What are Milk Tankers Made Of?
Milk tankers play a crucial role in the dairy supply chain, transporting large volumes of milk from farms to processing facilities while maintaining its quality and freshness. The design and construction of milk tankers are highly specialized to preserve milk under optimal conditions during transport. In this article, we’ll explore the materials milk tankers are made of, the structural components involved, and the reasons behind these choices.
1. Material Choice: Stainless Steel
One of the primary materials used in milk tanker construction is stainless steel. This durable and corrosion-resistant metal is ideal for handling food-grade products due to its inert properties and ability to maintain the milk’s quality during transport. Stainless steel is preferred because:
– Corrosion Resistance: Milk is slightly acidic and can corrode materials over time. Stainless steel is naturally resistant to corrosion, even when exposed to acidic compounds, protecting the milk from contamination.
– Non-reactive Surface: Stainless steel is non-reactive, meaning it doesn’t leach chemicals or interact with milk, thus preserving the milk’s flavor and purity.
– Ease of Cleaning: The smooth, non-porous surface of stainless steel is easy to clean, which is essential to prevent bacterial growth and ensure milk remains uncontaminated.
– Durability: Stainless steel can withstand the rigors of long-distance travel and heavy loads, offering excellent longevity.
Most milk tankers use 304 or 316 stainless steel, both of which are types commonly employed in food processing and pharmaceutical industries due to their superior resistance to corrosion and overall durability.
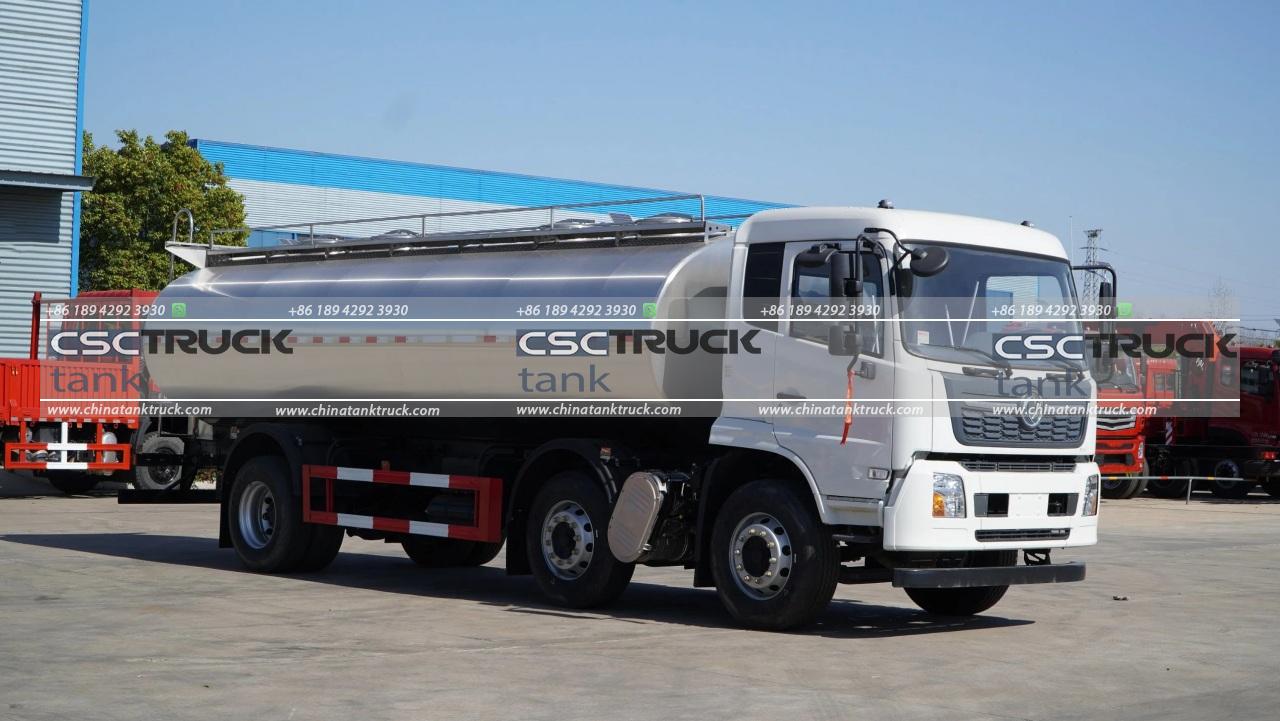
2. Insulation Materials
Milk tankers are also insulated to keep milk cool during transport. Temperature control is vital as it prevents the milk from spoiling. Milk tankers typically use insulation made from polyurethane foam sandwiched between layers of stainless steel. Here’s why polyurethane foam is commonly used:
– Thermal Insulation: Polyurethane foam has excellent thermal insulating properties, allowing it to maintain a constant temperature inside the tank for extended periods. This insulation can keep milk cool for several hours without the need for active refrigeration.
