressurized. The answer, however, depends on the type of tanker truck, the nature of the cargo it is carrying, and the safety and operational requirements.
This article explores the intricacies of tanker truck design, differentiating between pressurized and non-pressurized tanker trucks, their specific applications, and the importance of pressure control in ensuring the safe transportation of various goods.
Types of Tanker Trucks
Tanker trucks are classified based on the materials they transport, which broadly fall into 3 categories:
2. Gas Tanker Trucks: These carry gases like propane, liquefied natural gas (LNG), and compressed natural gas (CNG).
3. Dry Bulk Tanker Trucks: These are used for transporting powders, grains, and other bulk solid materials.
Each type of tanker truck is designed with different construction materials, safety mechanisms, and, most importantly, pressure requirements. Let’s explore how pressure plays a role in different tanker trucks.
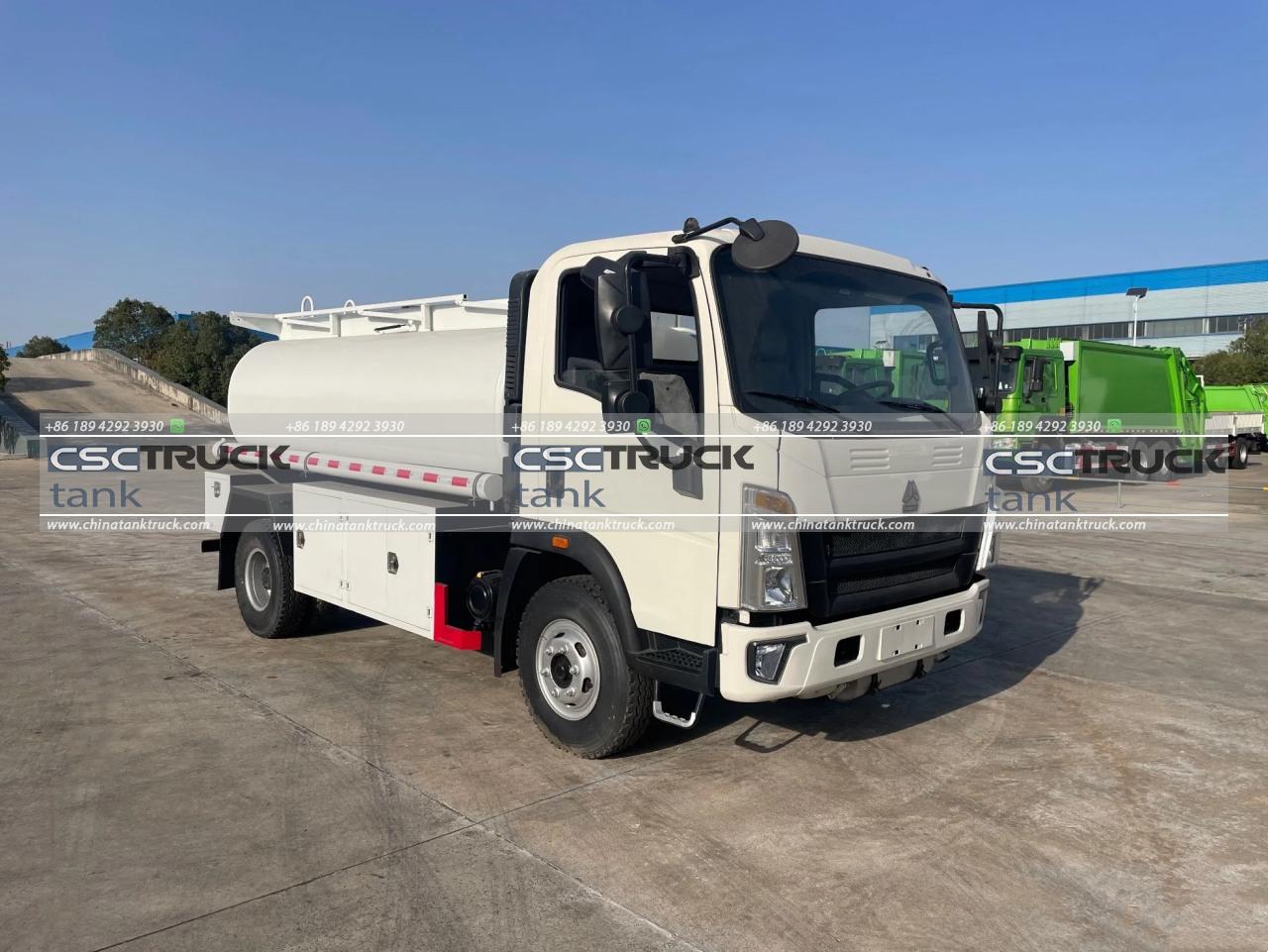
Pressurized vs. Non-Pressurized Tanker Trucks
The key factor that distinguishes pressurized from non-pressurized tanker trucks is whether they are built to contain cargo under high or low pressure. This distinction has profound implications for the truck’s construction, safety features, and operational protocols.
