Are Milk Tankers Baffled?
Milk tankers are essential vehicles in the dairy industry, tasked with transporting large volumes of milk from farms to processing plants. These specialized trucks are designed to maintain the quality of the milk during transit by keeping it cold and preventing contamination. One important aspect of their design that often comes up in discussions is whether these tankers are “baffled” or not.
Understanding Baffles in Tankers
Before diving into whether milk tankers are baffled, it’s essential to understand what baffles are and why they are used in tanker trucks. Baffles are panels or barriers installed inside the tank to reduce the movement of liquid inside it. When a liquid is transported, it tends to move or “slosh” around inside the tank due to inertia, especially when the vehicle accelerates, decelerates, or turns. This sloshing can create instability, making the vehicle harder to control and increasing the risk of accidents.
In many types of tankers, such as those transporting fuel or chemicals, baffles are used to mitigate this sloshing effect. They compartmentalize the liquid, breaking it up into smaller sections and reducing the force of the liquid’s movement. This makes the vehicle more stable and easier to handle, particularly during sudden stops or sharp turns.
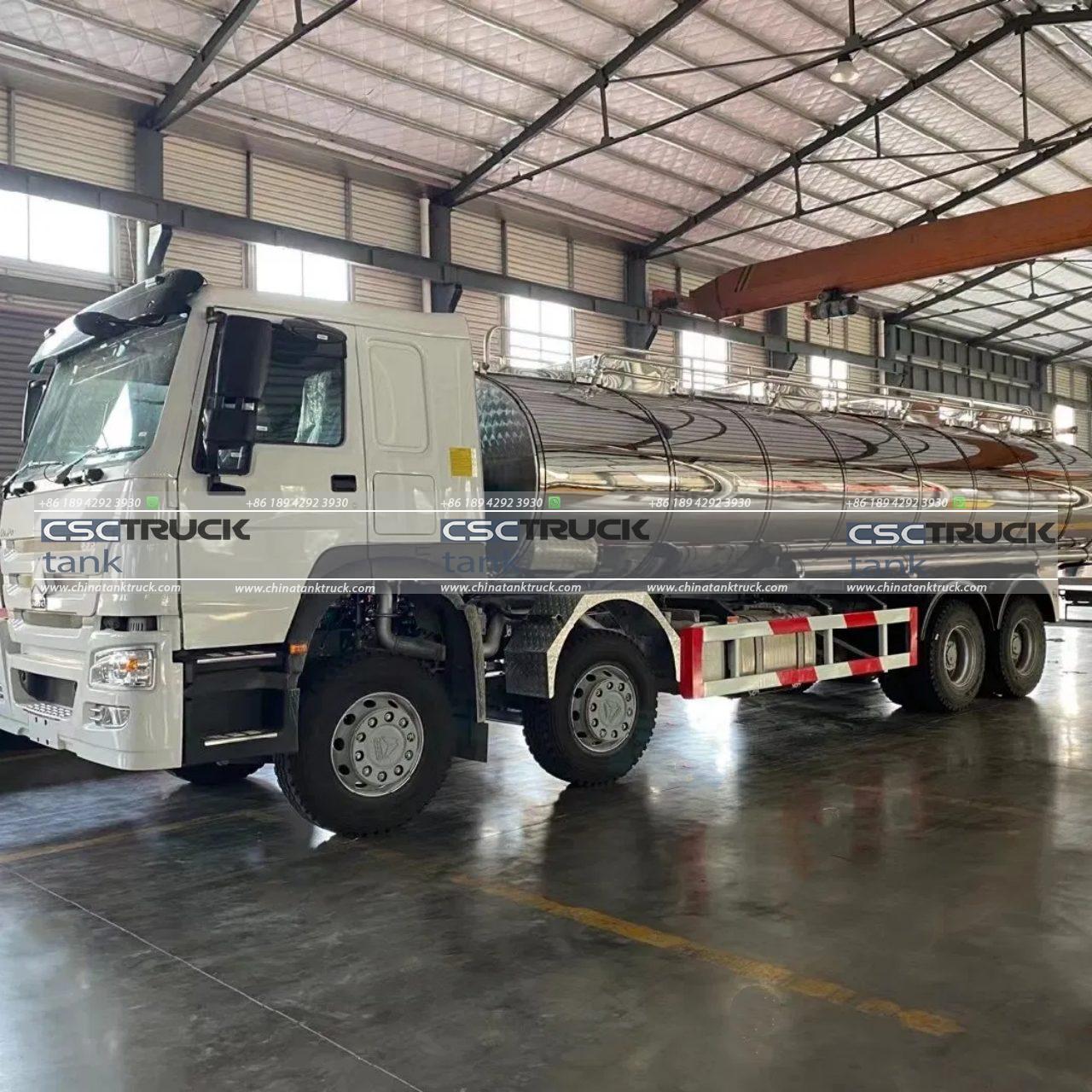
The Unique Nature of Milk Transport
Milk, however, presents unique challenges that make the use of baffles in milk tankers less straightforward. Unlike fuel or chemicals, milk is a perishable product that must be kept at a consistent temperature and handled with care to avoid spoilage and contamination. The design of milk tankers reflects these requirements, with an emphasis on hygiene and temperature control.
