What is an Example of a Milk Run in Logistics?
Logistics is a critical function in supply chain management, ensuring that goods are moved from one location to another efficiently and cost-effectively. One of the strategies employed to optimize this process is the “Milk Run.” A Milk Run in logistics refers to a distribution method where a single vehicle collects or delivers goods from multiple locations before returning to its starting point. The term originates from the traditional milk delivery service, where a milkman would deliver fresh milk to multiple homes on a single route.
Understanding the Concept of Milk Run
The Milk Run approach contrasts with direct shipment, where goods are transported from one location to another without any intermediate stops. In a Milk Run, the vehicle follows a planned route, stopping at various points to either collect or drop off goods. This method is highly efficient for companies looking to minimize transportation costs, reduce inventory levels, and improve delivery times.
A Milk Run can be inbound, where raw materials or components are collected from various suppliers and delivered to a manufacturing facility, or outbound, where finished products are delivered to multiple customers or distribution centers. This system is especially beneficial in industries where just-in-time (JIT) production is critical, as it ensures a steady flow of materials without the need for excessive inventory.
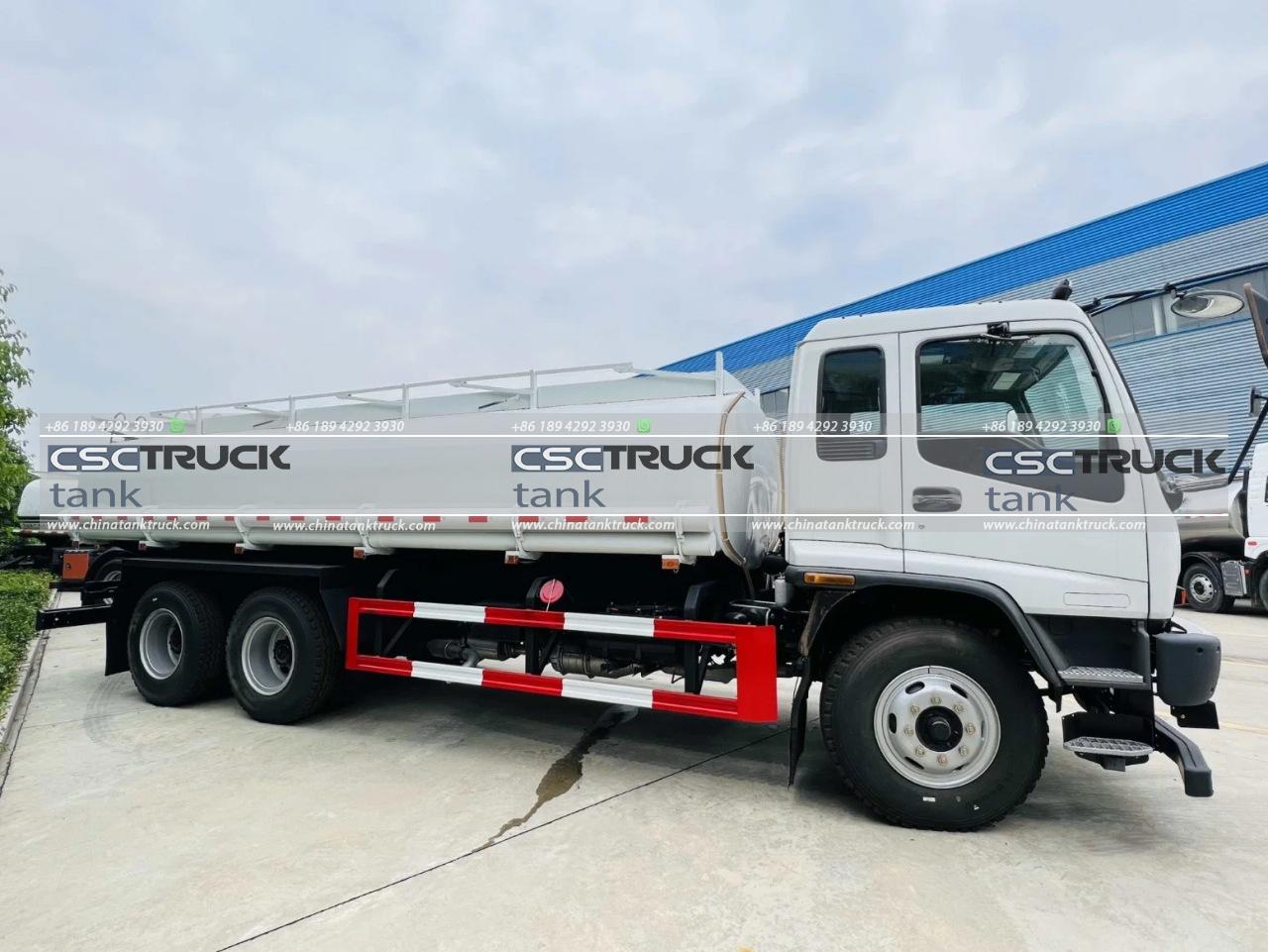
Example of a Milk Run in Logistics
To illustrate the concept, let’s consider an example of a Milk Run in the automotive industry, where a car manufacturer needs to receive various components from different suppliers to assemble vehicles.
