Are ISO Tanks Temperature Controlled?
ISO tanks, also known as intermodal tanks, are versatile and durable containers used for the transportation and storage of bulk liquids, gases, and powders across land and sea. Their robust design and ability to seamlessly transfer between different modes of transport—ships, trains, and trucks—make them essential for global trade. One key question often arises regarding these containers: Are ISO tanks temperature-controlled? The short answer is that some are, but the complexity lies in understanding the types, methods, and applications of temperature control in ISO tanks.
What are ISO Tanks?
ISO tanks adhere to standards set by the International Organization for Standardization (ISO), ensuring uniformity in their size, shape, and specifications. They typically consist of a cylindrical stainless-steel vessel encased in a protective layer. This robust construction makes them suitable for carrying hazardous and non-hazardous liquids, gases, and powders, including chemicals, food-grade products, petroleum products, and cryogenic gases.
The capacity of ISO tanks typically ranges between 17,500 liters and 26,000 liters, although variations exist based on the tank’s intended use. ISO tanks are also designed to be reusable, environmentally friendly, and highly durable, often lasting for over 20 years with proper maintenance.
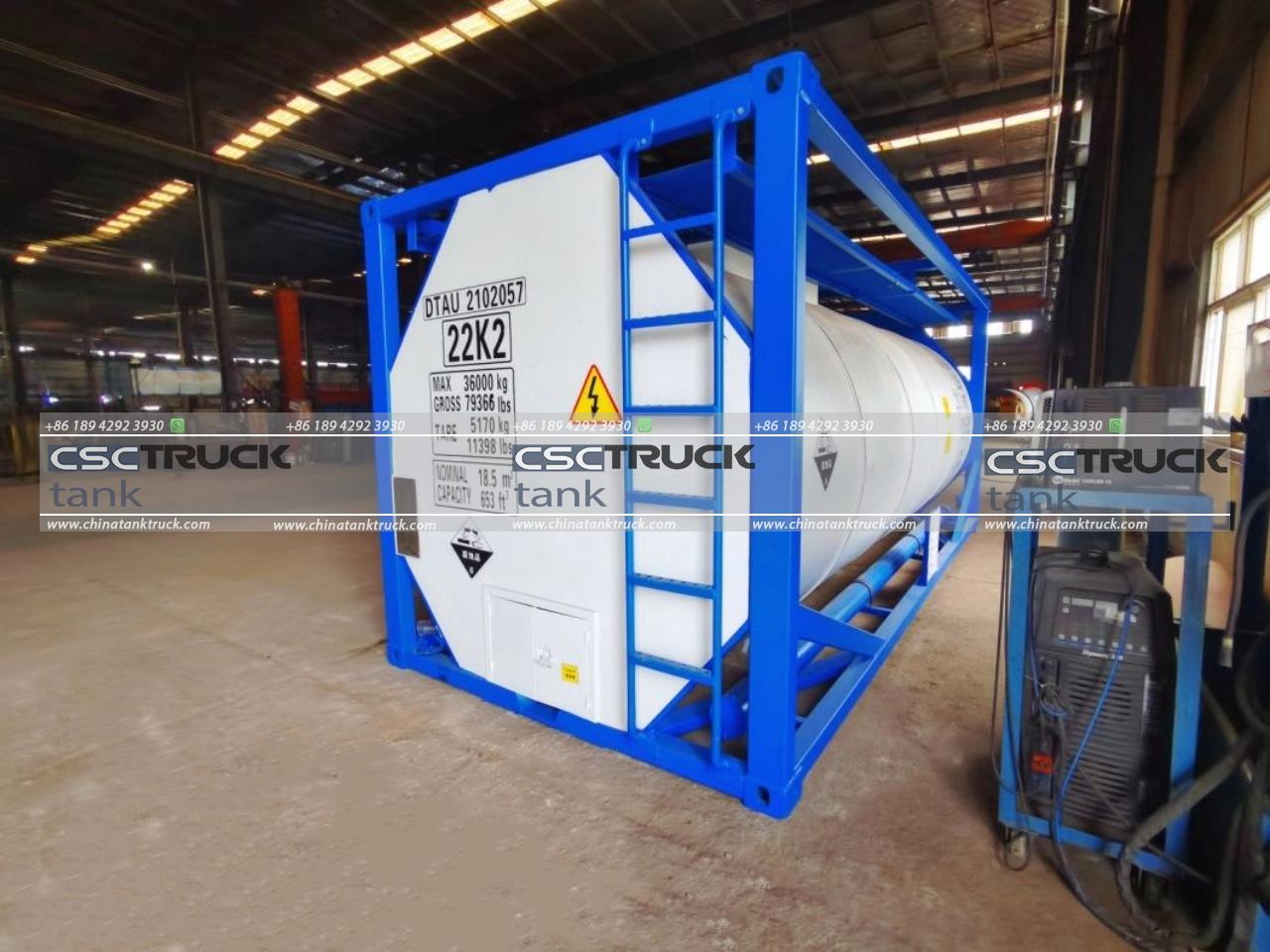
Why Temperature Control is Necessary
The need for temperature control during transportation or storage stems from the nature of the products being carried. Many substances, especially chemicals, food products, and pharmaceuticals, can be sensitive to temperature variations. For instance:
– Chemicals: Some chemicals are volatile and reactive under extreme temperatures, posing safety risks or degrading in quality.