1. Non-Pressurized Tanker Trucks
Non-pressurized tanker trucks are designed to transport liquids or gases that are not highly volatile and do not require special containment measures under pressure. These trucks are primarily used to transport liquids like milk, water, and certain chemicals that do not need to be kept under specific pressure levels.
Construction and Features:
– Simple Cylindrical Design: The tanks are typically cylindrical with a flat or slightly domed top and bottom. They are designed for durability but are not reinforced to withstand significant internal pressure.
– Venting Mechanism: Since these tanks are not pressurized, they include a venting system to allow the internal pressure to remain at or near atmospheric pressure. This prevents pressure buildup due to temperature fluctuations, which can occur when liquids expand or contract.
– Flexible Loading and Unloading: Non-pressurized tanks allow for gravity-fed or pumped loading and unloading. Because they are not pressurized, more straightforward systems can be used for moving the cargo in and out of the tank.
Applications:
– Fuel Trucks: Fuel delivery trucks that transport gasoline or diesel are often non-pressurized. The fuel remains at atmospheric pressure, though specialized compartments and safety valves prevent leaks or spills.
– Food-Grade Liquid Transport: Trucks that transport food-grade liquids, such as milk or edible oils, are typically non-pressurized since these liquids do not require high pressure to maintain their integrity.
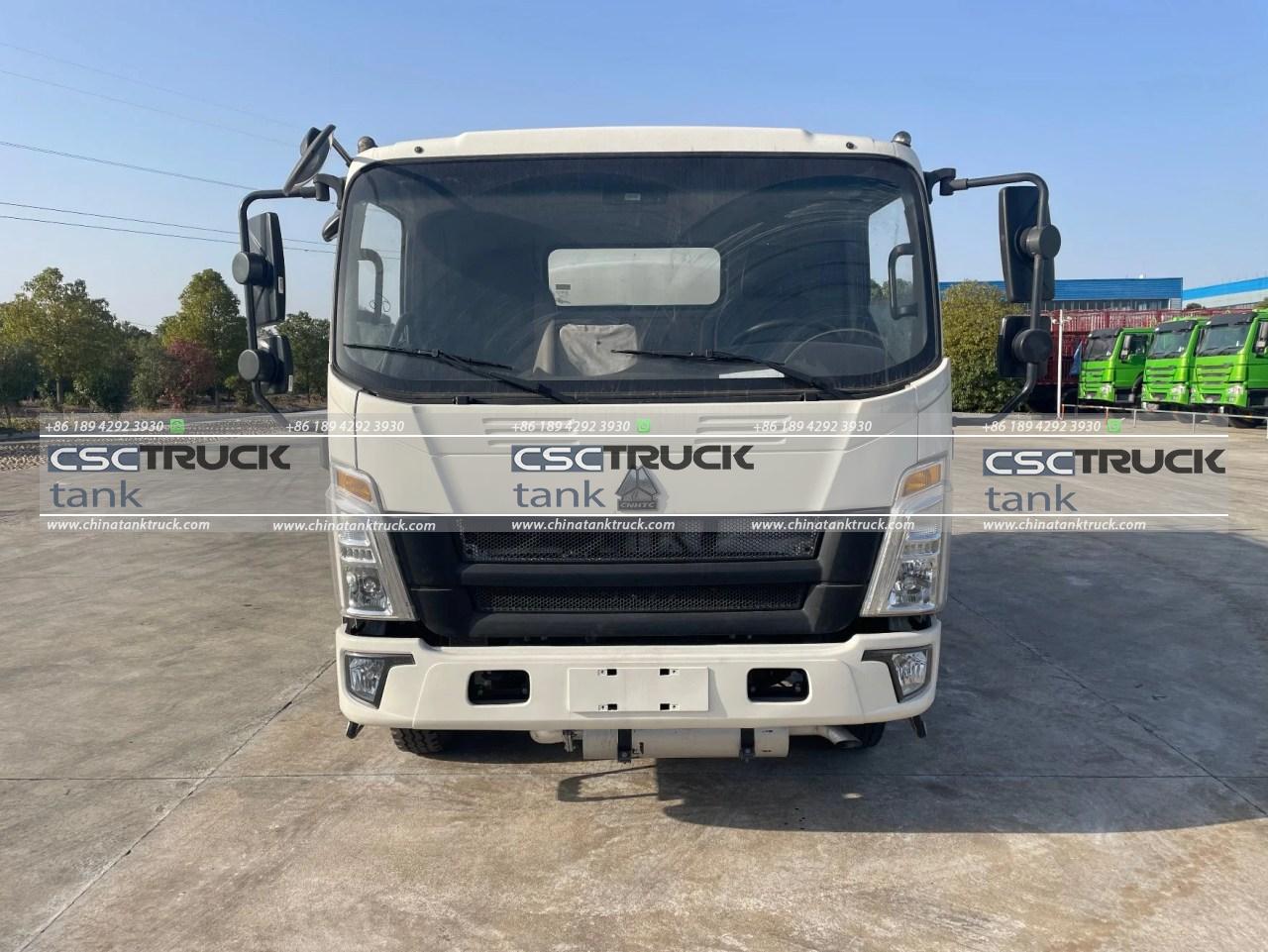
2. Pressurized Tanker Trucks
Pressurized tanker trucks are engineered to transport volatile liquids or gases that must be kept under a specific pressure to remain in a stable state. These trucks feature a reinforced structure capable of withstanding the pressure exerted by the cargo.
Construction and Features:
– Reinforced Structure: The tanks are made from stronger materials, such as steel alloys, and are heavily reinforced to withstand high internal pressure. The construction ensures that even in the event of a minor accident or bump, the tank won’t rupture or leak.