Scenario:
A car manufacturing plant requires specific parts to assemble its vehicles. These parts include engines, tires, and electronic systems. The plant is located in a central region, with suppliers scattered across different areas within a 100-mile radius. Instead of each supplier sending their parts individually to the plant, which could result in higher transportation costs and increased lead times, the manufacturer decides to implement a Milk Run.
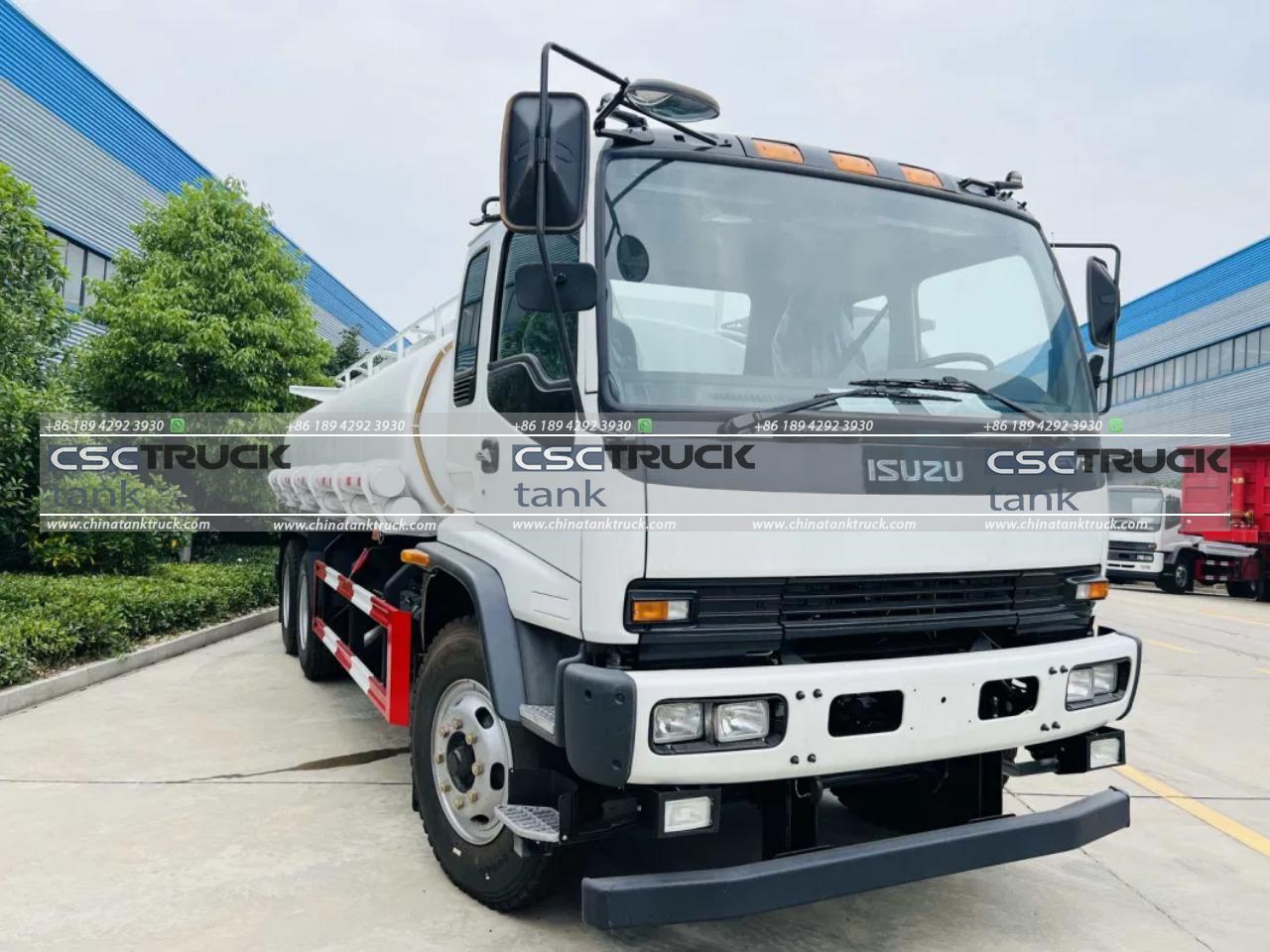
Step-by-Step Breakdown:
1. Route Planning:
  The logistics team at the car manufacturing plant plans a route that the delivery truck will follow. The route is designed to minimize the distance traveled and maximize the load capacity of the truck. The plan is to pick up the engines first, followed by the electronic systems, and finally, the tires.