– Food Products: Beverages like wine, milk, and juices require strict temperature management to prevent spoilage or contamination.
– Pharmaceuticals: Temperature-sensitive vaccines, biologics, and drugs require precise temperature ranges to maintain their efficacy and safety.
Given the diversity of substances transported in ISO tanks, it’s clear why temperature control can be essential.
Types of ISO Tanks with Temperature Control
ISO tanks come in different configurations, and not all are temperature-controlled. However, specific tanks are designed for this purpose. Here are the primary types of ISO tanks that offer temperature regulation:
1. Refrigerated ISO Tanks (Reefer Tanks)
  Refrigerated ISO tanks, often called “reefer tanks,” are used to transport temperature-sensitive liquids. These tanks come equipped with cooling systems designed to maintain specific low temperatures. The cooling system can either be mechanical, powered by electricity, or rely on passive methods such as insulation or phase-change materials (PCMs).
  Reefer tanks are typically used to transport food products like dairy, beverages, and other perishable goods, where maintaining low temperatures during transportation is essential to preserve quality and prevent spoilage.
2. Heated ISO Tanks
  Some ISO tanks are equipped with heating systems that allow for the transport of substances that need to stay above certain temperatures to avoid solidifying, gelling, or degrading. The heating methods can vary:
  – Electric Heating: Electric heating elements are built into the tank to keep the product within the desired temperature range. This method is often used for transporting chemicals that need to stay in a liquid state or viscous products like certain oils.
  – Steam Heating: Some ISO tanks have steam heating coils, which allow for steam to be introduced into the tank’s jacket to warm the contents. Steam-heated tanks are often used for transporting products like bitumen, waxes, and food-grade liquids such as certain oils and fats that must remain warm for easy offloading.
  – Thermal Fluids: Another option is to use thermal fluids that circulate within a jacket surrounding the tank, providing controlled heat.
3. Cryogenic ISO Tanks
  Cryogenic ISO tanks are designed for the transport of gases in liquid form at very low temperatures. These tanks are typically used to carry gases such as liquid oxygen, nitrogen, argon, and liquefied natural gas (LNG). Cryogenic tanks maintain temperatures as low as -196°C, ensuring that gases remain in their liquid state during transportation.
  The construction of these tanks includes multi-layer insulation, and they rely on passive temperature control methods to minimize heat transfer and maintain the required ultra-low temperatures. Vacuum insulation is often employed to further reduce thermal conductivity, making them highly efficient for transporting cryogenic products.