– Pressurization System: Pressurized tanks are equipped with a built-in system that maintains the internal pressure at a required level. This may involve using pumps, valves, and pressure regulators to ensure the pressure remains constant.
– Safety Valves: To prevent over-pressurization, which can lead to catastrophic failure, these trucks are outfitted with safety valves. In case the pressure inside the tank exceeds safe levels, the safety valves release some of the gas or liquid to prevent damage.
Applications:
– Gas Transport: Trucks that carry compressed gases such as propane, LNG, or ammonia are pressurized. The pressurization is essential because many of these gases are stored in liquid form under high pressure. If the pressure were not maintained, the gas could revert to its gaseous state, causing dangerous expansion and potential leaks.
– Cryogenic Tankers: These trucks transport extremely low-temperature liquids like liquid nitrogen or oxygen. In cryogenic tankers, both temperature and pressure need to be precisely controlled to keep the cargo in a liquid state. The pressurization ensures the gas remains in liquid form even at very low temperatures.
3. Pressurization in Dry Bulk Tanker Trucks
While it might seem counterintuitive, some dry bulk tanker trucks are pressurized. These trucks carry powdered or granular materials like cement, flour, or grains. The pressurization system helps in unloading these materials efficiently.
Features:
– Pneumatic Unloading: Pressurized air is used to force the dry materials out of the tank. This system is more efficient than gravity unloading, especially for heavy or fine powders that would be difficult to move otherwise.
– Pressure Regulation: While the pressure in dry bulk tankers is not as high as in gas tankers, it still plays a critical role in unloading the cargo. The system must be carefully managed to avoid rupturing the tank or causing an uncontrolled release of the material.