2. Supplier Coordination:
  The logistics team coordinates with the suppliers to ensure that the parts are ready for pickup at specific times. The suppliers are informed about the arrival times of the truck, and they prepare the goods accordingly to avoid any delays.
3. First Stop – Engine Supplier:
  The truck departs from the manufacturing plant and heads to the engine supplier, which is located 30 miles away. Upon arrival, the truck is loaded with the required number of engines. The logistics team ensures that the loading process is quick and efficient to keep the schedule on track.
4. Second Stop – Electronics Supplier:
  After picking up the engines, the truck travels another 20 miles to the electronics supplier. Here, the truck is loaded with the necessary electronic systems. Since the truck is already partially loaded with engines, careful planning is required to ensure that the remaining space is utilized effectively.
5. Final Stop – Tire Supplier:
  The last stop is at the tire supplier, located 50 miles from the electronics supplier. The truck is loaded with the required tires, filling the remaining space in the truck. Once all the parts are collected, the truck returns to the manufacturing plant.
6. Delivery to the Plant:
  Upon arrival at the plant, the parts are unloaded and moved directly to the production line. The manufacturing process can now proceed without any delays, as all necessary components are available.
Benefits of the Milk Run:
– Cost Savings:Â By using a single truck to pick up parts from multiple suppliers, the manufacturer reduces transportation costs. Instead of paying for multiple shipments, the cost is consolidated into one trip.
– Reduced Lead Times:Â The Milk Run approach ensures that all necessary parts arrive at the plant simultaneously, reducing lead times and preventing production delays.
– Inventory Reduction:Â Since the Milk Run allows for frequent and timely deliveries, the manufacturer can maintain lower inventory levels, reducing the need for excessive storage space and lowering inventory holding costs.
– Environmental Impact: Fewer trips mean less fuel consumption and lower carbon emissions, contributing to the company’s sustainability goals.
– Improved Supplier Relationships:Â The coordinated effort between the manufacturer and suppliers fosters better communication and collaboration, leading to stronger relationships and more reliable supply chains.
