What are the Four Types of Tanks in a Chemical Tanker?
Chemical tankers are specialized vessels designed for the safe and efficient transport of liquid chemicals in bulk. These ships are critical to the global economy as they transport a wide range of chemicals used in industries like pharmaceuticals, agriculture, oil refining, and plastics manufacturing. To safely carry such potentially hazardous materials, chemical tankers are built with advanced safety and containment measures, especially in terms of the tank types they use. The four primary types of tanks in a chemical tanker are stainless steel tanks, coated tanks, independent tanks, and integral tanks. Each type of tank has unique characteristics that determine its suitability for different types of cargo. In this article, we’ll explore the features, advantages, and disadvantages of each tank type and explain why different tank types are used depending on the cargo’s properties.
1. Stainless Steel Tanks
Characteristics
Stainless steel tanks are considered the gold standard in chemical tanker storage due to their excellent corrosion resistance, durability, and versatility. These tanks are typically constructed from high-grade stainless steel alloys, which provide superior resistance to both chemical corrosion and physical abrasion. Stainless steel tanks are suitable for carrying a wide range of aggressive chemicals, including acids, alkalis, and certain solvents that may react with other materials.
Stainless steel tanks are known for their smooth, easy-to-clean surfaces. This characteristic is particularly important when dealing with chemicals that must not mix, as cross-contamination can be a significant hazard. The tanks can be washed out relatively easily between different cargoes, allowing tankers to switch between carrying various substances with minimal risk of contamination.
Advantages
– Corrosion resistance: Stainless steel’s primary advantage is its ability to resist corrosion. This makes it ideal for carrying highly reactive chemicals like sulfuric acid, nitric acid, or hydrochloric acid, which would quickly degrade other tank materials.
– Durability: Stainless steel tanks have a long lifespan, resisting wear and tear even when exposed to corrosive and abrasive substances.
– Hygiene and ease of cleaning: These tanks can be easily cleaned between cargoes, reducing the risk of cross-contamination.
Disadvantages
– Cost: The main drawback of stainless steel tanks is their high cost. Stainless steel is more expensive than other materials used for tanks, such as mild steel or aluminum.
– Weight: Stainless steel tanks are also relatively heavy, which may reduce the overall cargo capacity of the vessel due to weight limitations.
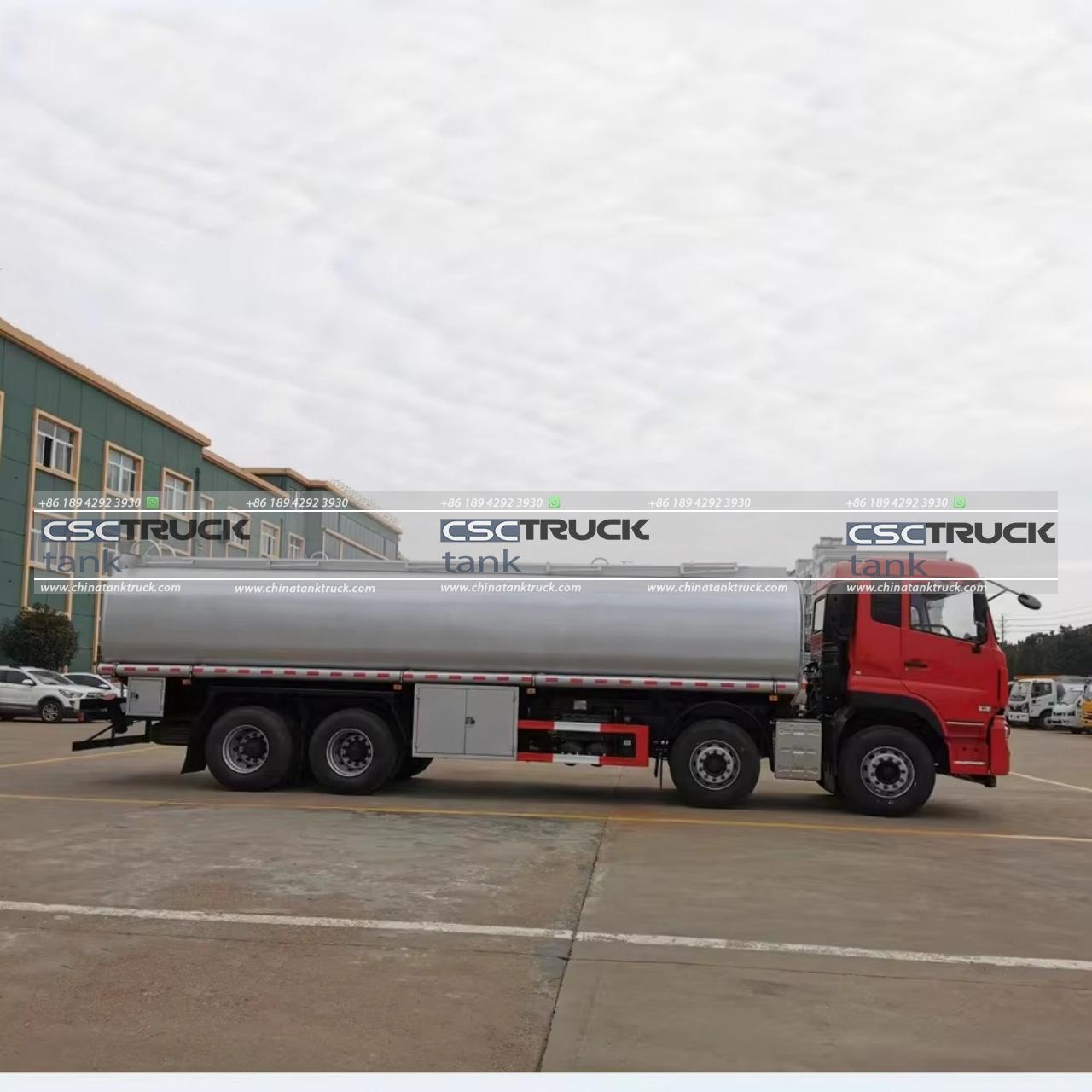
2. Coated Tanks
Characteristics
Coated tanks are constructed from a less expensive metal, such as mild steel, and then coated with a specialized layer that protects the chemical cargo. These coatings are typically made from epoxy or phenolic resins, which are designed to prevent the corrosive effects of chemicals on the tank’s structure. Different coatings are selected based on the type of cargo the tanker is intended to carry.
