What is a Milk Truck?Â
Milk trucks, sometimes known as milk tankers, are specialized vehicles designed for transporting large quantities of milk from dairy farms to processing facilities. Their unique design ensures that milk remains fresh and safe for consumption, preserving its quality during transport. These vehicles play a crucial role in the dairy supply chain, which demands efficiency, cleanliness, and careful handling due to the perishable nature of milk. This article delves into the construction, functionality, and operational importance of milk trucks in the dairy industry.
The Purpose and Importance of Milk Trucks
Milk is a highly perishable product, prone to spoilage if not stored at appropriate temperatures. To maintain its freshness, milk must be swiftly transported from farms to processing plants, where it is pasteurized, homogenized, and processed into various dairy products. Milk trucks serve as a critical link in this chain, enabling a seamless transition from raw milk production to the creation of consumer-ready dairy products. Their design incorporates features to preserve the milk’s quality during transportation, ensuring it reaches its destination in peak condition.
In addition to the transportation function, milk trucks also play a role in milk collection. They often follow designated routes, stopping at multiple dairy farms to collect milk before returning to the processing facility. This makes milk trucks a highly efficient and essential element in the dairy industry’s logistics network.
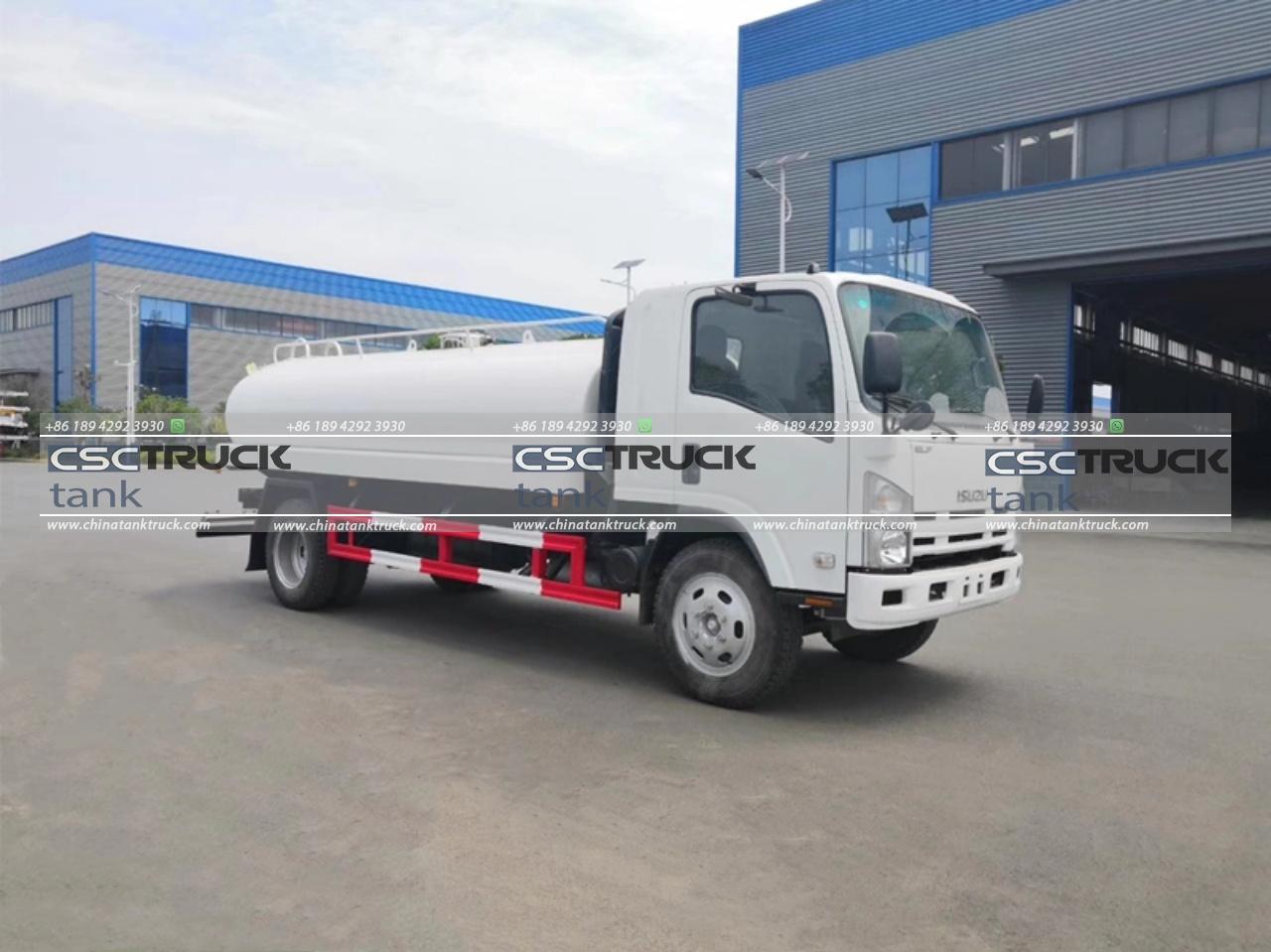
Design and Construction of Milk Trucks
Milk trucks are built with a unique focus on hygiene, insulation, and durability. The most prominent feature of a milk truck is its tank, which is typically made of high-grade stainless steel. Stainless steel is non-reactive, corrosion-resistant, and easy to clean, which are crucial characteristics for transporting consumable liquids. The tank design may vary slightly depending on the truck’s capacity and the terrain it will operate in, but it generally has a cylindrical shape to prevent milk from sloshing during movement, which can affect its stability and quality.