The primary reason that milk tankers are not baffled is the need to maintain strict sanitation standards. Baffles, while effective at reducing liquid movement, introduce additional surfaces inside the tank that can be difficult to clean thoroughly. Milk is a nutrient-rich liquid that can support the growth of bacteria if not properly cleaned from all surfaces. The presence of baffles would create additional nooks and crannies where milk residues could accumulate, increasing the risk of bacterial contamination. For this reason, milk tankers are typically designed without baffles, allowing for easier cleaning and ensuring that the interior of the tank can be thoroughly sanitized.
Alternative Methods for Managing Liquid Movement
Given that baffles are not used, milk tankers must rely on other methods to manage the movement of the liquid and ensure the safe transport of milk. One common approach is to design the tanks with a lower center of gravity. This helps to reduce the impact of sloshing by making the tanker more stable overall.
In addition, milk tankers often use a multi-compartment design. Instead of a single large tank, the tanker is divided into smaller compartments, each holding a portion of the total milk load. While this doesn’t eliminate sloshing, it reduces the volume of liquid in each compartment, thereby diminishing the effect of movement. These compartments are usually separated by bulkheads rather than baffles, which serve to prevent the milk from moving freely between compartments but still allow for easier cleaning.
The compartments also have another advantage: they allow for the collection of milk from multiple farms without mixing different batches of milk. This is important for quality control, as milk from different sources may vary in composition, and processors may want to keep these batches separate until testing can be done.
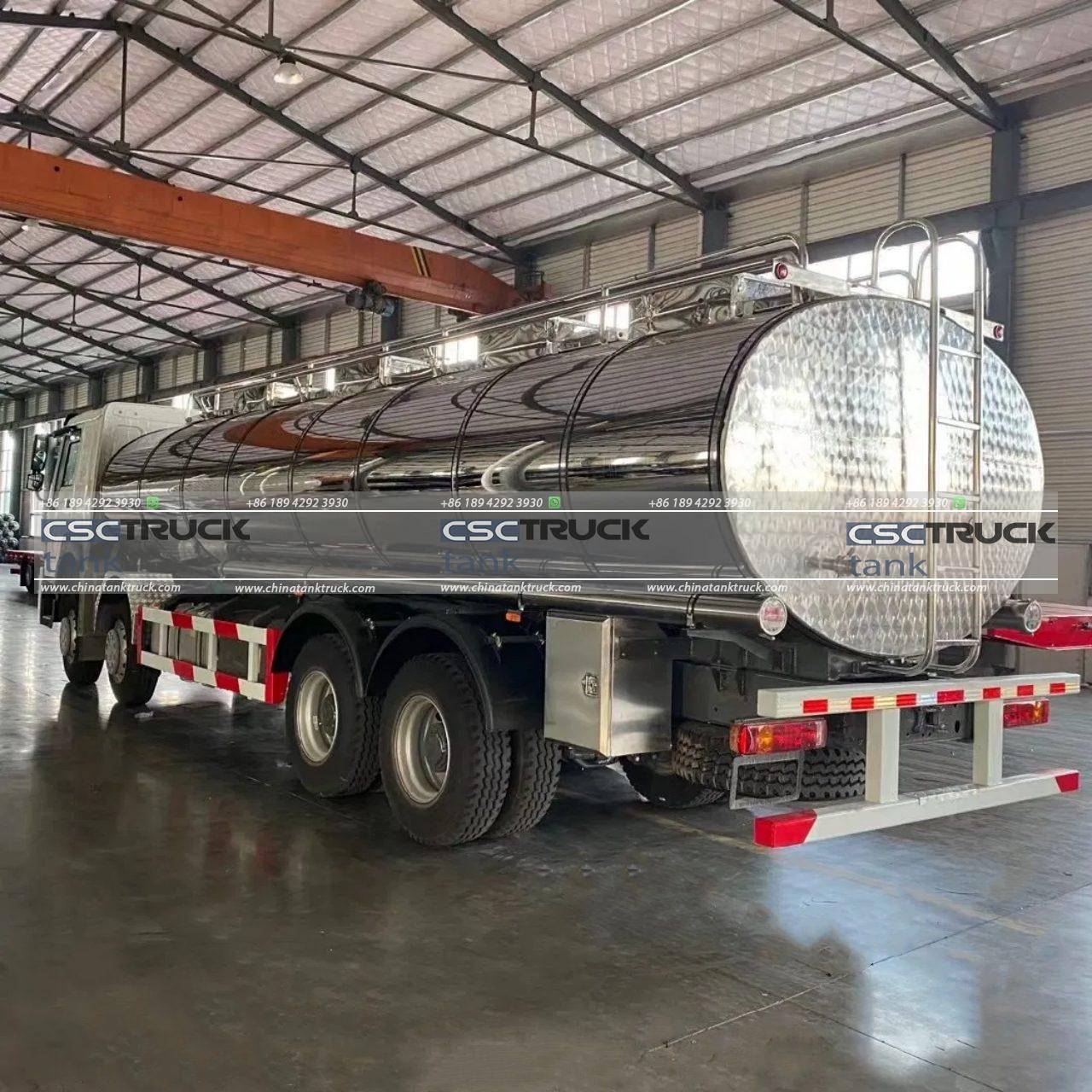
The Role of Technology in Milk Tanker Design
Modern milk tankers often incorporate advanced technology to further enhance the safety and efficiency of milk transport. For example, some tankers are equipped with electronic systems that monitor the temperature of the milk throughout the journey. If the temperature begins to rise, indicating a potential problem with the refrigeration system, the driver can be alerted immediately, allowing for quick action to prevent spoilage.