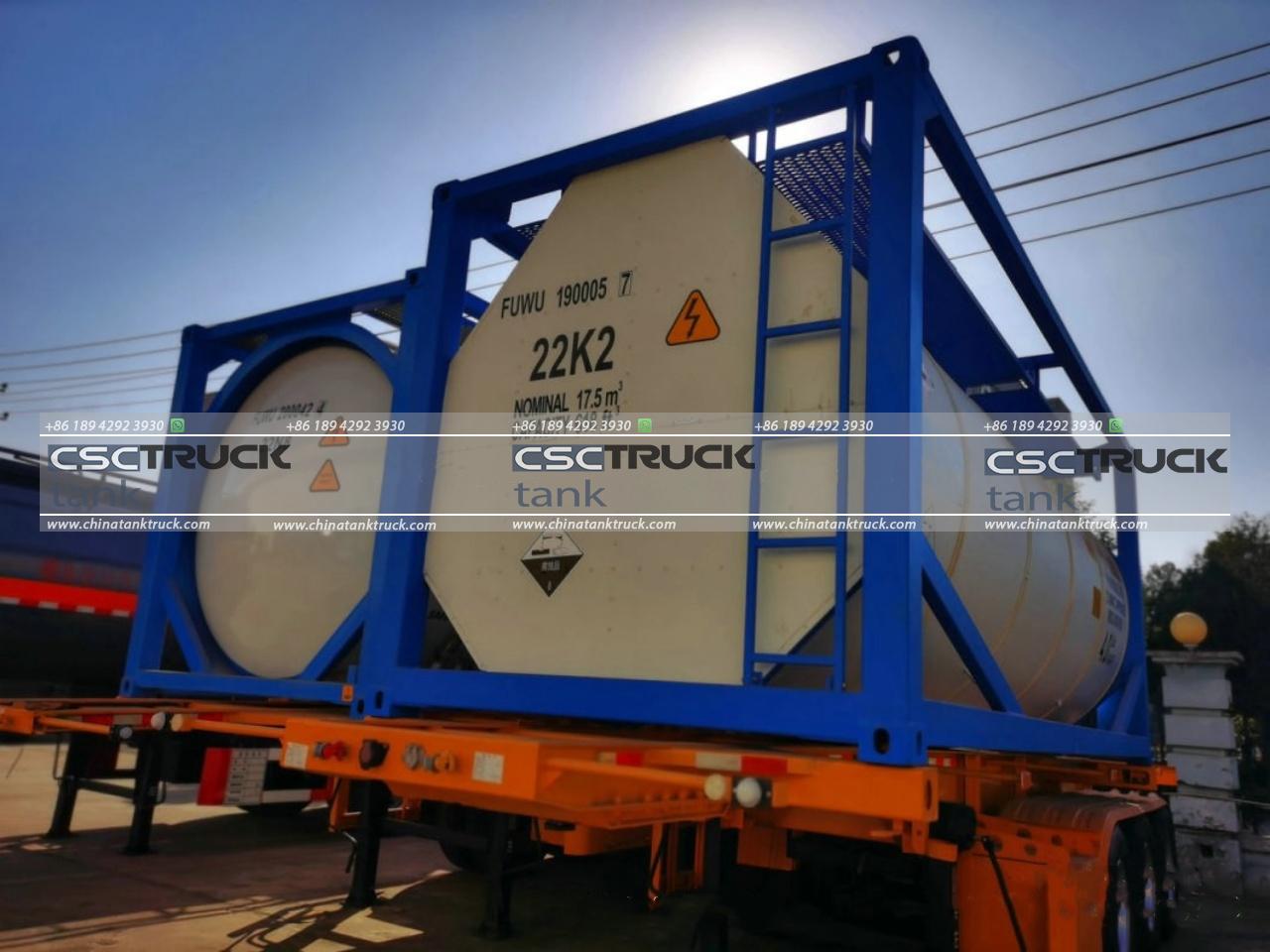
Methods of Temperature Control in ISO Tanks
Temperature control in ISO tanks is not one-size-fits-all; the method depends on the product being transported and the type of ISO tank used. Below are some common methods of temperature control:
1. Insulation
  Many ISO tanks rely on insulation to maintain a stable temperature. Insulated ISO tanks, without active heating or cooling, are designed to slow down the rate of heat exchange between the cargo and the environment. Insulation is crucial for maintaining the internal temperature of substances that are either highly sensitive to external temperatures or are stored for long durations.
2. Mechanical Temperature Control Systems
  For temperature-sensitive products that require precise control, active temperature control systems are installed. These can be powered by external energy sources such as electricity or generators. For reefer tanks, mechanical refrigeration systems help maintain low temperatures, while heated ISO tanks use electric or steam-powered heating elements.
3. Phase-Change Materials (PCMs)
  Another innovative method used in some ISO tanks involves phase-change materials, which can absorb or release heat at specific temperatures. When the temperature rises above or falls below a predetermined threshold, the material undergoes a phase change (solid to liquid or vice versa), helping maintain a stable temperature inside the tank.
4. Steam or Electric Heating
  As mentioned earlier, heated tanks may use steam or electric coils to maintain the required internal temperature. This method is effective for transporting substances that need to remain in a liquid state or at a specific viscosity, such as heavy oils, certain chemicals, or food products like chocolate or syrups.
Applications of Temperature-Controlled ISO Tanks
Temperature-controlled ISO tanks are used across a range of industries, including:
– Food and Beverage: Reefer tanks are vital for transporting juices, dairy products, beer, and wine, ensuring that temperature fluctuations don’t affect quality during transit.
– Chemicals: Temperature-sensitive chemicals, especially those that could become hazardous or unstable when exposed to incorrect temperatures, are often transported in heated or cooled tanks.
– Pharmaceuticals: The pharmaceutical industry relies heavily on temperature-controlled ISO tanks to transport drugs, vaccines, and other medical supplies that must remain within a narrow temperature range to retain their effectiveness.