– Lightweight: Polyurethane is lightweight, which is important in tankers to keep the total weight manageable and minimize fuel consumption during transport.
– Durability and Moisture Resistance: Polyurethane is resistant to moisture, which helps maintain its insulating properties even in humid conditions.
3. Inner and Outer Tank Design
Milk tankers are often designed with an inner and outer tank structure. The inner tank holds the milk, while the outer tank houses the insulation material. This dual-layer design is essential to keep milk protected from environmental temperature fluctuations. Some key aspects of the inner and outer tank construction include:
– Inner Tank: This tank, in direct contact with milk, is made from high-quality stainless steel. It’s designed with smooth, rounded edges to minimize bacterial buildup and make cleaning easier. The inner tank’s capacity varies, depending on the tanker size, but can typically hold between 20,000 and 30,000 liters.
– Outer Tank: The outer layer of the tank adds another layer of protection against external temperature fluctuations and physical damage. This outer tank is also made from stainless steel or aluminum, making it both lightweight and strong.
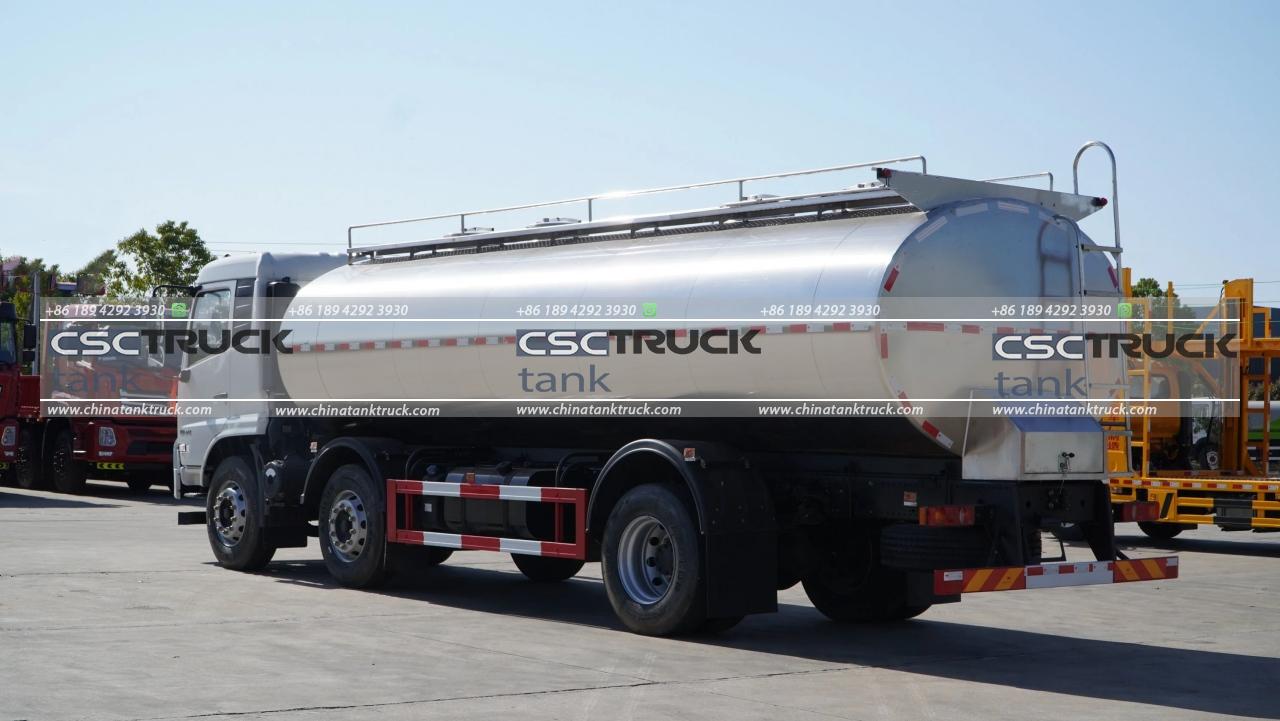
4. Components and Accessories
Milk tankers include several specialized components that help ensure safe and sanitary transport. Each component is carefully chosen and designed to meet strict hygiene standards:
– Valves and Pumps: Stainless steel valves and pumps are used to transfer milk in and out of the tanker. These are highly durable and resistant to wear and corrosion, preventing leaks and maintaining milk quality.