Another technological innovation is the use of air-ride suspension systems. These systems help to reduce the amount of shock and vibration that the tanker experiences during transit, which in turn reduces the movement of the milk inside the tank. By providing a smoother ride, air-ride suspension contributes to the overall stability of the vehicle and helps to protect the quality of the milk.
The Impact of Regulation on Milk Tanker Design
The design and operation of milk tankers are subject to strict regulations, particularly in terms of sanitation and temperature control. Regulatory bodies, such as the Food and Drug Administration (FDA) in the United States, set out specific guidelines for the construction, cleaning, and maintenance of milk tankers. These regulations are designed to ensure that the milk remains safe for consumption from the time it leaves the farm until it reaches the processing plant.
One key regulation is the requirement for tankers to be constructed from materials that are easy to clean and resistant to corrosion. Stainless steel is the material of choice for most milk tankers, as it is durable, non-reactive, and can be polished to a smooth finish that resists bacterial growth. The absence of baffles aligns with these regulatory requirements, as it simplifies the cleaning process and reduces the risk of contamination.
Conclu
sion
Milk tankers play a crucial role in the dairy supply chain, ensuring that fresh milk can be transported safely from farms to processing plants. While the use of baffles is common in many types of tankers, milk tankers are an exception due to the unique challenges posed by transporting a perishable, nutrient-rich liquid. The need for thorough cleaning and the prevention of contamination outweighs the benefits of baffles, leading to alternative design features such as multi-compartment tanks and advanced suspension systems.
In the end, the design of milk tankers reflects a careful balance between safety, efficiency, and hygiene. By understanding why milk tankers are not baffled, we gain insight into the complex considerations that go into the transportation of one of our most important food products.