The tank is usually insulated to maintain the milk at a specific temperature, typically between 1-4°C (33-39°F). Insulation minimizes the temperature fluctuations that could otherwise lead to bacterial growth, ensuring that milk remains fresh. Advanced milk trucks may also include temperature control systems that allow drivers or operators to monitor and adjust the internal temperature in real-time.
Milk trucks also have specialized pumping systems to transfer milk into and out of the tank. These pumps are designed to handle the milk gently, minimizing agitation and the risk of introducing unwanted air, which could spoil the milk. Most modern milk trucks are also equipped with automated metering and recording systems, which document the quantity and quality of milk being transported. This data can be vital for tracking the source and quality of milk, aiding in quality control measures.
Types of Milk Trucks
Milk trucks come in different configurations, often designed to cater to specific routes, capacities, and operational needs. Here are a few common types:
1. Single Tank Trucks: These trucks have a single, large stainless steel tank. They are typically used for shorter routes or smaller-scale dairy operations. Their design is simpler, but they still incorporate insulation and temperature control to ensure milk freshness.
2. Multi-Compartment Trucks: These trucks feature multiple compartments within a single tank, allowing them to collect and transport milk from various farms without mixing batches. This is particularly useful for quality control and traceability, as each compartment can hold milk from a specific farm. Multi-compartment trucks are often used by larger dairy processing companies with multiple supplier farms.
3. Long-Distance Tankers: For extended transport routes, long-distance tankers are used. These milk trucks are often larger and equipped with additional insulation and more advanced temperature regulation systems. Long-distance tankers may also have larger capacities, allowing them to transport milk from rural dairy farms to urban processing facilities over great distances.
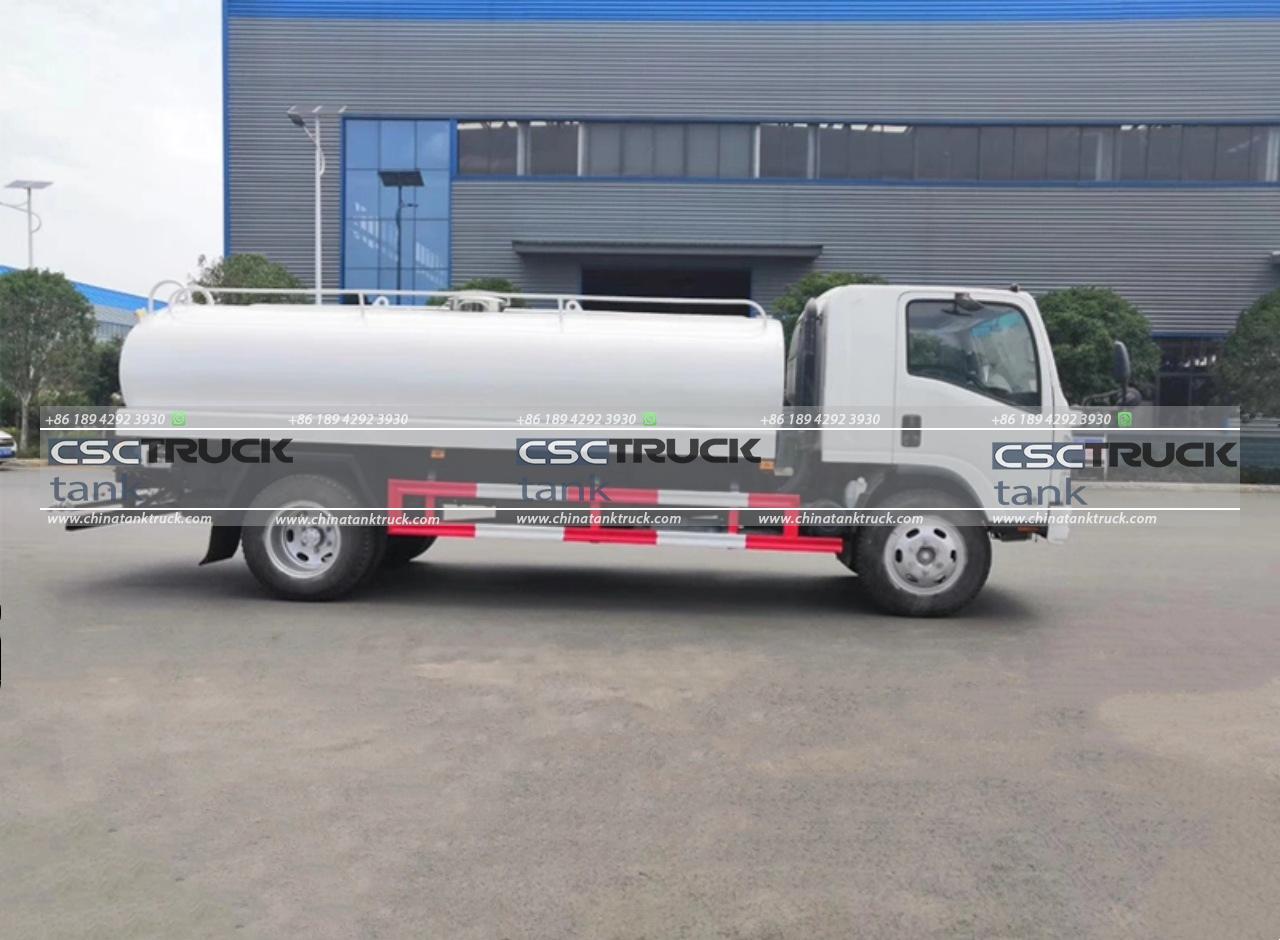
Key Components of a Milk Truck
The effectiveness of milk trucks depends on their various specialized components. Here’s a closer look at some of the essential parts:
1. Insulated Tank: The tank is usually double-walled and insulated with materials like foam or polyurethane. This insulation ensures that milk remains cool throughout the journey, minimizing spoilage risks.
2. Refrigeration System: While some milk trucks rely solely on insulation, others are equipped with active refrigeration systems, particularly for long-haul trips or warmer climates. These systems can regulate and maintain an optimal temperature within the tank, further preserving milk quality.
3. Pump System: The pump is a crucial element for loading and unloading milk. These pumps are designed to transfer milk at a steady, controlled rate, preventing air bubbles from forming. Gentle handling is necessary to preserve milk’s quality and consistency.
4. Sanitization Systems: Since milk is highly susceptible to contamination, milk trucks often include cleaning systems to sanitize tanks after each trip. Automated cleaning processes, such as Clean-in-Place (CIP) systems, are commonly used to ensure all equipment surfaces are thoroughly sanitized between loads, preventing bacterial growth and contamination.
5. Monitoring and Control Systems: Modern milk trucks are equipped with digital systems that track temperature, volume, and other important data. This monitoring provides real-time insights into the milk’s condition, allowing for immediate intervention if any issues arise.
Operational Aspects of Milk Trucks
Operating a milk truck requires adherence to strict hygiene and quality standards. Drivers and operators are often trained to handle milk with care, following protocols to prevent contamination. The loading process is meticulous; before transferring milk from the farm’s storage tanks, operators test the milk for quality and ensure that all hoses and connections are sanitized.
During transport, the driver monitors temperature and tank conditions, especially on longer routes. The unloading process is similarly controlled, with pumps and valves designed to minimize agitation as the milk is transferred to processing facility tanks.
Regulations surrounding milk trucks vary by country but generally include standards for sanitation, temperature control, and traceability. These regulations are enforced to protect public health, ensuring that consumers receive safe, high-quality dairy products.