– Hoses and Couplings: The hoses that connect the tanker to loading and unloading stations are often made of food-grade materials like flexible stainless steel or high-quality, food-safe rubber. These hoses are easy to clean and resistant to bacterial growth.
– Temperature Monitoring Systems: Milk tankers are equipped with temperature sensors to ensure milk is transported within the ideal temperature range (typically between 3°C and 6°C). Monitoring systems alert the driver if the temperature deviates, allowing for corrective actions.
– Baffle Plates: Inside the tanker, baffle plates are installed to prevent milk from sloshing around during transport. These plates are often made of stainless steel and are strategically placed to allow for a smooth flow while also controlling the milk’s movement. This minimizes the risk of tanker instability during transport, enhancing driver safety.
– Cleaning Systems: Milk tankers are cleaned using CIP (Clean-in-Place) systems, a method that involves circulating cleaning solutions inside the tanker without needing to dismantle the equipment. The CIP system uses high-quality stainless steel spray balls that ensure cleaning agents reach all parts of the tanker.
5. The Role of Aluminum
While stainless steel is the primary material in milk tanker construction, aluminum is sometimes used for the outer structure to reduce overall weight. Aluminum is lightweight, corrosion-resistant, and more affordable than stainless steel, making it a suitable choice for tanker exteriors. However, aluminum is rarely used for parts that come into direct contact with milk due to its susceptibility to corrosion when exposed to acidic substances.
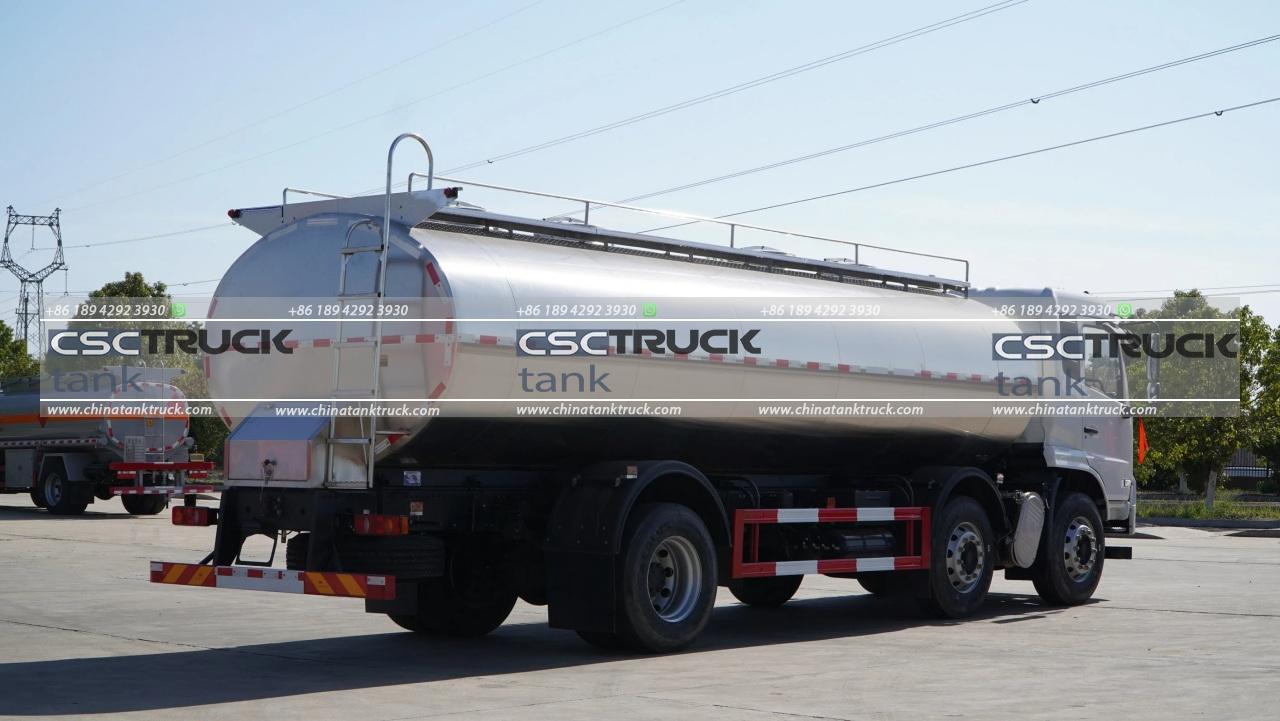
6. Regulatory Standards and Compliance
Milk tankers must adhere to strict food safety regulations to ensure milk quality remains uncompromised during transport. In many countries, food transport vehicles must be certified by regulatory agencies, such as the USDA in the United States or European Union regulations, that require:
– Hygienic Design Standards: Tankers must meet design standards to prevent contamination and facilitate cleaning.