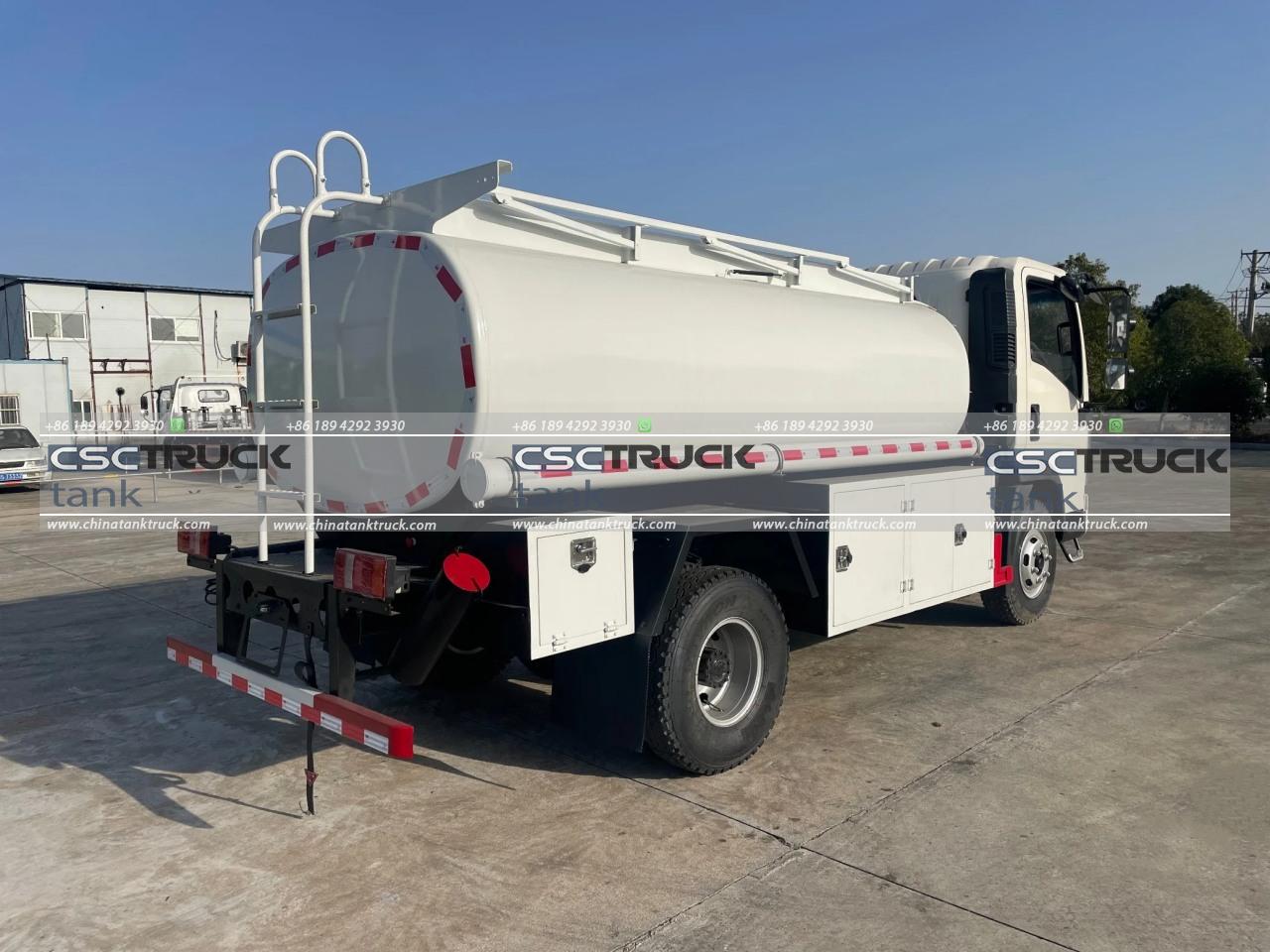
Why Are Some Tanker Trucks Pressurized?
The decision to pressurize a tanker truck boils down to the cargo’s chemical and physical properties. Many gases, for example, require high pressure to remain in liquid form, as this state is more space-efficient for transportation. Additionally, pressurized tanks offer better protection against leaks, making them suitable for hazardous materials.
For liquids that can be transported at atmospheric pressure, such as water, pressurization is unnecessary. Non-pressurized tanks are simpler, cheaper to manufacture, and easier to maintain, making them suitable for less hazardous or stable cargo.
Safety Considerations
The use of pressurization in tanker trucks introduces several safety considerations. Pressurized tanks must be regularly inspected for structural integrity, as even a minor flaw in the tank’s wall can lead to dangerous leaks or explosions. Specialized training is also required for drivers of pressurized tanker trucks, as they need to understand how to manage the pressurization system and what to do in the event of a system failure.
In addition to regular maintenance and training, pressurized tanker trucks are subject to stringent regulations. Agencies like the Department of Transportation (DOT) in the U.S. or the European Agreement concerning the International Carriage of Dangerous Goods by Road (ADR) in Europe enforce safety protocols, requiring regular inspections and certifications for pressurized tanks.