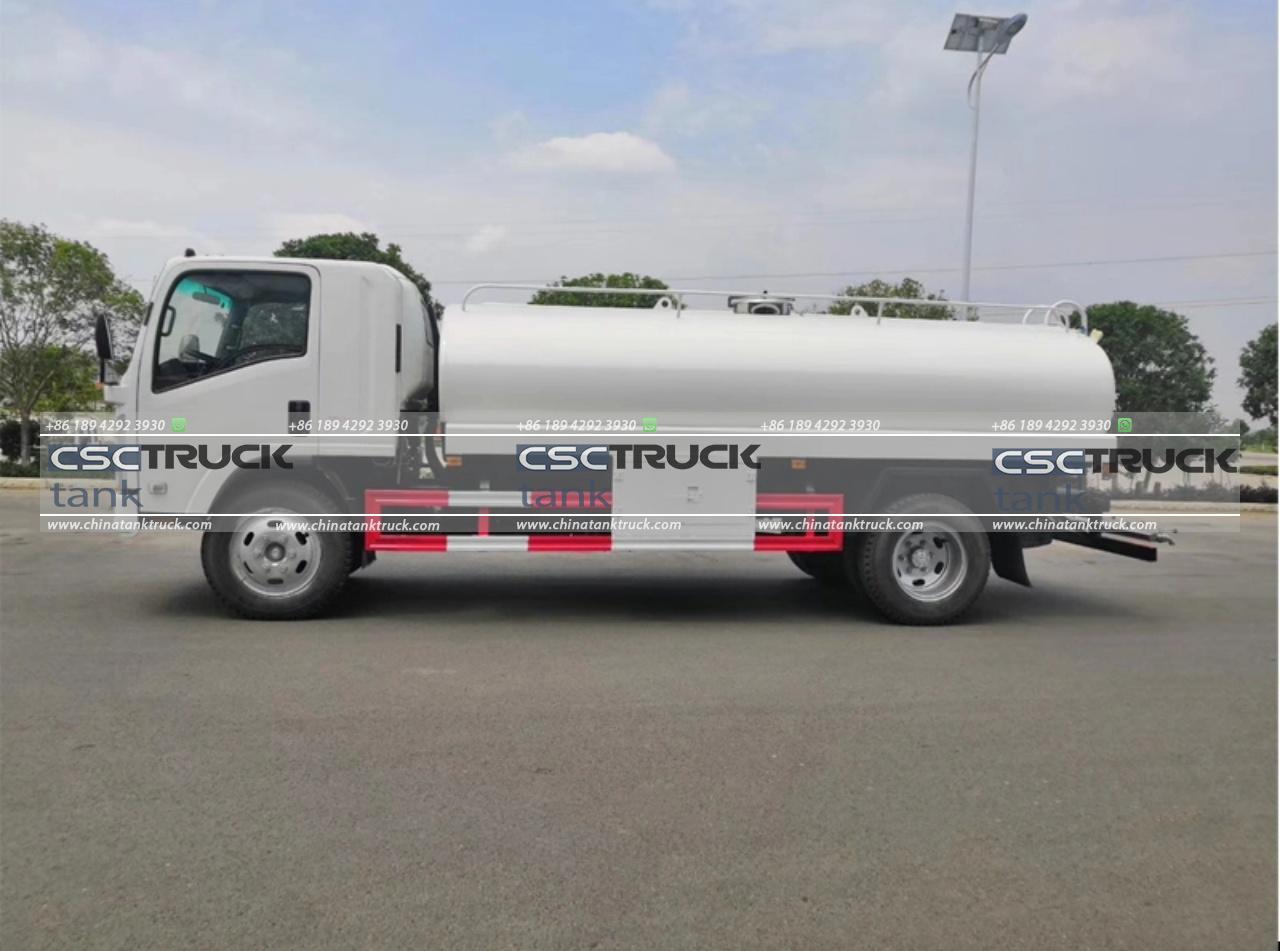
Innovations in Milk Truck Technology
Advancements in milk truck technology have introduced new features that enhance efficiency and quality control. Some of these innovations include:
– Telematics and GPS: Many milk trucks now come equipped with telematics and GPS systems that help optimize routes, reducing travel time and fuel consumption. These systems also allow dairy companies to track deliveries and manage logistics more efficiently.
– Automated Quality Testing: Advanced milk trucks are fitted with sensors that can conduct real-time quality assessments, measuring factors like temperature, pH, and fat content. This information is recorded and transmitted to the processing facility, enabling quick action if milk quality is compromised.
– Eco-Friendly Refrigeration: As sustainability becomes a focus, some milk trucks are adopting eco-friendly refrigerants and energy-efficient insulation materials. This reduces the environmental impact of milk transportation, aligning with dairy industry efforts to promote sustainable practices.
The Future of Milk Trucks
With growing consumer demand for fresh and organic dairy products, milk trucks are evolving to meet these needs. Future innovations may include even more advanced refrigeration systems, electric-powered trucks, and further automation. As technology advances, milk trucks will likely continue to improve in efficiency, quality assurance, and sustainability, ensuring that milk can be transported safely and responsibly from farms to tables worldwide.