Coated tanks are widely used because they offer a cost-effective solution for transporting less aggressive chemicals. However, the coating must be carefully maintained because any damage to the coating could expose the underlying metal to corrosion, leading to structural damage or contamination of the cargo.
Advantages
– Cost-effective: Coated tanks are generally less expensive than stainless steel tanks, making them a popular choice for transporting less corrosive chemicals.
– Flexibility: The coatings can be chosen and applied depending on the specific cargo requirements, making these tanks adaptable for carrying a wide range of chemicals.
– Weight: Coated tanks tend to be lighter than stainless steel tanks, increasing the vessel’s cargo capacity.
Disadvantages
– Coating maintenance: The coating is subject to wear and tear, especially when loading or unloading abrasive materials. Regular inspection and maintenance are crucial to ensure the coating remains intact.
– Limited lifespan: The coatings on these tanks degrade over time, especially if the tank frequently carries corrosive chemicals or abrasive substances, requiring periodic re-coating or replacement.
3. Independent Tanks
Characteristics
Independent tanks are self-contained structures that are not part of the ship’s hull. These tanks are typically used for transporting liquefied gases, such as ammonia, propane, and butane, or highly toxic chemicals that require extra safety precautions. Independent tanks are often made of materials designed to withstand extreme temperatures and pressure, such as aluminum alloys, stainless steel, or specialized polymers.
There are several types of independent tanks, such as Type A, Type B, and Type C, each defined by international maritime regulations based on their structural design, pressure capabilities, and insulation requirements. Independent tanks are typically spherical or cylindrical to distribute the internal pressure more evenly, reducing the risk of structural failure.
Advantages
– Safety: Independent tanks provide an additional layer of protection, as they are not integrated into the ship’s hull. In the event of a hull breach, the cargo remains contained within the tank.
– Pressure resistance: These tanks are designed to handle higher pressures, making them ideal for transporting liquefied gases and other pressurized chemicals.
– Temperature control: Independent tanks often include insulation or other temperature control mechanisms, allowing for the transport of chemicals that must be kept at very low or high temperatures.
Disadvantages
– Cost and complexity: Independent tanks are often more complex and expensive to install and maintain, particularly when dealing with cargoes that require specific temperature or pressure conditions.
– Space inefficiency: Because these tanks are not integrated into the ship’s hull, they may take up more space, reducing the vessel’s overall cargo capacity.