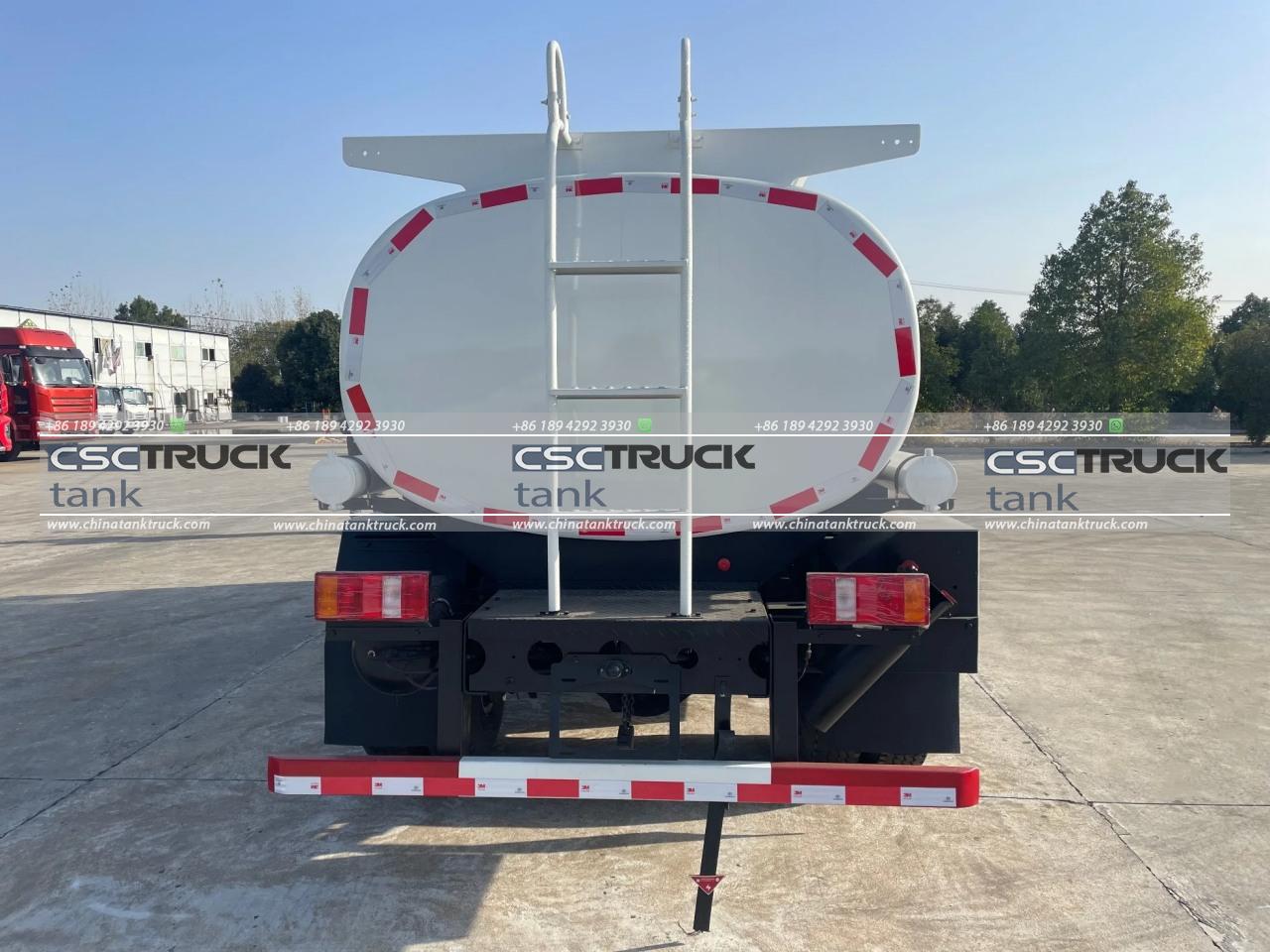
Conclusion
Tanker trucks can be either pressurized or non-pressurized, depending on the type of cargo they carry. While non-pressurized trucks are suitable for stable liquids like water and milk, pressurized trucks are necessary for gases and volatile liquids that must remain under specific conditions to ensure safe transportation. The pressurization of tanker trucks is an essential aspect of their design, ensuring the safety of both the cargo and the public while in transit.