– Temperature Control Requirements: Insulation and temperature monitoring systems must keep milk within the required temperature range.
– Construction Materials Standards: Materials used must be food-grade, durable, and non-reactive with dairy products.
These regulations mandate regular inspections, cleaning protocols, and maintenance procedures to ensure that milk reaches processing facilities in the best condition possible.
7. Environmental Considerations and Innovations
With a growing emphasis on sustainability, the dairy transport industry is exploring ways to make milk tankers more environmentally friendly. Some of the key innovations include:
– Lightweight Materials: Using lighter materials, such as advanced composites, reduces the tanker’s weight, lowering fuel consumption and emissions.
– Renewable Energy Systems: Some companies are integrating solar panels to power temperature monitoring and auxiliary systems, reducing dependency on fossil fuels.
– Advanced Insulation Technologies: Improved insulation materials and vacuum-insulated tanks provide even better temperature control with reduced material usage.
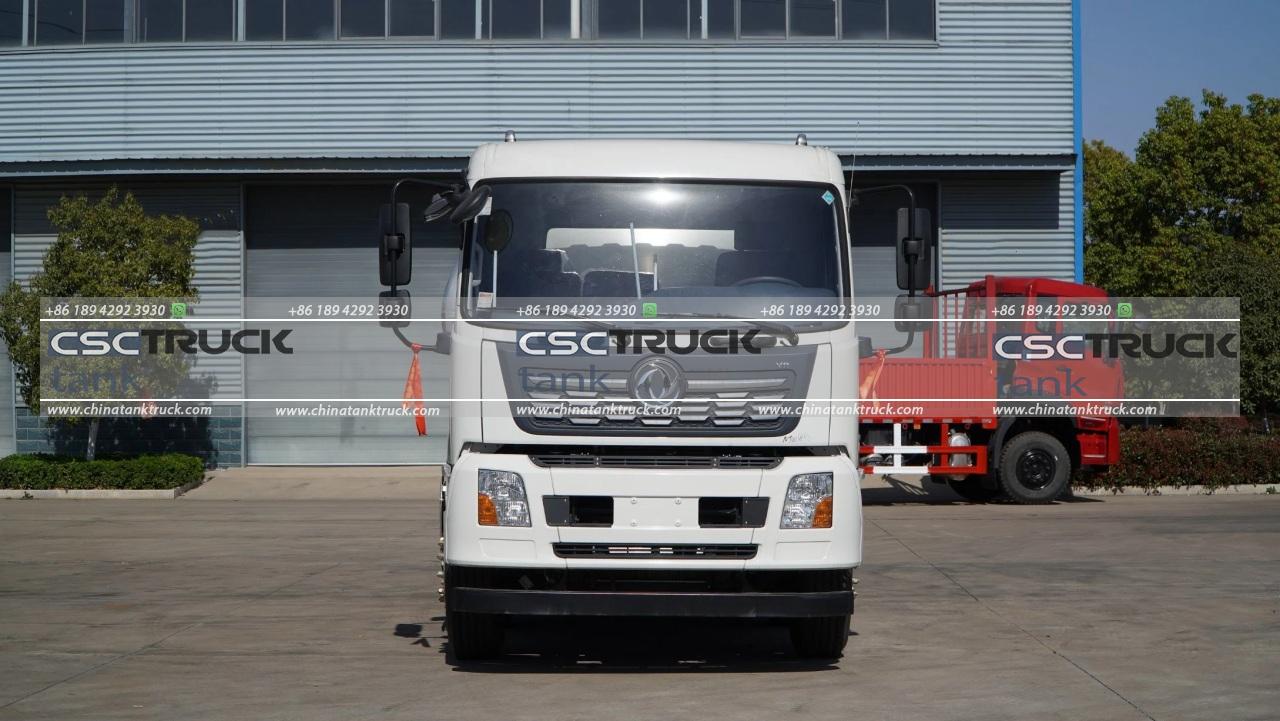
8. Why Tanker Construction Materials Matter
The choice of materials for milk tankers directly impacts milk quality, safety, and transport efficiency. Stainless steel, polyurethane, and other materials work together to ensure that milk reaches its destination fresh, free from contaminants, and within regulated temperature limits. The durability of stainless steel also minimizes long-term maintenance costs and ensures the longevity of these vehicles, making them reliable assets in the dairy industry.