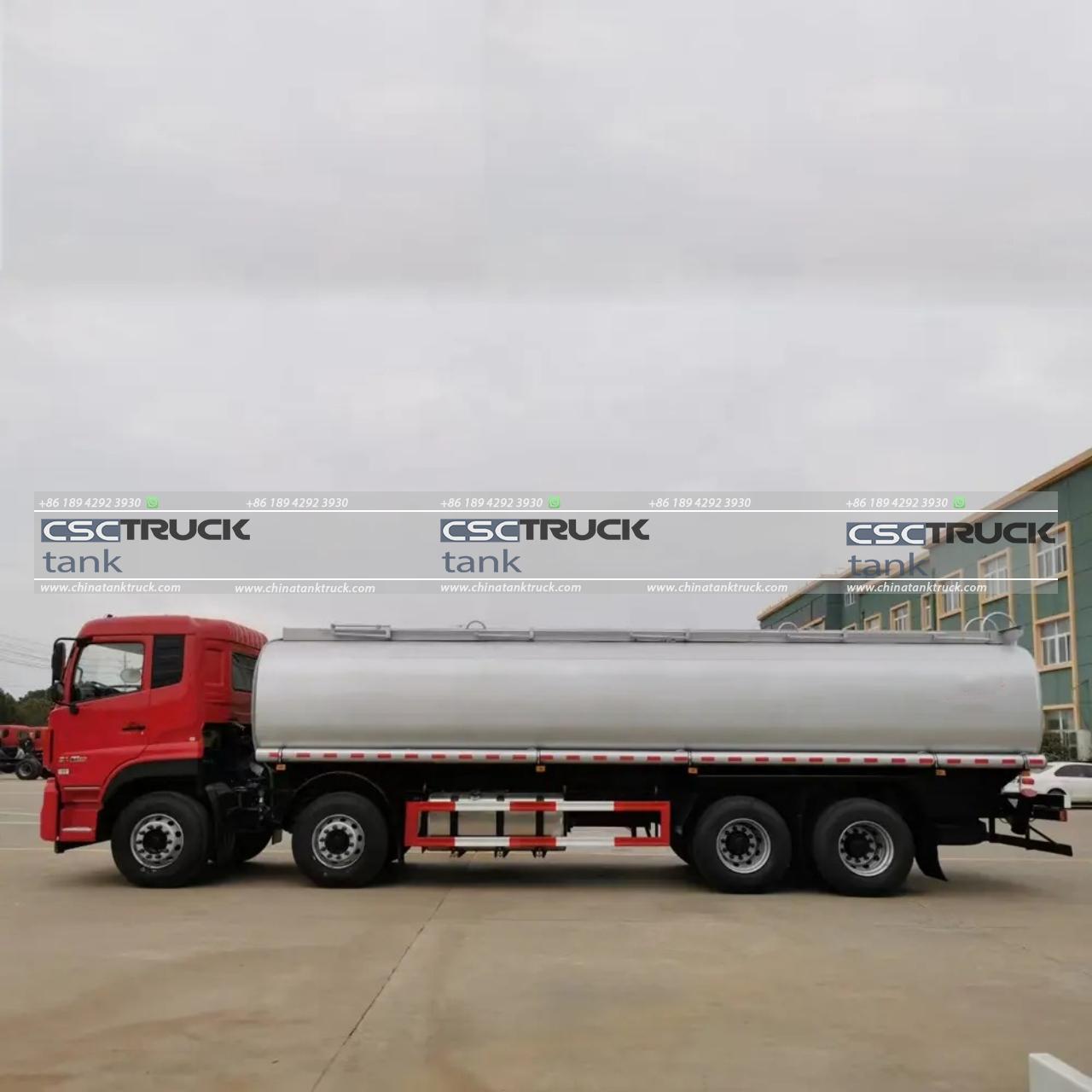
4. Integral Tanks
Characteristics
Integral tanks are directly built into the ship’s hull and form part of the ship’s structural framework. These tanks are usually made from the same material as the ship’s hull and are commonly used for transporting bulk chemicals that do not require specialized containment measures. The main advantage of integral tanks is that they maximize the available cargo space on the ship, allowing for larger quantities of chemicals to be transported.
Integral tanks are more commonly used in oil and product tankers, but some chemical tankers are designed with integral tanks for transporting chemicals that are less hazardous or reactive. However, the lack of separation between the tank and the hull means that any damage to the hull could result in a leak.
Advantages
– Cargo capacity: Integral tanks allow for the maximum use of the ship’s volume, providing greater cargo capacity compared to independent tanks.
– Cost-effective: Since these tanks are part of the ship’s structure, they are less expensive to build than independent tanks or stainless steel tanks.
Disadvantages
– Risk of contamination: Because the tanks are part of the hull, any damage to the ship’s structure can lead to contamination or loss of cargo.
– Limited chemical compatibility: Integral tanks are less versatile than stainless steel or coated tanks because they cannot be easily modified to accommodate a wide range of chemicals.