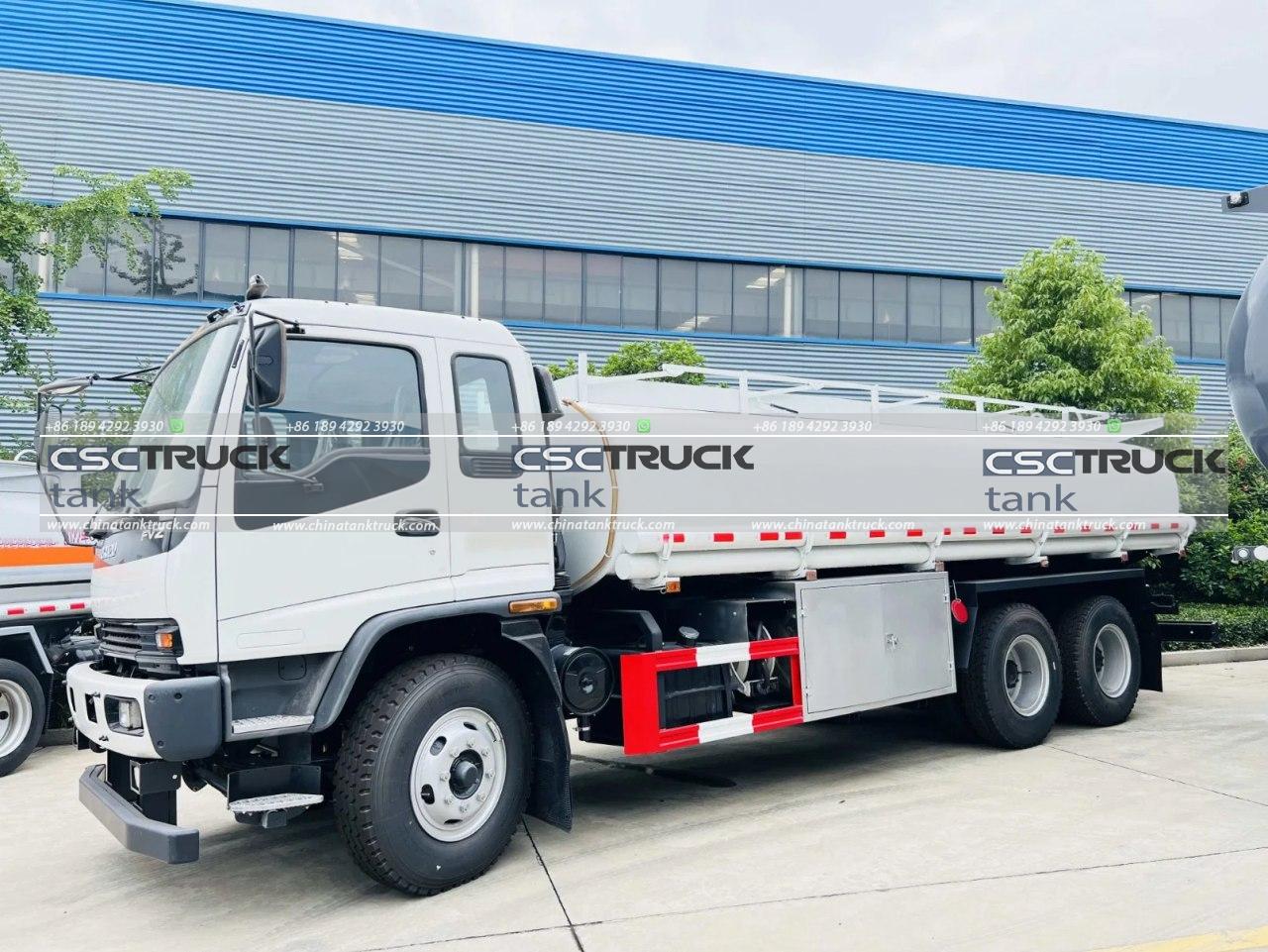
Applications of Milk Run in Different Industries
While the example above focuses on the automotive industry, the Milk Run approach is applicable across various sectors:
1. Retail:Â In the retail industry, a Milk Run can be used to distribute products from a central warehouse to multiple stores. This method ensures that each store receives the right amount of stock without overloading any single location.
2. Food and Beverage:Â In the food and beverage industry, a Milk Run can be used to collect raw materials like fruits, vegetables, and dairy products from different farms and deliver them to a processing facility.
3. Electronics:Â In electronics manufacturing, components from various suppliers can be picked up through a Milk Run and delivered to the assembly plant, ensuring that production schedules are met.
4. Healthcare:Â Hospitals and clinics can use a Milk Run system to collect medical supplies from various suppliers and distribute them to different departments or satellite locations.
Challenges of Implementing a Milk Run
While the Milk Run offers numerous benefits, it also comes with certain challenges:
– Complex Route Planning:Â Planning an efficient route requires careful consideration of factors like distance, traffic, and supplier locations. Any miscalculation can lead to delays and increased costs.
– Coordination with Suppliers: Effective communication and coordination with suppliers are crucial. Any delay at one supplier’s location can disrupt the entire schedule.
– Load Optimization:Â Ensuring that the truck is loaded efficiently at each stop is essential. Poor load planning can result in wasted space or the need for additional trips.
– Flexibility:Â The Milk Run approach requires a certain level of flexibility. If a supplier cannot meet the scheduled pickup time, the logistics team must quickly adapt to avoid disruptions.