Conclusion
Milk tankers are carefully constructed with food-safe, durable, and temperature-regulating materials to meet the demands of the dairy industry. Stainless steel’s non-reactive properties make it the material of choice for milk transport, while polyurethane insulation and advanced technology help maintain milk’s freshness during long trips. As environmental considerations become increasingly important, we may see continued innovation in milk tanker design, further refining the balance between safety, efficiency, and sustainability. The materials and design choices behind milk tankers underscore the care taken to maintain milk’s quality as it travels from farms to consumers, making these tankers an essential part of the dairy industry’s infrastructure.
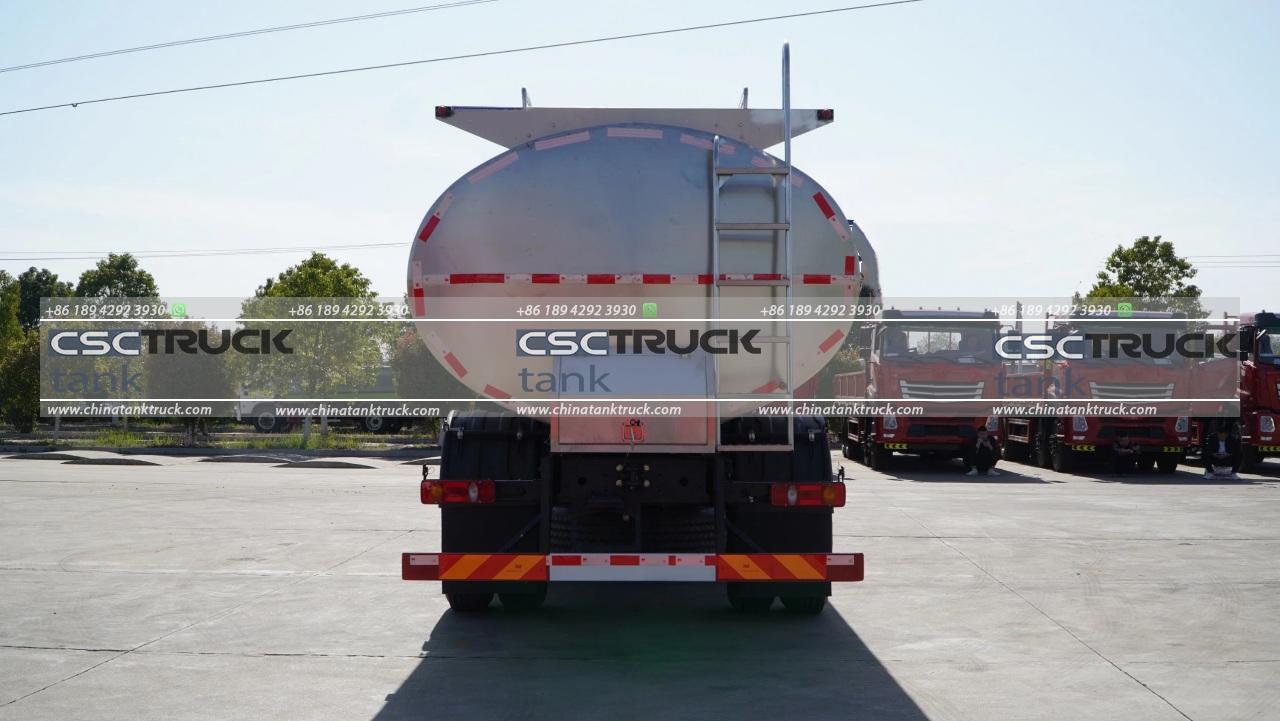