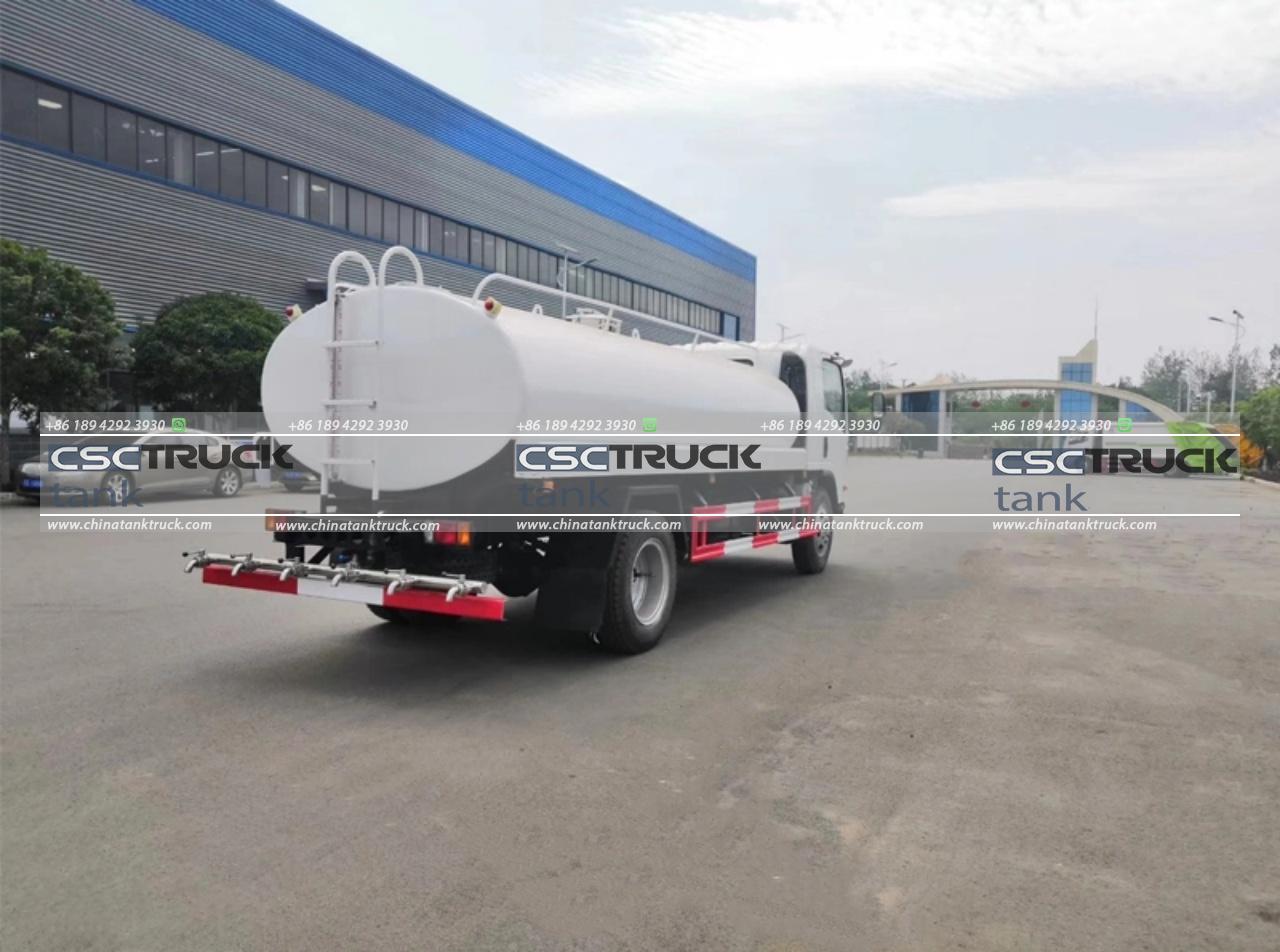
Conclusion
Milk trucks are a critical component of the dairy industry, facilitating the efficient and safe transport of milk from farms to processing plants. Their specialized design, from insulated tanks to monitoring systems, ensures that milk remains fresh and free from contamination. The intricate operations and strict hygiene protocols followed in milk truck transport underscore the industry’s commitment to delivering high-quality dairy products to consumers. As technology and sustainability practices evolve, milk trucks will continue to play an indispensable role in the dairy supply chain, adapting to meet new challenges and standards.