– Cryogenic Gases: Industrial gases used in medical, industrial, and energy sectors, such as LNG and liquid oxygen, are often transported in cryogenic ISO tanks that maintain ultra-low temperatures.
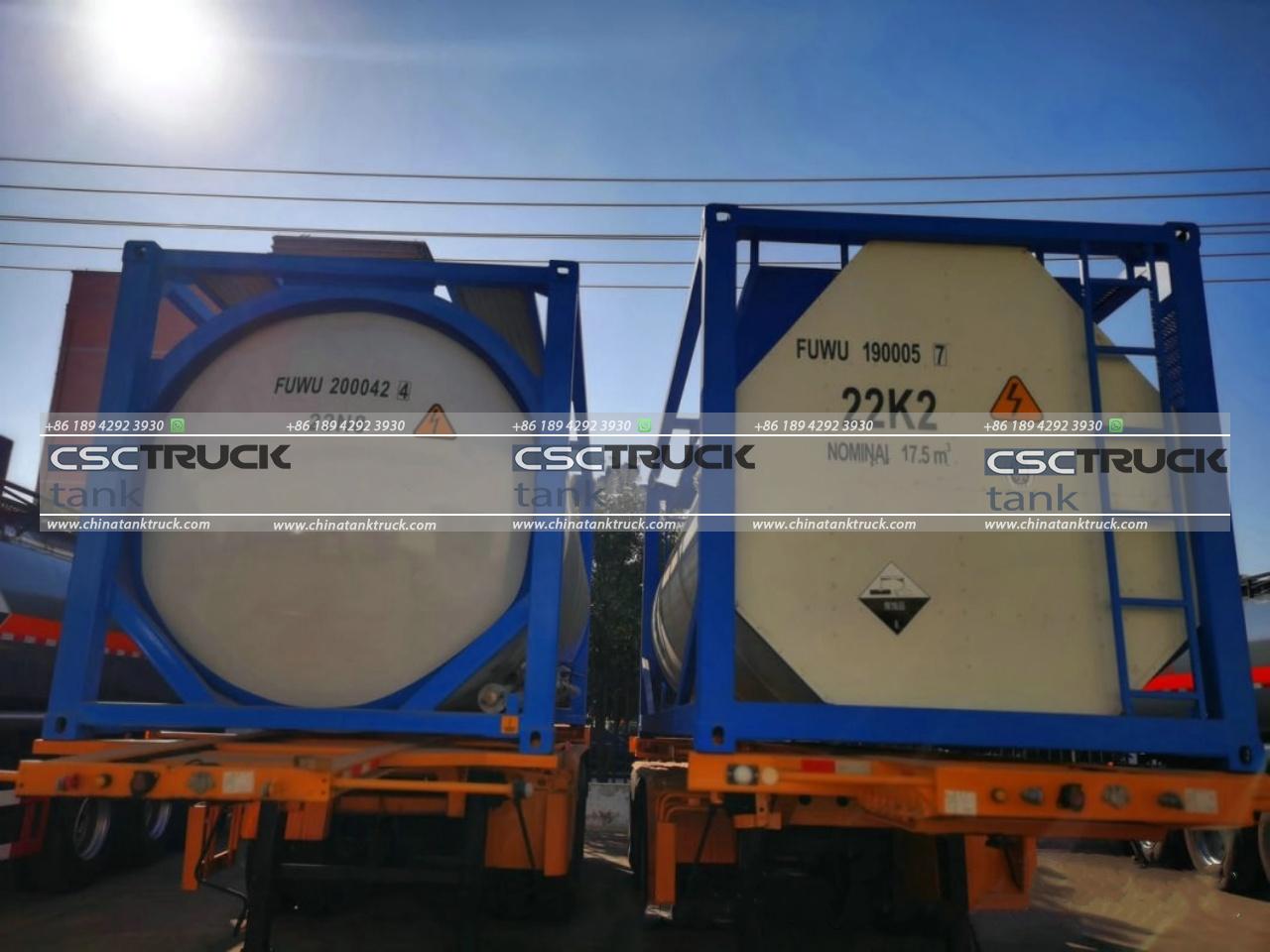
Conclusion
Not all ISO tanks are temperature-controlled, but specific types—such as reefer tanks, heated tanks, and cryogenic tanks—are designed for temperature-sensitive cargo. Whether through insulation, active cooling and heating systems, or advanced technologies like phase-change materials, ISO tanks provide an effective means of transporting temperature-sensitive goods across the globe. Their role in preserving product quality, ensuring safety, and meeting regulatory requirements highlights the importance of temperature-controlled ISO tanks in modern logistics and trade.