Conclusion
Each of the 4 tank types in a chemical tanker—stainless steel tanks, coated tanks, independent tanks, and integral tanks—offers unique advantages and disadvantages depending on the chemical being transported. Stainless steel tanks are the most versatile and durable but come at a high cost. Coated tanks provide a more economical solution for less corrosive chemicals but require regular maintenance. Independent tanks offer the highest levels of safety for hazardous cargo but are space-inefficient. Lastly, integral tanks maximize cargo capacity but are limited in their compatibility with certain chemicals.
Choosing the right type of tank for a chemical tanker depends on a careful assessment of the chemical properties, safety requirements, and economic considerations involved in the cargo’s transport. The design and operation of chemical tankers will continue to evolve as new technologies and materials are developed to meet the growing demand for safer and more efficient chemical transport.
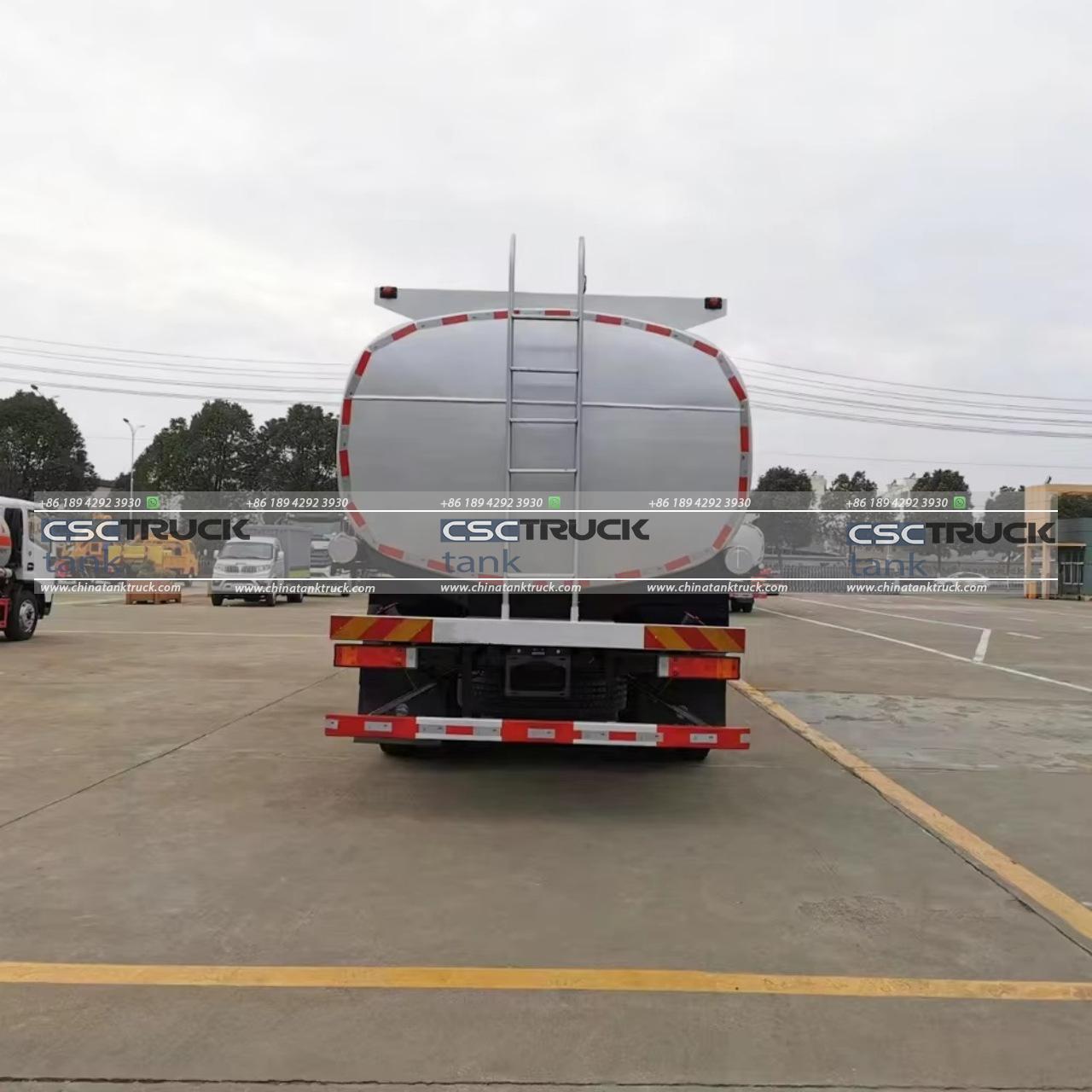