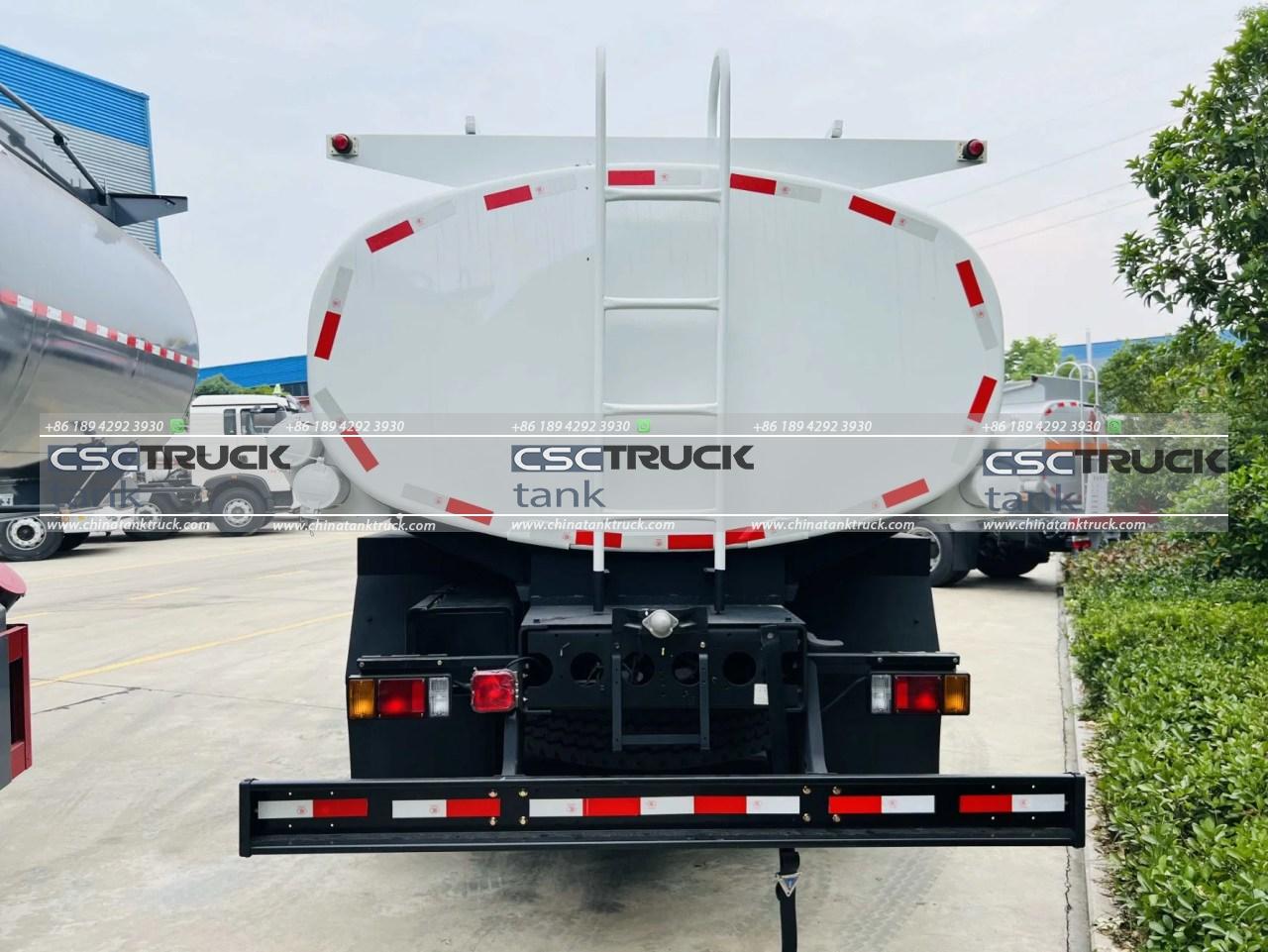
Conclusion
The Milk Run is an effective logistics strategy that can significantly improve supply chain efficiency. By consolidating deliveries and optimizing routes, companies can reduce costs, improve delivery times, and maintain lower inventory levels. While it requires careful planning and coordination, the benefits often outweigh the challenges, making the Milk Run a valuable tool in modern logistics. As supply chains continue to evolve, the Milk Run approach is likely to play an increasingly important role in helping companies stay competitive in a fast-paced global market.